Modern heating and water supply systems for apartments have long moved away from the use of cast-iron pipes. They were replaced by lightweight, easy-to-use and corrosion-free plastic. It was widely used due to the long life and ease of installation. In the presence of a special apparatus and compliance with the technology of work, the welding of polypropylene pipes with your own hands for beginners is considered not so difficult. Pipes of various categories are produced from pure polypropylene or with a reinforced inner layer of metal foil, which increases the strength of this material.
Polypropylene pipe categories
Marking is applied to the outer surface of the product, according to which it is easy to determine under what pressure this material can be operated.
The following types of polypropylene pipes exist:
- PN10 are pipes designed for cold water supply systems, as well as underfloor heating devices. These thin-walled products can operate at a pressure of 1 MPa.
- PN16 - withstand pressure of 1.6 MPa and a temperature of up to 64 โ. These products are used as pipelines of a heating system with reduced pressure, as well as distributing cold liquid.
- PN20 - are considered universal pipes, which are widely used in both cold and hot water supply. Working pressure - 2 MPa.
- PN25 - pipes reinforced with aluminum foil, which can be used in any system at a pressure of 2.5 MPa.
Material Features
Reinforced polypropylene is made by special technology, which allows layers of material to be bonded to each other not by glue, but by the use of perforation. Each manufacturer applies the holes differently, which distinguishes the pipes in quality. Due to this type of connection, the layers of the product are thin-walled, which significantly increases the flow rate of the liquid.
Ecological purity of the material allows its use in the drinking system, without consequences for human health.
Methods for joining polypropylene pipes
Depending on the equipment and materials used, welding of polypropylene pipes with your own hands can be carried out in the following ways:
- The diffuse joint method allows you to get the most reliable and durable welding seam. This method is based on the principle of diffusion of the material, which occurs due to heating of the edges of the workpieces to the melting temperature. In this case, the polypropylene of both parts of the product is mixed together and after cooling forms a high-quality compound. A feature of the diffuse method is the ability to work only with homogeneous materials.
- The polyfuse joint is similar to diffuse welding. Only in this case, one of the two billets is heated by the contact of the welding machine.
- The bell-shaped method is used for joining pipes of small diameter. The diameter of the pipe to be connected is slightly larger than the internal section of the coupling, after melting and a little physical effort, the workpiece enters the coupling to the depth of heating.
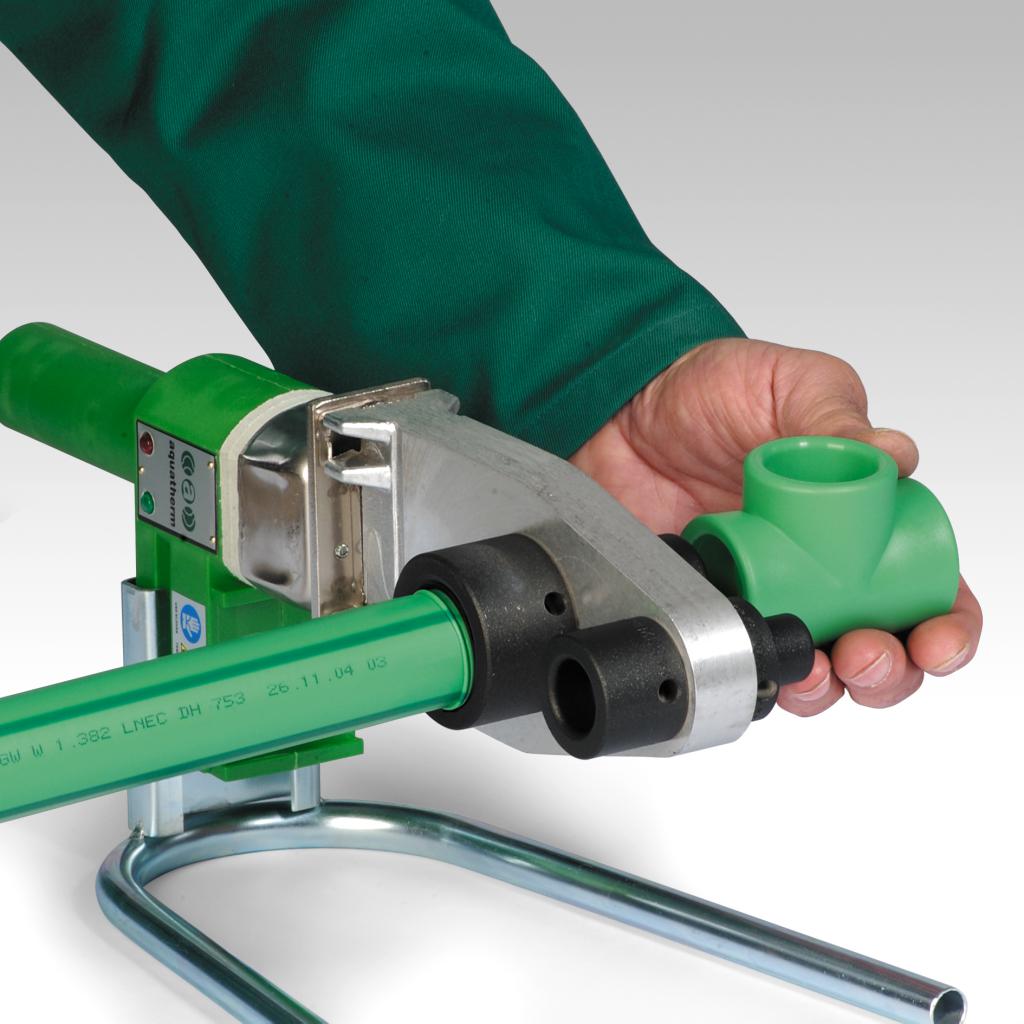
- The joint method of the surfaces to be welded is used when welding polypropylene pipes of the same diameter and type. The ends of the workpieces must be strictly aligned. As a result of simultaneous heating and mechanical pressing on the workpiece, the polypropylene merges two pipes. Due to the need for a high-precision welding machine for welding polypropylene pipes at home, this method is almost never used.
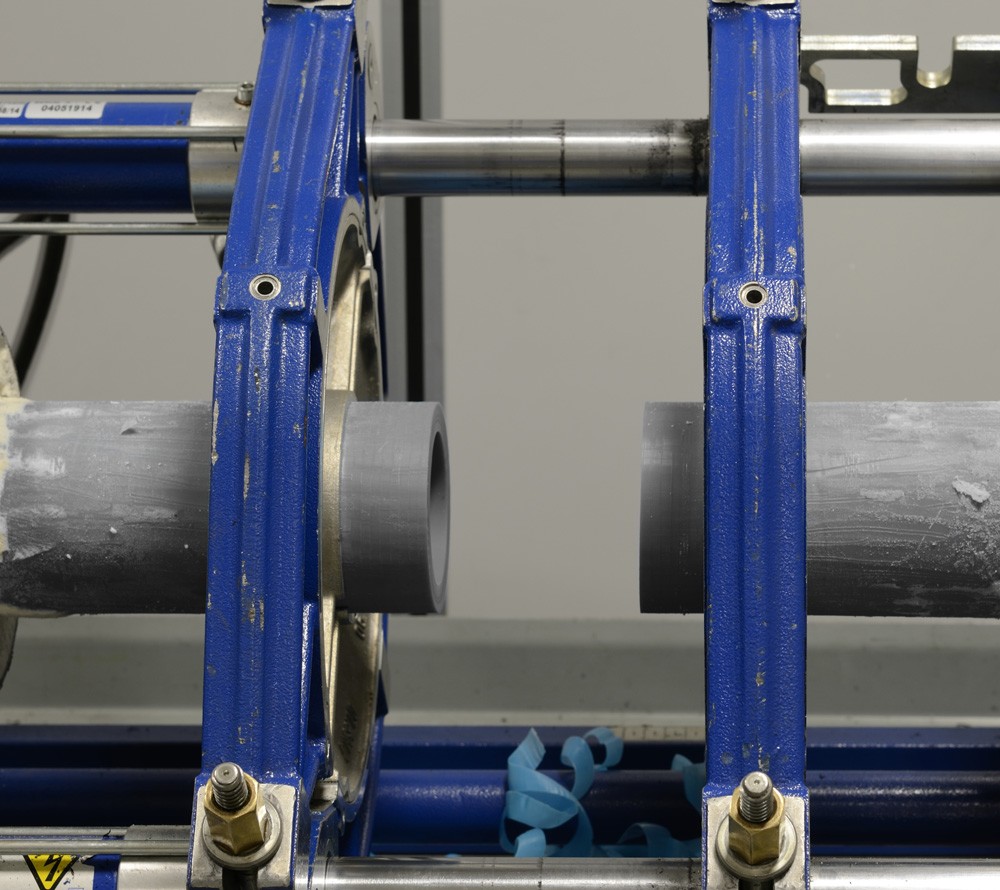
- In the coupling method, special-purpose equipment is used for connection - electrical fitting. The two ends of the pipe, cut strictly at right angles, are inserted into the coupling. After applying voltage to the fixture, the parts are heated to the optimum value and the workpieces are welded together.
- The cold method is used when installing a domestic water supply system with a low working pressure. This view more closely resembles the technology of gluing two surfaces. The inner edge of the fitting and the edge of the pipe are lubricated with glue solution, after which the workpieces are joined and held until the glue hardens.
When welding polypropylene pipes with a diameter of 4 cm or more, it is very difficult to center and connect them, therefore special units are used, which are related to expensive and high-tech equipment operating in automatic mode.
Welding operations
The most common is welding with fittings, in which the workpiece is inserted into a special fixture, which ensures tight joining of the products. The main stages of the welding joint:
- cutting blanks;
- preparation of surfaces for welding;
- setting up the apparatus for welding polypropylene pipes;
- direct welding process;
- cooling parts after connection.
Pipe cutting
The process of cutting blanks is carried out with a special tool. Although at home, often the cutting stage is carried out with a hacksaw, a grinder or an electric jigsaw. With this method of cutting, the surface is obtained with large burrs, therefore, before welding the polypropylene pipes, the edges must be carefully cleaned.
It is better for novice installers to cut pipes with special scissors:
- The model of precision type is very convenient to use. It has a serrated blade and a special ratchet. Scissors allow you to get a high-quality and even cut. But if necessary, working with a large number of workpieces can quickly tire your hand.
- Even better cut quality can be achieved using the roller model. The cutting technology is carried out by a guide roller that rotates around the pipe. A negative property is the low cutting speed.
- Models of the battery type combine all the advantages - quality and cutting speed. They are equipped with a small electric motor and can be used to perform a large amount of work.
Billets of large diameter are cut with special pipe cutters, allowing to obtain a high-quality and clean cut.
Preparation of the workpiece for welding
Exact adherence to the process when welding do-it-yourself polypropylene pipes for beginners is considered half the success of this work. Therefore, an important step is the preparation of the surface of the parts to be joined.
Implementation of several recommendations will allow you to get a positive result:
- Welding of polypropylene pipes begins with marking and cutting in the right place, of good quality.
- On the reinforced blanks, the metal top layer of the material is removed, otherwise the presence of foil will not make it possible to obtain a reliable, long-term connection. The protection layer is cleaned with a special tool. If the reinforcement is carried out with a layer of fiberglass, then stripping it is not required.
- The inside of the fitting and the edges of the pipe are degreased with a solution of alcohol, and also checked for contamination or surface defects. Then the welding process itself is performed.
Apparatus for joining pipes by welding
Any apparatus for welding polypropylene pipes has a working surface, which is heated by the action of electric current. The device may be equipped with one or more heating elements that heat various nozzles. It is these devices of different diameters that allow you to work with different pipes in one device. At home, this equipment is called an iron for welding polypropylene pipes.
As a rule, devices have four sets of welding nozzles in a set, which allow you to connect almost any pipe used in household systems. Nozzles for welding polypropylene pipes are coated with Teflon spraying, which eliminates the possibility of plastic sticking to them during heating. Independent manufacture of these devices is impossible due to the complexity of the technological process of spraying.
Xiphoid devices
Such inexpensive devices are designed to work in a domestic environment. They weld polypropylene pipes with a diameter of up to 40 mm. The appearance of the heating plates in many models is very similar to a household iron. The plates of the heating element have holes in which interchangeable nozzles are installed.
When welding for polypropylene pipes, positive reviews relate to the PRORAB 6405-K model. It is distinguished by sufficient reliability and relatively low cost. Perfect for home work. This apparatus consists of a heating plate, a temperature regulator and a handle. The soldering iron kit for welding polypropylene pipes can also include additional equipment: a torch, a device for chamfering, a device for removing reinforcement.
Cylindrical units
Models of this series belong to professional welding machines. Nozzles in such devices are mounted on an elongated side or straight cylinder.
Devices having a L-shaped heater are used for welding in inaccessible places.
Of course, the high cost of such devices makes it difficult to use them at home, but many craftsmen still prefer to weld pipes with these devices. They provide high quality work with large diameter pipes.
Criteria for choosing devices
First of all, when choosing a fixture, it is necessary to correctly establish the range of tasks that need to be solved during operation. With a one-time use of the welding process in domestic conditions, the acquisition of an expensive professional apparatus is considered unprofitable. It is enough to have an inexpensive high-quality device of medium power.
Power of devices for welding
The speed of the work completely depends on the rated power of the welding machine. Any device heats up to a predetermined temperature, so the power indicator of the device does not affect the quality of the connection. For home use, a device with a power of up to 1 kW is enough.
A more powerful device is much faster put into a ready state after switching on, since any device needs time to compensate for the heat loss during the operation.
Also, high power indices are required when welding large diameter workpieces.
Temperature and heating time
Obtaining a high-quality and durable connection of polypropylene pipes completely depends on the correct choice of the heating temperature of the welded surfaces. The optimal indicator is 260 โ. If its parameters are deviated, surface damage during operation and, as a result, leaks in the system can occur.
At a low heating temperature, the fastening of parts is fragile due to poor melting of the material. Excessively high temperature leads to deformation of the plastic and the formation of sagging, as a result of which the pipe diameter decreases.
The temperature level is set by electronic or bimetallic thermostat.
From the diameter of the pipes to be welded, the time of temperature exposure depends. It should be within:
- a workpiece with a diameter of up to 20 mm is heated for no more than 6 seconds;
- 7 seconds are enough for soldering a 25 mm pipe;
- parts up to 32 mm are processed for 8 seconds;
- products with a diameter of 40 mm heat up 12 seconds.
Despite the seemingly simple technology of the work, you must always listen to the advice of experienced operators. Before welding polypropylene pipes for beginners, it is better to practice on unnecessary pieces of workpieces, since the connection is inseparable, and with poor quality work, you can spoil the basic materials.