If you are the owner of a livestock farm, you know very well how useful the grain crusher is. Using this equipment, you can quickly replenish food supplies for poultry and rabbits, and prepare a combined composition designed for livestock. Finding an inexpensive grain crusher in the market for related products is difficult. For this reason, do-it-yourself grits can be made.
Making a grain crusher from an old vacuum cleaner
Do-it-yourself kruporushka can be made from an old vacuum cleaner, so do not get rid of old household appliances. You can borrow a motor from him. Among other things, it will be necessary to use a plywood sheet whose thickness is 10 millimeters. You will need a metal plate that will perform the task of the knife. The working chamber will be made of steel strip. It will be necessary to stock up with wooden pins, as well as nuts and washers. You will need a sleeve, as well as a hopper and a damper, which are necessary for feeding grain.
Features of the work
Do-it-yourself kruporushka should be made using technology that involves preparing the base. For this purpose, a plywood sheet should be used, from which it is cut out, and after a square is cut, the side of which should be equal to 300 millimeters. On top of it should be fixed working electric motor, borrowed from a vacuum cleaner. In this case, it is necessary to arrange its lower part so that it protrudes by 40 millimeters.
Making a knife for equipment
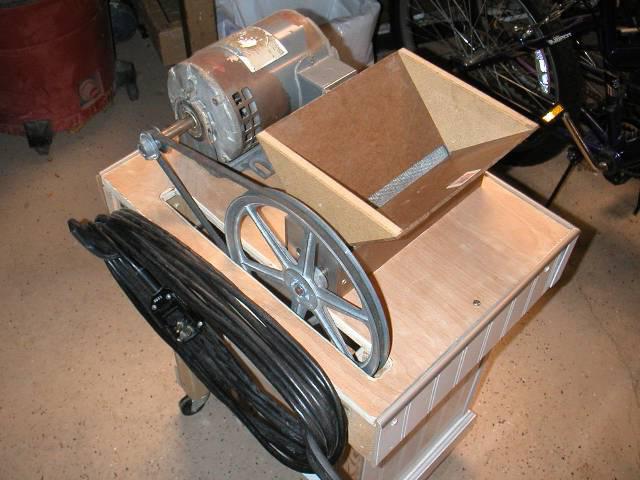
Do-it-yourself grinder should be made using a knife, which will have to rotate at high speed, due to which the grain will grind, this element must be performed separately. To do this, you will need to use a steel plate, which should have dimensions of 15x200 millimeters, while the thickness should be equal to 1.5 m. It is preferable to choose the strongest materials. In addition, you can use car holders or other parts that can be borrowed from household appliances. The knife should be sharpened in the form of a blade; for this, both edges should be machined towards the axis of rotation. When a home grinder is made with your own hands, you can experiment with the shape, giving the blade the appearance of a propeller or mowing corners. Using emery, it will be possible to adjust the plate horizontally and vertically. After that, in the central part of the working surface of the knife, it is necessary to make holes in diameter, suitable for the shaft of the vacuum cleaner motor. The knife must be fastened to the threaded tail using a bushing, two washers and a nut.
Production of the working chamber and the hopper
When making a grinder for the house with your own hands, you will need to make a camera, for which it is necessary to use a steel strip, its length should be 700 mm, while about 10 mm will be needed for fastening, while the width should be more than 60 mm. The steel billet must be rolled up into a ring, and the rib bent outward around the perimeter of the chamber. The resulting flanges in width should be no more than 10 millimeters, which will be needed for fixing with the base and for mounting the sieve.
When a do-it-yourself grinder is carried out, the drawings of which can be prepared independently, the crusher needs to be firmly fixed; for this, it will be necessary to install fonts on the bottom of the camera that will be needed in the amount of three pieces. You need to remove them from each other at an equal distance.
Sieve making
Before you make a grinder with your own hands, you need to think about what the sieve will be. It can have any diameter of the holes. The parameters of this element will depend only on what result you want to get. So, for the manufacture of flour, you need a fine mesh, to get coarse grinding the cells must be larger. The grain will enter the working chamber from the hopper, which is fixed on the base. It must be equipped with a minor hole, as well as a shutter made in the form of a plate. Using the latter, it will be possible to adjust the flow of raw materials. Do-it-yourself corn grinder should be equipped with a container that should be installed under a sieve. It will be intended to collect finished products, you can use a bucket or pan for this.
Production of crushers by type of mill
Kruporushka (with his own hands), a photo of which is presented in the article, may look like a mill. To do this, it will be necessary to prepare the stator, as well as the rotor, which will work on the basis of millstones. As a stand for such equipment will be a box on which to mount an electric motor of low power. Be sure to use a single-phase unit, you can use the one that is redone from a three-phase.
Features of making a homemade mill
The equipment case is a box made of metal, the thickness of the latter should be equal to 5 millimeters. From the material it will be necessary to form a body in the form of a cylinder, the diameter of which is 300 millimeters. The lower part will need to be equipped with a stator, while the cover should be located on top of the equipment. Inside the housing, a motor and a mill should be located, which is fixed so that the bearing slides on the device shaft, in turn, the rotor is mounted on it. Rotating, it will begin to reach speeds of up to 3000 rpm in one minute. The bunker will need to be strengthened over the housing, using screws for this, and through it grain will be supplied.
In order to make it more convenient to use the equipment, you need to install a damper that will regulate the flow of raw materials. You will need a sleeve, which will serve as anther, it must be made of canvas material. Products will come out through this element. Do not forget that holes must be made for the supply and subsequent extraction of the finished grain.
Stator manufacturing features
The stator needs to be made using a sheet of metal whose thickness is 2 millimeters, while the width is equivalent to 50 millimeters. The metal strip must be bent around the circumference and placed in the mold for pouring, closing from one end with aluminum to make a bowl. Its thickness should be equal to 4 millimeters. In the next step, the part is ribbed. To do this, cut several corners, and then weld from the inner side of the stator.