An important point in the start of production is the preparation of the enterprise for the release of new products. To this end, in each country, systems have been developed to prepare enterprises for the launch of new production lines and the compliance of ongoing technological changes with certain established standards.
What is the technological preparation of production at the enterprise (CCI)?
This is a set of measures that ensures the readiness of the enterprise in terms of technology to release new products. These are technological, organizational, economic, scientific and design work on launching production of new products or mastering the latest technologies.
Technical and technological preparation of production are very important links when launching a new product line. At the same time, the CCI is an integral part of technical training.
At this stage, the enterprise management determines which technologies and resources will produce new products, and also calculates the cost of one unit of production.
The result of the CCI is expressed in the readiness of the enterprise to produce products of a certain quality on time, in the required volume and at certain costs. The set of measures and their number depends on the technical and technological equipment of the company, the complexity and purpose of the final products. Technological readiness is a complete set of documents and technical equipment that are required for the release of new products.
Work with CCI documentation
Work with the CCI documentation takes place in 3 stages: the development of the terms of reference, technical and working draft.
When developing the terms of reference, it is necessary to analyze the existing organizational and technical means, to develop ideas and suggestions on the organization, planning and process control procedures.
A technical project is a general phased scheme for the preparation of the production process, the readiness of all services for launching new products into production, the development of the main provisions for the organization of work, bringing documentation to general standards (document forms), the development of technical specifications for the automation of the main components of the CCI.
A working draft is an informational component of the CCI: job descriptions, general provisions, documents and standardization of production processes, preparation and putting into operation of documentation for solving computer problems.
Technological processes at the enterprise (TP)
TP is a set of methods for manufacturing a product by changing its design, condition, properties, shape, size, taken for the use of raw materials, materials and / or blanks.
Preparation for the CCI is carried out in two directions: as part of the introduction of new products and with the aim of improving the existing production process, which will not be associated with changes in the design of manufactured products. In each direction, their tasks are solved and a certain list of works is carried out. It all depends on the products and the selected production process.
To develop technological processes, the company has a special service - the department of the chief technologist. These works are carried out for the manufacture or repair of those products that have already passed the test for manufacturability.
Manufacturability
This is a series of product design parameters that are tested for the possibility of optimizing labor costs, materials and time during the CCI, production and use of the product, its repair compared to similar indicators of the same type of product while maintaining the specified quality parameters in certain conditions of production, use and repair.
Information on the level of manufacturability is necessary in order to optimize decisions made at the following stages:
- development of design documentation;
- definition of plans for the start of production of a particular product;
- CCI analysis;
- development of an action plan to improve the level of manufacturability and production efficiency and operation of products.
Among the indicators that are involved in assessing the manufacturability of the design include:
- labor input;
- specific material consumption;
- cost price;
- terms of technical support.
When evaluating manufacturability, it is recommended to use a minimally sufficient set of indicators. The evaluation methodology and indicators, as well as quantitative results, are determined depending on the product:
- her kind;
- degree of novelty;
- complexity and production conditions;
- maintenance and repair;
- planned volumes of manufactured batches;
- prospects for the future;
- type of production;
- level of development of the production process of the product design.
Checking the design of manufactured products for manufacturability should answer a number of the following questions:
- Decrease in the prime cost and labor costs for release.
- Reduced cost and maintenance costs.
- Reducing material consumption of production - the amount of metal, fuel, energy resources expended, as well as installation and repair on the territory of the customer.
Cost reduction and labor costs
This is facilitated by the introduction of new products into serial production by standardizing and unifying production and other processes, reducing the range of structural components and materials used, introducing highly efficient and low-waste technologies, standardizing the organization’s technical equipment, and developing the most optimal level of mechanization and automation.
Material consumption reduction
Work to reduce the material consumption of manufactured products can be divided into the following components:
- the use of the most suitable grades and types of materials, options for obtaining the most effective blanks, ways to increase the strength of the individual components of the structure;
- the use of modern and most effective solutions that are aimed at increasing the resource of manufactured products, as well as the use of non-waste and / or low-waste technological processes;
- the use of a reasonable layout of products in order to reduce costs spent on the production of materials.
During the CCI, two types of manufacturability of the structure are distinguished:
- Production - designed to reduce the time and material costs of preparation, and the time frame of the production cycle.
- Operational - is necessary to reduce time and material costs for maintenance and repair of products.
Evaluation of the technological design of the finished product takes place according to two types of characteristics: qualitative and quantitative.
CCI goal
Technologies and their processes are developed for the production of each specific product, and for the manufacture of products that have become traditional for the organization. The purpose of technological preparation of production is to increase the technical level of organization and goods, reduce production costs, and improve working conditions for personnel. CCI is used as part of measures to protect the environment from the effects of production.
CCI objectives
It is necessary to perform the following tasks of technological preparation of production:
- To analyze the manufacturability of new manufactured products.
- To analyze the existing technologies, equipment fleet, production lines and production capacity at the enterprise.
- To analyze the processes used and configure existing ones or develop new technologies for the production of products.
- Introduce non-standard organization equipment, tools.
- Define standards for various types of material and technical resources.
- Design and implement, if necessary, new production sites.
- Conclude agreements with new suppliers of necessary resources.
- Define standards for production processes.
- To develop plans for the release of new products, as well as for the operational management of the CCI.
CCI stages
There are 3 main stages of technological preparation of production:
- Development of a prototype production program.
- Preparation of the enterprise for the release of a pilot batch.
- Preparation and maintenance of new products on an industrial scale.
Any CCI begins with the definition of route technology - that is, the sequence of operations performed and the introduction of work on the workshops for each specific group of equipment. Along with this, there is a selection of tools and technical equipment, calculations of temporary standards and the establishment of the category of work to determine the specialty and level of qualification of the staff.
In individual and small-scale production, as well as in enterprises with relatively simple methods of technology development, the CCI is limited to the development of route technology (MT). Large enterprises are also working on operational ones.
When considering MT options, the most optimal one is selected by comparing all indicators and comparing the cost of the final product, the work carried out at different stages of production and maintenance. That is, typical technological processes are determined, which, in turn, are designed to reduce the number of technological operations and establish unified methods of production, processing of identical products, which leads to cost reduction.
To develop new processes at the enterprise, it is necessary to go through a series of the following stages, which will form the basis for the organization of technological preparation of production:
- determine the technological route of processing products of a certain group;
- choose a surgical process (if necessary);
- identify and implement methods of processing individual components of products.
At the CCI, it is also necessary to carry out the elaboration of projects, to produce and adjust equipment, technical equipment. This is a rather complicated, labor and resource consuming job. At large enterprises with technologically complex production, the launch of a new product is accompanied by reconstruction and re-equipment with new equipment and technologies.
Carrying out the CCI, it is necessary to take into account the material and organizational readiness of the company for a new type of product. Material preparation includes the consolidation of resources, the acquisition and launch of new equipment and production lines, the production and / or acquisition of new tools and other technical equipment, as well as raw materials, materials, blanks and much more. Simply put, the material and technical equipment of the organization with all the necessary resources to start production of new products. Organizational preparation of the enterprise is an increase in the efficiency of labor and production processes, as well as adaptation of all services to the release of new products, the use of technologies and equipment.
Ectp
In the structure of standards for technological preparation of production, it is worth noting the interstate standards of the CCI, such as:
- SRPP - a system for the development and putting products into production.
- ESKD - a single system of design documentation.
- ESTD is a unified system of technological documentation.
- CAD - a computer-aided design system.
A special place among these CCI standards is given to the standardization of technical documentation.
Management of the technological preparation of production takes place precisely by following the developed, generalized uniform standards and rules, as well as other regulatory documents.
Effective standardization is achieved by the following methods:
- Reduction and refusal of expenses on re-issuance of documents in the process of their transfer to other organizations and enterprises.
- Reduction of textual and graphic documents to simpler forms, reduction of costs for their preparation and use corresponding to this procedure.
- The introduction of unified documents and workflow, the expansion of their use in the design process, development of new technological solutions, preparation and implementation of equipment, tools, technical equipment.
- Modern methods of accounting for computer technology, which is used in the manufacture and processing of the entire flow of documents of the organization.
- Work on improving the quality of development of technical documentation.
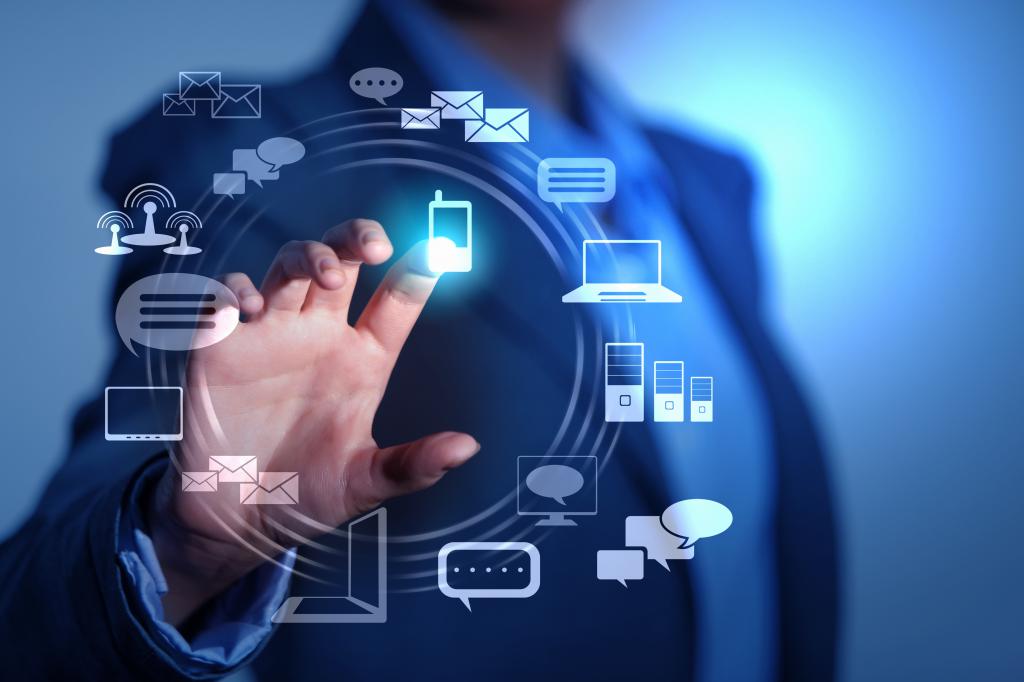
The unified system of technological preparation of production (ESTPP) is a system of organization and management of the CCI process, defined by state standards, which provides for the use of modern technologies, technological equipment with necessary equipment, means of mechanization and automation of production processes, managerial and engineering processes.
ESTPP is a generally accepted system-forming approach for enterprises to determine the methods and means of CCIs, their application, as well as to the development of finished products technology in the shortest possible time, with small material and labor costs at each stage, including test samples. This leads to the creation of flexible production, which will continuously improve technical processes or quickly change them to the release of new types of products.
The complex of a unified system of technological preparation of production is divided into 5 components:
- Group 1 (preparatory): general standards, terms, basic requirements, procedure for evaluating the CCI.
- Group 2: enterprise standards - includes enterprise rules and rules for managing the CCI, stages of documentation development, formation of organizational structures for the enterprise, automation, rules for organizing the economic and organizational activities of the enterprise.
- Group 3: product standards - determine the manufacturability of the manufactured product as a whole, by type of products, development stages, indicators of manufacturability of production and the procedure for choosing these indicators, the procedure for implementing control of design documentation.
- Group 4: standards of production processes - the procedure for the development and implementation of production technologies, means of equipping production with technologies, the selection and implementation of equipment, controls, processes of mechanization and automation of production.
- Group 5: standards for mechanization and automation - the rules for the use of technical means and mechanization / automation of ongoing work, solving new problems, information, mathematical and technical equipment, determining objects and the queue for implementing automation and solving tasks.