Do-it-yourself blade for a walk-behind tractor can well be made by any home craftsman who has some experience in working with metal. With the help of this add-on, you can regularly and easily rid the territory of snow drifts. This applies not only to private use, as the device will be able to master a very impressive amount of work. But such manipulations are quite inexpensive, which cannot be said about factory-made equipment.
The need to use a blade
This solution eliminates the need to use a shovel, which is a rather time-consuming task. Before proceeding with the manufacture of an addition to an existing walk-behind tractor, it is necessary to consider the design features of a snow blower, which consists of three parts, namely: a mount, a snow shovel and a device for adjusting the angle of rotation. The mounting unit is responsible for fixing the shovel on the tractor frame. Having made a dump for the walk-behind tractor with your own hands, you can do such work on the site as garbage collection and leveling the surface of the soil. If it is necessary to carry out the last of these works, it will be possible to transfer the soil from one place to another.
Blade design features
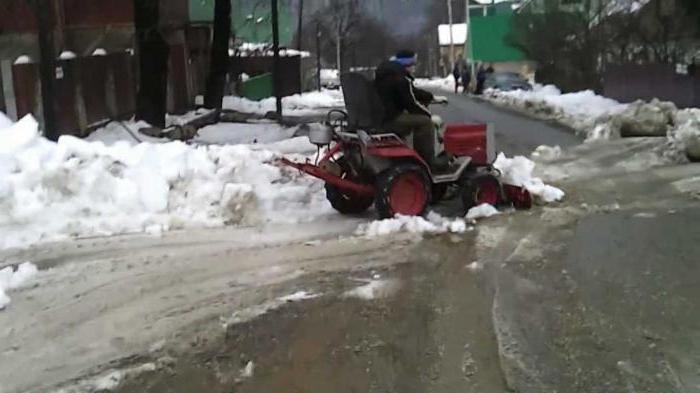
If you decide to make a do-it-yourself dump for your walk-behind tractor, you first need to familiarize yourself with the design features of this attachment. The operation to adjust the position of the element is completed by setting the required angle and fixing the blade in a certain position. In this case, cotter pins are used. It should be noted that the width of the spade of the described equipment, as a rule, is equal to the limit of one meter. This indicator can be considered relevant in the case when the bucket is made of metal with a thickness ranging from 2 to 3 millimeters. You should take advantage of the experience of professional manufacturing companies that use high-quality steel in the manufacturing process of dumps. When a do-it-yourself dump for a motor-block is made, it can be additionally equipped with metal nozzles in the form of knives, which will be most convenient to use for leveling the soil. Among other things, you can equip the equipment with rubber nozzles, which are indispensable for snow removal. Shovels should not be equipped with spring damping mechanisms, this is due to the fact that the speed of movement is quite low, therefore protection from contact with an uneven base of the soil is not required. The motoblock absolutely does not need rotary lifting devices that can reduce the cost of a set designed for snow removal.
Features of the manufacture of the blade
It is not difficult to make a moldboard for the Salute motor-block on your own, and you will have to use a welding machine, a grinder and a drill. Itβs not worth it for a long time to search for a metal of suitable quality, because for this you can prepare an ordinary steel barrel, the volume of which is 200 liters. The capacity must be cut into three equal parts, which will allow you to get three segments, each of which has a curved shape, which is exactly what is required. It is these blanks that will be used to make the shovel. On the contour, two pre-prepared elements must be welded together, which will allow you to get a product whose metal thickness is three millimeters. This indicator will be enough to provide the necessary rigidity of the equipment.
The nuances of the work
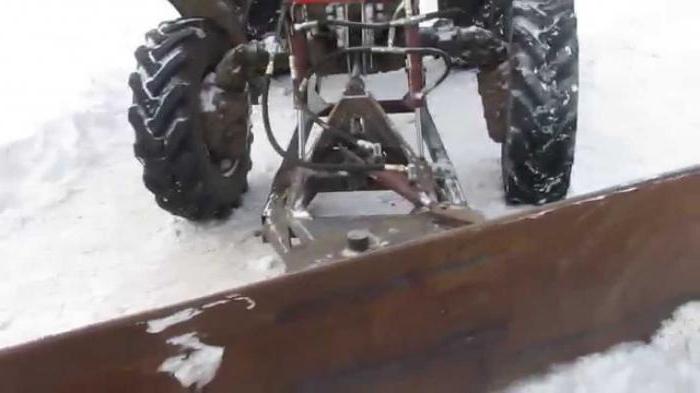
When a blade is made for the Salute motoblock, the lower part of the element can be strengthened with a knife. To do this, the master must prepare a metal strip whose thickness is 5 millimeters. Its length should be equivalent to the capture of the blade. At the next stage, 6 mm holes should be made in the knife, placing them 12 cm apart. These manipulations are necessary to fix the safety strip, which is made of rubber. The Salute motoblock is supplemented with attachments through a technique that involves a fairly simple fastener design. Any master can make such work at home. To the blade, which is made of two elements of the barrel, a pipe of square section with a side of 40 millimeters must be welded to the middle of the height. This will strengthen the device. Motoblock βSaluteβ will have with attachments, which will be quite convenient to use. At the next stage, a semicircle made of thick steel should be welded to the pipe, and more precisely to its central part. Three holes are pre-made in it, which are needed to fix the rotation angles of the manufactured element.
Moldboard specialist tips
When a spade blade for a walk-behind tractor is manufactured, the next step is to mount the holder, which has a L-shaped shape. One end of this element should be inserted into the hole located on the semicircle. The other end is fixed to the walk-behind frame with bolts. Bolts should also be used to adjust the height of the blade. They are screwed into the holes in the segment of the profiled pipe, which is located on the coupling device.
Features of the manufacture of a spade blade
A drawing of a blade for a walk-behind tractor will allow you to figure out what design features the manufactured item will have. Thus, the dimensions of the device are 850x220x450 millimeters. The shovel must be made of steel sheet, the thickness of which is 3 millimeters. Racks, which are located inside, must be made of sheet steel of impressive thickness. These additions act as stiffeners. They need to drill holes to fix the blade to the rods. It is important to ensure the vertical arrangement of equipment in relation to the front of the walk-behind tractor.
The dump on the Neva motor-block can be made by the same technology. To mount the element, use the bracket that is mounted on the legs of the walk-behind tractor. The latter is fixed base hinged front support. In this case, use M10 bolts. Additionally, the equipment should be strengthened to the walk-behind tractor using adjusting rods, the number of which is limited to two. When they are inoperative, they allow to unload the brackets. Blade blade for walk-behind tractor mounted to the bottom with bolts. The knife should have dimensions of 3x100x850 millimeters.
Final work
The bottom should be sheathed with metal in order to exclude the incision of the element into the ground. The depth of the bottom can be what you choose yourself. If the height of the main element is equal to 450 millimeters, and the depth is equivalent to 220 millimeters, then such equipment will more resemble a bucket.
Conclusion
If you decide to make a dump yourself, which will be used in conjunction with a walk-behind tractor, it is recommended to take the above rules as a basis. Each master can independently experiment with the sizes, which will allow equipping motoblocks of different brands with attachments. Among the most famous can be distinguished "Salute" and "Neva". At the same time, snow removal will be not only easy for you, but also quite enjoyable. It is important to ensure that the metal is not affected by corrosive processes. For this, its surface is often treated with special primers that convert rust. After that, the base can be coated with special frost-resistant paint. Such manipulations will extend the life of the elements, eliminating the need for repairs or the purchase of a new snow removal device.