Finishing the facade, the basement of the house and the interior walls with stone becomes a more popular solution. This fact cannot be called surprising, because such a design allows you to protect the surface from damage and pollution, and also becomes a decorative decoration. However, natural stone has not only an impressive weight, but also creates additional loads. It is very difficult to work with it, and the price of such decoration often becomes the reason that consumers refuse such decisions.
There is a way out, and it is quite simple. It is expressed in the use of artificial stone. It has a small mass, is easy to process, it is very simple to work with it. The material attaches well to the surface. Artificial stone can replace natural, and it can be used not only for wall decoration, but also for facing fountains, flower beds, as well as laying garden paths.
A particularly important factor in favor of this finishing material is its affordable cost. In order to achieve more significant savings, you can resort to the independent manufacture of this material at home. For this, it will only be necessary to prepare a solution, create or acquire forms with the desired relief, and also be savvy with relevant knowledge.
What is an artificial stone?
If you set out to make an artificial stone with your own hands, you should ask what it is. You can execute it from different raw materials, which is selected depending on the type of walls, as well as the goals pursued. For example, gypsum-based stone is most often used for interior decoration, while cement mortar is excellent for exterior cladding, and different substances are added to its ingredients. Among these components, it is worth highlighting those that give the stone a unique relief pattern.
Use in the process of creating the solution can sand and fine gravel. To give the stone the desired shades, coloring dry components are added. If there are several pigments, then they are selected so as to ensure a harmonious combination. Finishing stone should turn out to be of high quality, for this you should prepare a good shape for it. You should not buy cheap plastic products, as they often break after the manufacture of the first batch of stone. Silicone matrices that are ready to last a long time will be the best option. Using them you can make as much stone as you need.
Mold making
You can make a mold for making artificial stone with your own hands. This method should be resorted to if you want to finish this or that surface using a certain design, and a stone suitable for this is too expensive, or you have not been able to choose an option that matches the shade. In this case, you can purchase several tiles, on the basis of which forms will be made.
As a basis, you can take a real stone, which will have a favorite textured pattern. The source can be wood with an expressive textured pattern. It is pre-deepened. If you decide to make a mold for artificial stone with your own hands, then you can make it in the form of complex or single products. The latter are carried out according to a simpler technology, because there will be no need for dimensional formwork. The amount of silicone is also reduced.
To make an artificial stone in the next step using such forms will be much easier and faster. The output will be able to get several ready-made solutions at once. For formwork you need to find a box of plywood. A cardboard box will do. The dimensions of this element should be 15 mm wider. As for the height, it should be 30 mm larger in relation to the original sample. If the stone should have a small size, then for the formwork you can use the usual box of juice. When preparing it, you will need to cut the cardboard from one of the wide sides. Such a product has sufficient rigidity to withstand silicone pouring.
Before you start making artificial stone with your own hands, you will need to prepare a mold. It can be performed by connecting several boxes together. In this case, a distance of 12 mm is maintained between the elements. This lumen should be hermetically sealed, as it acts as a wall between future forms. You can proceed to the preparation of the initial sample in the next step. As it can be used silicone sealant, compound or polyurethane.
Silicone molds
Silicone sealant can be purchased in buckets or tubes. You should buy the amount of material that will be needed to make the mold. As soon as the formwork can be prepared, grease should be applied to its inner walls, sometimes even solidol acts. At the bottom is the original element, it can be made of natural stone, a finished version of artificial stone or tile with smooth surfaces. You can use as a template any item for which you plan to make a mold.
The item laid in the formwork should be greased with a greasy substance. This is to ensure that silicone can be easily detached after solidification. If the finished artificial stone made of gypsum acts as the initial sample, then it must first be covered with two layers of drying oil or varnish. Each layer dries well.
At the next stage, you can begin to prepare a soap solution. It will be necessary to wet the spatula and brush. These tools are used for laying out and distributing silicone inside the formwork. If you purchased silicone in a tube, then it should be placed in the formwork completely, and then dip the brush in the solution and distribute it inside the box.
It is extremely important that the silicone fits snugly against the sample. In this case, no sinuses should be formed. As soon as the formwork is filled to the desired level, the silicone surface is leveled with a spatula. Its working surface should first be moistened in a soap solution. As soon as the work is completed, the formwork is left until the moment of polymerization.
There is no need to rush to remove the form. It should stand intact for as long as possible. The quality of the resulting matrix will depend on this. Polymerization will occur, starting from the outer surfaces, gradually deepening. About 2 mm of thickness will dry in a day. The process of solidification may take several days or weeks. Everything will depend on the depth and thickness of the layer. If you decide to do the manufacturing of stone at a certain time, then you should take care in advance to prepare the matrix. After the end of the estimated period, the formwork is removed, the resulting form is removed and washed from grease. Only then can it be considered that it is ready for use.
Making gypsum stone
If you wondered how to make an artificial stone with your own hands, then you can take gypsum as a basis. It is most often used for interior decoration. However, if proper processing is ensured, the products can be used for facade surfaces. Plaster is more common among artificial stones compared to cement. After solidification, products have better adhesion than those made of concrete.
For the work should be prepared:
- form;
- capacity;
- electric drill;
- brushes;
- pallet;
- white gypsum;
- spatulas;
- citric acid;
- washed river sand;
- water
- dry coloring pigment;
- composition of wax and turpentine.
Before you make an artificial stone with your own hands at home, you must take care of the presence of the form. It will act as a matrix and should be made of elastic material. To mix the ingredients, you should prepare a container, a plastic bucket can act as it. To dry the tiles you will need a pallet.
Additives and Tips for Making
In addition to citric acid, PVA glue should be prepared. The water used in the work must have room temperature. When making artificial stone with your own hands at home, you should take care of the working area. It should be equipped with a workbench. Its surface is well aligned horizontally. Use for this necessary level. Otherwise, the tile will receive a different thickness.
If the amount of finishing material should be large, then you should take care of the availability of shelving for drying products. The material will remain on them for several days. To mix the solution, you also need free space.
Mixing solution
When an artificial gypsum stone is made with your own hands, the raw materials must be added to the water. Otherwise, the mass will turn out to be heterogeneous, it will have inclusions and lumps. It must be remembered that gypsum sets quickly. The polymerization process occurs within 7 minutes. If there is a need to increase this period, then citric acid should be added to the ingredients. For 1 kg of raw materials should be about 0.8 g of crystalline mixture. The liquid state of the solution under such conditions is extended to 1.5 hours.
Acid is diluted in warm water, and then added to the solution. If the mass will be poured into a single form, then it is necessary to prepare it in a small amount. For the strength of the finished product, sand can be added to the solution. The size of the fraction can vary from 0.01 to 1 mm. The final value will affect what kind of stone will take.
Proportions and Consistency
When making artificial stone with your own hands, you must remember that the mixture is mixed to the consistency of thick sour cream. The composition can be shut in different proportions, but experts recommend adding 100 g of sand per 1 kg of gypsum. Plasticizer can be PVA glue. He is able to slightly extend the setting time of the mixture. Plaster and water are added in proportions of 1.5 to 1.
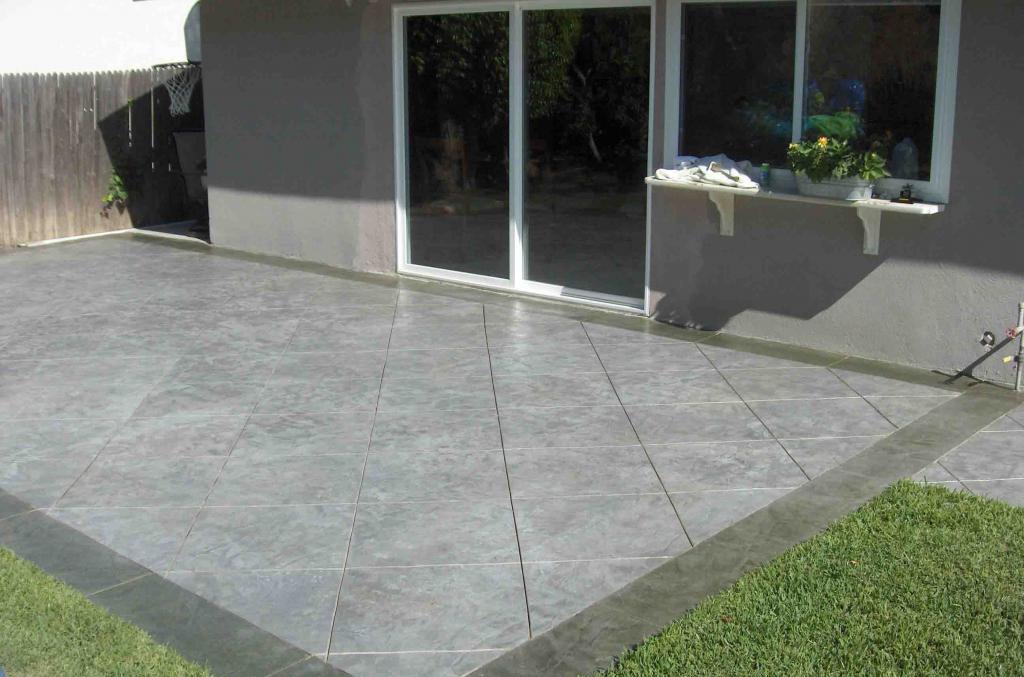
The right amount of water should be poured into a clean bucket. If there is a dry coloring pigment in the solution, then it is added next and mixed well. At the next stage, gypsum is poured, after which the mixture is well mixed with a mixer. Following is sand, the composition after that mixes well. Once the mixing of the solution has been completed, the matrix should be prepared. If it is made of plastic or silicone, then it is smeared with a composition that consists of turpentine and wax. You can apply the release agent in the finished form. If the form is made of polyurethane, then it does not require special preparation, although lubrication will not become superfluous.
Countertop Making
Quite often, recently made tabletops made of artificial stone with their own hands. The basis can lie:
- concrete;
- finished artificial stone;
- ceramic tile.
In the first case, we are talking about a solution that is also used in capital construction. The design will turn out massive and durable, and you can take care of beauty by adding special fillers to the mixture. The tabletop made of artificial stone with your own hands can also be made of acrylic, which is sold in the form of sheets. Their thickness can vary from 3 to 12 mm. The filling is granite or marble chips.
Features of the work
The base is formed from plywood, to which a sheet of artificial stone is fixed on top.
The simplest and most affordable method of manufacturing countertops is ceramic tile. Quite often, home craftsmen use concrete. For its mixing cement of grade M-400 or higher, coarse filler, fine filler and plasticizer for thinning are used. If you want to make a countertop made of artificial stone with your own hands, it is better to use a granite sink or river sand. Marble or granite chips can become a large filler.
Additionally, colors and dyes can be used. They are added at the time of pouring concrete into the mold and distributed occasionally. This allows you to get a design with a kind of ornament. If you use imagination, you can get incredible drawings and patterns. In the manufacture of countertops made of artificial stone with your own hands, you can make the design as smooth as possible. The glossy surface is formed using plywood or laminated particleboard. Their surface must be moisture resistant.
Mounting Features
Artificial stone in the end can have a wide variety of shapes, textures and colors. Such products are even painted after the solution dries. To achieve the desired shade, paints and varnishes are applied in several layers.
When installing artificial stone with your own hands on a wooden surface, the base is carefully prepared. It is waterproofed and covered with a crate. But in the case of concrete or a brick base, additional preparation work is not required. Surfaces are just aligned. Do-it-yourself fixing of artificial stone is carried out on cement mortar or adhesive compositions. You can resort to stitching. Sometimes this step is neglected.