Plasma cutting is very widely used in various sectors of construction and production. Convenience of work and the quality of the final result of such a processing method have gained immense popularity among specialists. That is why many novice craftsmen and even individual teams often ask how to make a plasma cutter from an inverter with your own hands, since the original device is quite expensive and everyone wants to save money using the available equipment.
Appointment
First of all, this device allows you to quickly cut various metals. This is very convenient when creating all kinds of designs without using another tool. Also, a manual plasma cutter can use different electrodes with which welding is performed.
The process of joining metals using an aggregate involves the use of a soldering method. Therefore, the main advantage of this equipment is that thanks to it it is possible to connect completely different metals using high-temperature solder.
Special attention deserves the use of such a tool in blacksmithing. The fact is that with its help it is possible to produce hardening, annealing, thermal stripping and welding of ferrous and non-ferrous metals together. Therefore, its presence in such a production is a necessity, which allows to save a lot of time.
Design Features
Assembling a plasma cutter from the inverter with your own hands, you need to know its device and configuration. However, it is immediately worth noting the fact that some parts are much easier to purchase in finished form than to create yourself.
A typical apparatus consists of a power source, a plasma torch, which is also very often called a βcutterβ, an air compressor, and a hose-cable package.
- A power source is necessary in order to supply a current of a certain strength to the device. In fact, it is the heart of the device, and its technical characteristics depend on it.
- No less important is the torch itself or the plasma torch. It has a certain design, which differs significantly from similar products on welding units. It should be noted right away that when creating a plasma cutter from an inverter with your own hands, it is better to purchase this part in a store. This will greatly facilitate the operation and solve a lot of problems with the replacement of some elements.
- A compressor in an apparatus operating using a current of no more than 200 A is required to supply air, which performs the functions of cooling and allows you to create a dense plasma beam. For more powerful plants, argon, helium, hydrogen, nitrogen, oxygen and mixtures thereof are used.
- The cable β hose package serves as a connecting element through which electric current from the power source and air from the compressor to the plasma torch are supplied.
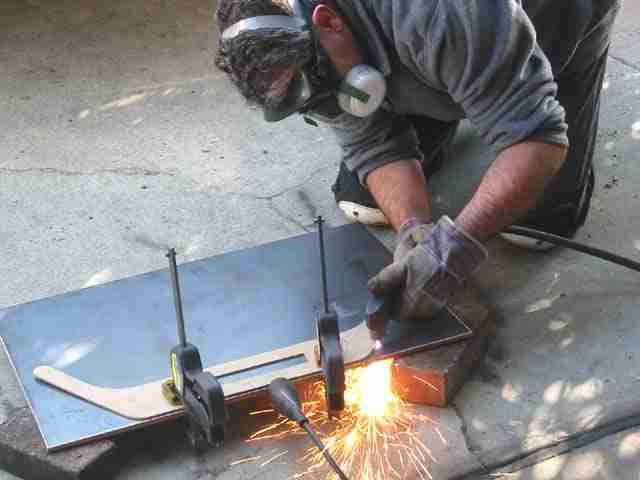
Transformer or inverter
Typically, a plasma metal cutting machine uses an inverter or a special transformer as a power source . Both of these options are great for self-manufacturing, but before deciding on a choice, you need to know what are the differences between them and how this affects the technical characteristics of the final product.
- A typical plasma cutter from a welding inverter is the most efficient and economical. Its efficiency is 30% higher than that of units using a transformer, and it produces a stable arc. However, such a device can only perform strictly defined tasks, working with materials of a certain thickness.
- When using a transformer, you need to remember that this product is rather bulky and requires space for placement. At the same time, its power makes it possible to work with large parts of a rather large thickness. That is why it is installed in stationary rooms or on special mobile platforms.
Given these features of both units, it is best to create a plasma cutter from the inverter, with your own hands connecting the finished power source and other parts in a certain sequence.
Necessary equipment
First of all, you need to purchase all the necessary elements. However, it is immediately worth noting the fact that in order for the installation of plasma cutting of metal to turn out to be high-quality and practical, many of them will have to be purchased ready-made.
Inverter
This unit can be taken from the finished welding machine. Its cost is relatively low, although this can be considered the most expensive investment in this project. Usually, specialists when choosing this device focus on a certain power. It is determined by focusing on the amount of work and its specificity.
Some experts prefer to create an inverter on their own, choosing parts for specific needs or using existing materials. However, as practice shows, it is much easier to use a ready-made unit, since it is more reliable, and certain standards were used in its manufacture.
Cutter
Creating a homemade plasma cutter, masters often make a mistake when trying to completely create the cutter itself, to which current and air will be supplied. The fact is that this product consists of a handle, supply elements and nozzles. Moreover, the latter, with intensive use, wears out very quickly and needs to be replaced periodically. That is why it is recommended to buy a nozzle factory, and the remaining elements can be made independently. However, professionals believe that it is not worth spending a lot of effort and money on the independent creation of this element, since it is much easier to purchase it in a finished form.
Compressor
Typically, a plasma cutter, the instruction for which involves the use of an inert gas or oxygen, is preferred to be connected to cylinders with special mixtures. The fact is that it is they that make it possible to obtain the most dense plasma beam and creates the best cooling. However, for domestic use, it is easier and more economical to use a conventional compressor.
Immediately it is worth noting the fact that this unit can be created independently, using an ordinary cylinder as a receiver. The compressor itself can be taken from a ZIL car or from a refrigerator. However, it is very important to correctly adjust the pressure. Usually, experts do this empirically directly at work.
Cable-hose package
This equipment can be purchased as a set for a specific unit, or separately from each other. The fact is that it consists of hoses that are designed for the pressure necessary for work, and a cable of a certain section. It is worth remembering that the conductor is selected for the power of the inverter itself, because otherwise it will overheat and there may be a possibility of fire and even electric shock.
Assembly
The whole manufacturing process is that you need to connect the plasma cutting nozzle to the compressor and inverter. For this, a cable β hose package is used. It is best to use special clamps and clamps, which allow both assembly and disassembly to be carried out very quickly. Such an approach makes it possible to obtain a compact device that can be conveniently transported to the place of work, which is very much appreciated by specialists.
Recommendations of specialists
- Given that the principle of operation of the plasma cutter is based on the use of gas, it is worth taking care in advance of the availability of spare gaskets that are used when connecting hoses. This is especially important if the unit is constantly disassembled and transported. An elementary lack of this element can stop all work.
- It is also very important to have a spare nozzle for the torch. This part, during prolonged use, fails most often, since it is affected by high temperatures and rapid cooling.
- It is important to remember that inverters from welding machines can be quite expensive, and the price of the issue depends on its power. Therefore, before you purchase it, it is worth deciding on the output characteristics and needs, for which the device is created. This will help to significantly save and get an aggregate that is ideal for specific jobs.
- To work with such a tool, you will need to purchase special electrodes of refractory metals. Materials from thorium, hafnium, zirconium or beryllium are best suited for these purposes. However, it should be remembered that some metals emit harmful substances during heating and can cause harm to the welder. For example, thorium is very toxic, and beryllium forms radioactive oxides. That is why it is easier and safer to use hafnium.
- It is important to remember that the working plasma temperature in such units reaches 30,000 degrees. Therefore, when working, it is necessary to strictly observe safety rules so as not to harm yourself or others or cause a fire. That is why only qualified specialists are allowed to work with such a tool.
- During operation, do not disturb the vortex air flow. Otherwise, two arcs may form, which will completely disable the device. Given this, specialists prefer to use factory cutters, believing that it is better to spend money once than to constantly repair the inverter itself.
- When performing the same type of work, you can make certain modifications to the device. For example, some craftsmen make a special protective cover for the hand or modify the nozzle. However, it is worth remembering that all these additions should not affect the process of equipment operation and should not violate safety rules.
Conclusion
Having considered the question of how to make a plasma cutter using an inverter, you can understand that almost all the necessary equipment will have to be purchased from various manufacturers. In fact, the manufacture itself is an elementary assembly. However, even with this approach, you can save significantly, since a full-fledged set of a new unit will cost several times more.