A homemade engine can be made in several ways. We begin the review with a bipolar or step version, which is an electric motor with a double pole without brushes. It has DC power, divides the full revolution into equal shares. For the operation of this device will require a special controller. In addition, the device includes a winding, magnetic elements, transmitters, signaling devices and a control unit with a dashboard. The main purpose of the unit is to equip milling and grinding machines, as well as to ensure the operation of various household, industrial and transport mechanisms.
Types of motors
A homemade engine can have several configurations. Among them:
- Options with permanent magnet.
- Combined synchronous model.
- Variable motor.
The permanent magnet drive is equipped with the main element in the rotor part. The functioning of such devices is based on the principle of attraction or repulsion between the stator and the rotor of the device. Such a stepper motor is equipped with a rotor part of iron. The principle of its operation is on a fundamental basis, according to which, the maximum allowable repulsion is carried out with a minimum gap. This contributes to the attraction of the rotor points to the poles of the stator. Combined devices combine both parameters.
Another option is two-phase stepper motors. The device is a simple design, can have two types of windings, it is easy to install in the right place.
Monopolar modifications
A home-made motor of this type consists of a single winding and a central magnetic crane, which affects all phases. Each winding compartment is activated to provide a specific magnetic field. Since in such a circuit the pole is able to function without additional switching, the switching of the path and direction of the current has an elementary device. For a standard motor with an average power, one transistor is enough, provided for equipping each winding. A typical two-phase motor circuit involves six wires on the output signal and three similar elements in phase.
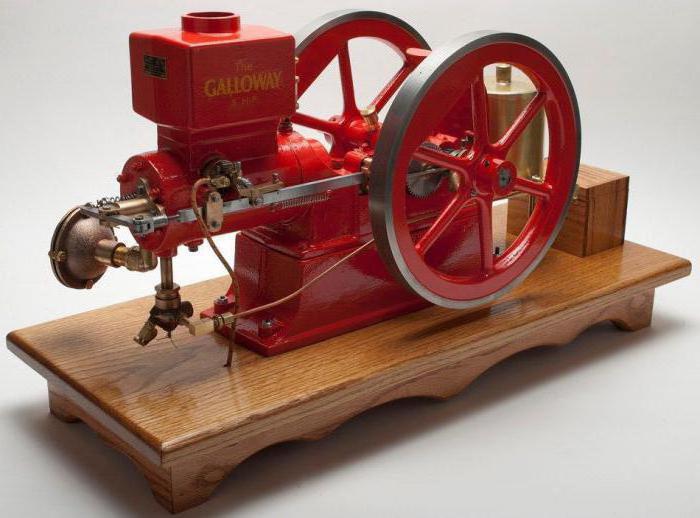
The microcontroller of the unit can be used to activate the transistor in an automatically determined sequence. In this case, the windings are connected by connecting the output wires and a permanent magnet. When the coil terminals interact, the shaft locks to rotate. The resistance between the common wire and the end of the coil is proportional to a similar aspect between the ends of the wiring. In this regard, the length of the common wire is twice as long as the connecting half of the coil.
Bipolar options
A homemade stepper motor of this type is equipped with a single phase winding. The flow of current into it is carried out by a tipping method using a magnetic pole, which causes the complexity of the circuit. It usually aggregates with a connecting bridge. There are a couple of extra wires that are not shared. When mixing the signal of such a motor at higher frequencies, the friction efficiency of the system decreases.
Three-phase analogues having a narrow specialization are also created. They are used in the design of CNC machines, as well as in some automotive on-board computers and printers.
Device and principle of operation
When voltage is transmitted to the terminals, the motor brushes are driven in continuous rotation. The idle setting is unique because it converts incoming pulses to a predetermined position of the existing drive shaft.
Any pulse signal acts on the shaft at a specific angle. Such a gearbox is most effective if a series of magnetic teeth is placed around a central gear iron rod or its analogue. Electric magnets are activated from an external control circuit consisting of a microregulator. To start turning the motor shaft, one active electromagnet attracts the teeth of the wheel to its surface. When they are aligned with the leading element, they move slightly to the next magnetic part.
In a stepper motor, the first magnet should turn on, and the next element should be deactivated. As a result, the gear will begin to rotate, gradually aligning with the previous wheel. The process is repeated alternately as many times as necessary. Such revolutions were called "constant step." The rotation speed of the motor can be determined by counting the number of steps for a complete revolution of the unit.
Connection
Connecting a mini-engine, made by yourself, is carried out according to a certain scheme. The main attention is paid to the number of wires of the drive, as well as the purpose of the device. Stepper motors can be equipped with 4, 5, 6 or 8 wires. The four-wire version can only be operated with a bipolar device. Any phase winding has two wires. To determine the required connection length in step-by-step mode, it is recommended to use a regular meter, which allows you to set the required parameter accurately enough.
A powerful six-wire motor has a pair of wires for each winding and a centering valve that can be connected to a mono or bipolar device. For aggregation with a single device, all six wires are used, and for a paired analogue, one end of the wire and the central crane of each winding will be enough.
How to make an engine do it yourself?
To create an elementary motor, you will need a piece of magnet, a drill, fluoroplastic, copper wire, a microchip, a wire. Instead of a magnet, you can use an unnecessary vibration alert on your cell phone.
A drill is used as a part of rotation, since the tool is optimally suited for technical parameters. If the inner radius of the magnet does not correspond to a similar aspect of the shaft, you can use copper wire by winding it in such a way as to remove the backlash of the shaft. This operation makes it possible to increase the diameter of the shaft at the point of connection with the rotor.
In the further creation of a home-made engine, it will be necessary to make fluoroplastic bushings. To do this, take the prepared sheet and make a hole with a diameter of 3 mm. Then design the sleeve tube. The shaft must be sanded to a diameter that allows free movement. This will avoid excessive friction.
Final stage
Next is the winding of the coils. The frame of the required size is clamped in a yew. To wind 60 turns, you need 0.9 meters of wire. After the procedure, the coil is treated with adhesive. It is best to carry out this delicate procedure with a microscope or a magnifying glass. After each double winding, a drop of glue is introduced between the sleeve and the wire. One edge of each winding is soldered together, which will make it possible to obtain a single unit with a pair of outputs that are soldered to the microchip.
Technical plan options
DIY mini-engine, depending on the design features, can have different characteristics. Below are the parameters of the most popular step modifications:
- ShD-1 - has a step of 15 degrees, has 4 phases and a torque of 40 Nt.
- DSh-0.04 A - the step is 22.5 degrees, the number of phases is 4, the revolutions are 100 Nt.
- DSHI-200 - 1.8 degrees; 4 phases 0.25 Nt of torque.
- DSh-6 - 18/4/2300 (values ββare indicated by analogy with the previous parameters).
Knowing how to make the engine at home, it is necessary to remember that the speed of the twisting parameter of the stepper motor will be transformed in direct proportion to the similar current parameter. Lowering the linear moment at high speeds depends on the drive circuit and the inductance of the windings. Motors with degree of protection IP 65 are designed for harsh operating conditions. Compared to servers, step models work much longer and more productively, do not require frequent repairs. However, servomotors have a slightly different focus, so comparing these types does not make much sense.
Making a homemade engine
A do-it-yourself motor can also be made with liquid fuel. At the same time, sophisticated equipment and professional tools are not required. A plunger pair is needed , which can be taken from a tractor or automobile fuel pump. The cylinder of the plunger sleeve is created by trimming the thickened element of the loop. Then you should make holes for the exhaust and bypass windows, solder a couple of nuts in the upper part, designed for spark plugs. Type of elements - M-6. The piston is cut out from the plunger.
Homemade diesel engine will require the installation of a crankcase. It is made of tin with soldered bearings. Additional strength will allow you to create a fabric coated with epoxy resin, which covers the element.
The crankshaft is assembled from a thickened washer with a pair of holes. It is necessary to press the shaft into one of them, and the second extreme socket serves for mounting the stud with the connecting rod. The operation is also performed by pressing.
Finishing work on the assembly of a homemade diesel engine
The following is the assembly order of the ignition coil:
- Used part from a car or motorcycle.
- A suitable candle is installed.
- Mounted insulators, fixed with the help of "epoxy".
An alternative to a motor with an internal combustion engine system can be a closed-type non-contact motor, the device and principle of operation of which are a system for the reverse exchange of gases. It is made up of a two-section chamber, a piston, a crankshaft, a transmission box, an ignition system. Knowing how to make an engine with your own hands, you can significantly save and get the necessary and useful thing in the household.