Throughout the entire history of the existence of human civilization, people have had to solve an engineering problem that constantly arises and becomes more complicated over time - how to move cargo from point βAβ to point βBβ in the least lengthy time, with the least labor costs, minimal losses and damage to the transported cargo, ensuring the health of those who organize the process and take part in it.
Recently, the system of safety requirements during loading and unloading operations has received a solid base on specialized operations technology, information support, technical means to ensure the implementation of these technologies and labor protection procedures.
General questions of the organization of cargo operations
The industrialization processes that have taken place in most countries of the world over the past several decades have led to the creation of a large number of different vehicles, with different characteristics of bodies for placement and storage during transportation of goods. Each type of transport is significantly different from the other. Different types of transport have specific means designs for ensuring the transportation process. The design of a car, wagon or sea ship must comply with the type of cargo transported and its characteristic features.
Fulfillment of safety requirements during loading and unloading operations leads to the development of a large number of various transport designs - gondola cars for transporting sand, refrigerated food machines, sea container ships, air tankers.
Moving cargo consists of three main stages - loading the required material assets into transport, moving to the required point in space with preserving all the properties of the transported product (material, substance) and unloading upon arrival. As you can see, from the point of view of safety measures during loading and unloading operations and the technology of the preparatory and final stages of transportation, cargo operations are extremely relevant.
Analysis of adverse production factors
At the stages of the operations under consideration, maintenance personnel perform their functions with a risk due to the concentration of various adverse factors in the work area.
These include:
- various moving machines, mechanisms and their individual parts (autocars, electric cars, conveyors, buckets, industrial magnets, etc.);
- features of dangerous goods in terms of their composition and properties (acids and alkalis, oil products, electrolyte, large mass products, etc.);
- harmful compounds in the air of the working area;
- dangerous from the point of view of injuries to the surface as a result of exposure to technological elements or goods (icing, slippery surfaces);
- cargo properties that affect the likelihood of emergencies.
According to the degree of consequences obtained and safety requirements during loading and unloading, they can be either harmful - those that, when interacting with an employee, lead to overwork, reduced labor productivity or the occurrence of an occupational disease (lung silicosis in miners, diseases of the urogenital system in drivers or electric locomotive drivers, etc.). Or dangerous - those that can lead to injuries at work, accident and even death (electric shock, explosion, fire, falling from a height of a heavy object). Safety measures during loading and unloading in this case are decisive.
Responsibilities of the leader, which contribute to the creation of normal working conditions
The employer ensures compliance with safety requirements during loading and unloading based on the requirements of the state labor code. He is obliged to create the necessary conditions at workplaces, when located in industrial buildings or structures, while servicing certain types of equipment, interacting with various raw materials.
The safety of actual cargo operations is ensured by:
- the choice of a rational technological system - technological processes, specialized tooling and equipment, optimal production area;
- the choice of a system for providing jobs - the rationality of the allocation of funds and objects of labor, the creation of optimal microclimate parameters of the working area;
- the choice of a rational protection system - rubber gloves and boots, gas masks and protective suits when working with aggressive environments;
- using the appropriate training system - a medical examination of prospective employees, their familiarization with the features of the functions from the position of labor protection.
SSBT: loading and unloading. General safety requirements
To create the most suitable production and service environment in terms of its parameters that meets numerous safety conditions, a system of special standards has been developed for cargo operations.
In general, safety requirements during loading and unloading operations require the use of special equipment for moving goods. If necessary, it is allowed to use manual transportation with the obligatory accounting of existing legislative acts. For safety, a rational choice of ways and methods of work, the type of equipment required, etc. is necessary.
Description of the stages of work
The presented system has a developed information management base for safety requirements during the loading and unloading operations. Let us cite as an example the most common points.
When performing the stages of unloading products and subsequent operations for their storage, the following should be considered:
- Operations regarding material assets are carried out, focusing on the standard numbers of individual industries and industry standards developed within the industry.
- They are carried out according to the developed schemes - using non-special means of transportation or to designated storage places.
- Heavy loads (above the standard values ββspecified in the instructions) must be laid on special gaskets that allow mechanizing technological processes.
- Shelves (racks) for the safety of materials must comply with state standards.
- If there is a need to store materials without racks, they are packed in boxes (boxes) and stacked in the form of a stack on pallets of the required dimensions.
- Observe the height from the floor level to the luminaires located under the ceiling in order to optimize the volume of the space, the absence of disturbances in work and safety during loading and unloading.
- The required linear dimensions of the aisles and driveways must be observed.
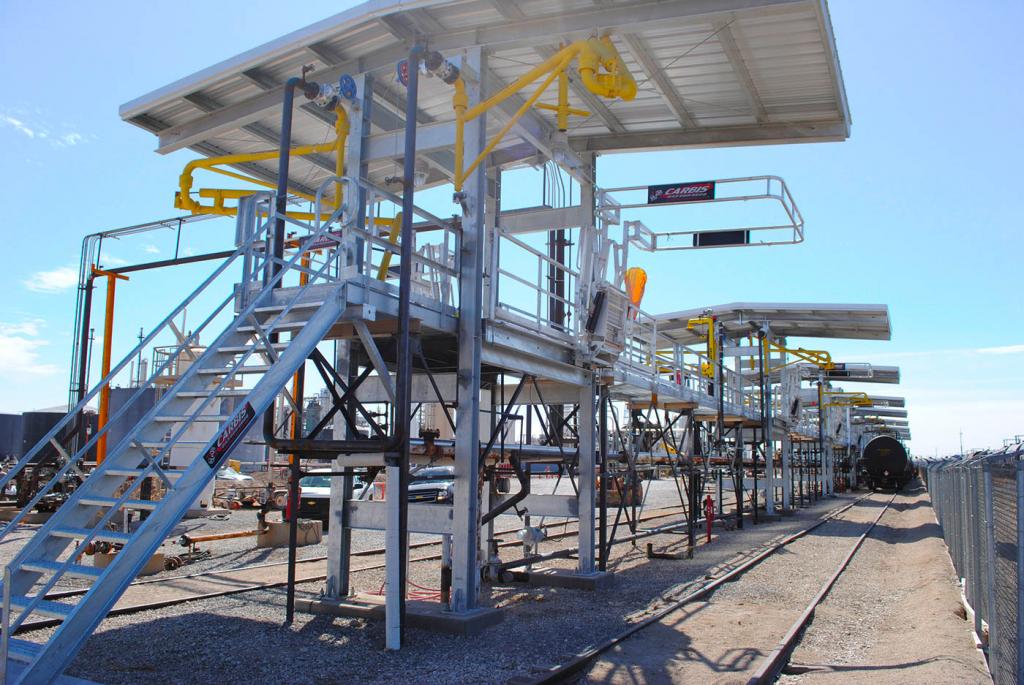
When loading material assets, loading and unloading operations according to general safety requirements are carried out as follows:
- Finished products are installed in special containers (for example, pallets), which ensures safety and reduces the number of additional movement operations. Pallets are manufactured in accordance with the requirements of NTD.
- Packaged goods are placed over the entire packaging area uniformly in location and density.
- When products (materials) are installed in containers (car bodies) without pallets, they are installed in rows of the same height with maximum use of the entire area.
- It is not allowed to place containers in transport with irregularities in the packaging process (leaks, weaknesses in coordination), to create empty zones in different parts of vehicles (containers).
- When carrying out cargo operations and moving the container with lifting equipment (gantry, bridge or other crane), a forklift or other means, workers are prohibited from standing on top of the container or doing work inside it.
Machine requirements
- Any designs for lifting materials or resources are used depending on the existing labor safety requirements specified in the technical conditions (for equipment of a certain type).
- The used equipment for lifting goods (elevators, cranes) must have a registration position in the technical supervision bodies and is subject to mandatory monitoring and inspection in the time and in the volumes determined by the relevant authorities.
- Technical control of equipment that is registered at the enterprise necessarily takes place at the right time (once every twelve months - partial, once every several years - full) for safety during loading and unloading.
- The condition of all snap-in units ensures operation and operation, with minimal impact on operators.
- Electrical parts have workable and undamaged insulation. Their design and the system for maintaining good condition should guarantee the trouble-free operation of various alarms about unforeseen situations, the trouble-free operation of control devices, incandescent lamps and other elements of the system. Should exclude the possibility of short circuit.
- On the equipment in the form of an information element, a characteristic of its rated carrying capacity must be present. Net and gross masses shall be recorded.
- The open-air areas for setting up vehicles must have a visual marking that defines the location of the vehicle and the required driveways.
- Electric vehicles, autocars (auto-loaders) should be inactive (off) in unoccupied time to exclude their use by non-core personnel, etc.

Features of the staff of cargo operations
- Workers who are engaged in cargo operations are required to undergo inspection and control in medical institutions to determine compliance and safety during loading and unloading.
- To the work of operators for servicing lifting equipment (crane operator, assistant, locksmith), slinger and electrician to monitor the technical condition and safe operation of elevators are allowed workers who are at least 18 years old. They must undergo special training and be certified in the appropriate institutions or technical schools.
- Obligations of the slinger can be performed by workers of other professions if they undergo training and subsequent certification.
- Drivers of electric cars (electric forklifts) must undergo training on the basics of electrical safety and have a certain qualification group.
- The operator of the vehicle is responsible for securing the cargo on a car (platform) and in case of violations that in the future will cause consequences during subsequent transportation, may require the shipper to eliminate them.
Operator Protection Tools
Safety requirements during loading and unloading operations are determined depending on the type of enterprise, the type of product with which cargo operations are performed (food in piece containers, acid in special containers, gas cylinders, etc.) and various technical features of the enterprise (type of lifting equipment, parameters of the cargo zone, layouts, etc.) The main task is to protect the employees of special services from the negative effects of materials and the processes of loading and unloading.
For example, you can specify the following requirements:
- The employer is obliged to provide employees with appropriate means (respirators, gas masks, rubber gloves and boots, protective overalls, helmets, etc.) that allow safe operations and minimize the risk of emergencies and work-related injuries.
- Workers are trained in the proper use of their protective equipment.
- Personal safety features are consistent with technical regulations, industry guidelines, and local guidelines.
- The indicated funds are prepared before the start of the planned work and are checked for the performance of their functions.
Hazardous materials
The processes of cargo operations are closely related to the requirements of fire safety during loading and unloading. Given the great risks and dangerous consequences in the event of an emergency, the requirements under consideration are categorical and unambiguous.
Here are a few features:
- All dangerous (fire hazardous) cargoes are presented for cargo operations only in specialized containers or packaging.
- Working areas of cargo operations must have the appropriate microclimate parameters.
- It is strictly forbidden to use open fire closer than 50 meters from the places of cargo operations.
- Operators (drivers) of vehicles do not have the right to leave it unattended during work processes (during the operations themselves, the engine of the machine is off).
- Cargo areas are equipped with fire prevention and protection equipment.
- Workers must strictly adhere to the recommendations and warnings indicated on the stamps and tags of the goods.
- Prevent the product (material) from falling to the ground, which will result in damage to the package or container, spillage and subsequent fire.
Conclusion
Safety requirements for loading and unloading are an urgent task for most enterprises in all sectors of the industrial complex. The creation of new materials, large structures, and products for critical industrial facilities (power plants, production facilities, etc.) requires constant improvement of the regulatory framework for cargo operations in order to meet the changing requirements of the production environment.