For the manufacture of a small number of plastic blanks, vacuum molding in silicone molds is most often used. This method is quite economical (the manufacture of a metal mold requires more time and money). In addition, silicone molds are used repeatedly, and this also significantly reduces the cost of production.
Plastic molding
The essence of plastic molding techniques is as follows. The molten material is located in the screw of the unit (special equipment for molding in silicone molds). Under the influence of the piston, the mass moves along the sprue channels, then fills the space of the mold. In this way, a casting can be obtained. When the plastic is heated, the atoms of which it consists begin to move randomly and randomly. However, upon cooling, crystallization centers begin to form. Crystals grow near the walls of the mold, then such a process also takes place inside the casting. At this stage, it is very important to observe the temperature regime, choose the right exposure time. Otherwise, plastic molding in silicone molds will be of poor quality, with visible signs of marriage. But, first of all, the molds themselves should be made into which the mass for crystallization will be poured.
Technology for creating molds
There are several ways to create silicone molds. The first of them is a solid fill. This method is suitable for simple designs: reliefs, souvenirs, two-dimensional details. The model is placed in the formwork, filled with silicone. Detachable forms are made like the previous ones, they are used for more complex forms. Two-part forms are produced in several stages. First, the first half of the workpiece is poured, after the hardening of the silicone, the mold is turned over and the second part is likewise made. In this method, it is very important to designate special locks on the basis (casting in a silicone mold of this type should occur without its displacement). Most accurately repeats all the details of the workpiece form "putty." A rather viscous silicone is applied to the part with a brush. The process takes place in several stages, this is necessary for the complete repetition of all the small nuances of the product. Moreover, the form itself is quite thin - from 3 mm. To keep it in shape, at the final stage an external hard shell is created.
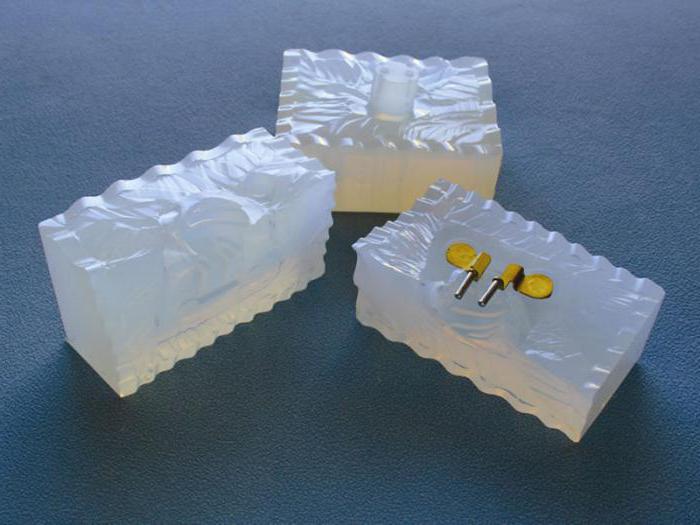
Silicone for making molds
Vacuum casting in silicone molds involves the use of various materials to create the matrix. One of them is Mold Star silicone. It is applied for continuous filling, rather strong and flexible. Hardening occurs at room temperature. For the “spreading” technique, the Rebount series is most often used. This silicone has a high viscosity, which can be controlled with a thickener. Casting in silicone form of this kind allows you to get a high-quality, durable matrix, and, accordingly, an ultra-precise part. There are also translucent silicones that are ideal for cut forms.
Casting materials
As a rule, polyurethane is used to make the parts themselves. The material has high impact strength, hardness, elasticity. Polyurethane rubber possesses higher tensile strength and tensile strength. Use them in the manufacture of various tapes, cylinders, dies, gaskets, bushings. Transparent plastic is also used for casting . It is quite resistant to ultraviolet rays and retains its transparency even when stained. Scope - lenses for various tests, prototypes in medicine, manufacturing of souvenir products, etc. As a rule, casting in silicone form involves the use of two-component mixtures, which directly include plastic and a catalyst.
Molding plastic into silicone molds. Equipment
Small-scale production of cast billets is a technological process that allows you to get a batch of exact copies of a part of any complexity. Very often, the technique is used to obtain prototypes that are tested before starting mass production, working out the appearance, design.
The equipment for industrial casting of plastic into silicone molds includes the following: a vacuum chamber (injection molding machine), a heating cabinet, and a vacuum mixer (mixer). Silicone is first prepared in a vacuum chamber where the material is degassed. This is necessary to prevent the formation of bubbles on the mold. After the mold has been made and preheated, polyurethanes (or resins for the final part) are mixed directly. This process takes place in a vacuum chamber. Through the gate, the mixture is poured into the mold. For final processing, it is necessary to place the workpiece in a special heating cabinet, where the product finally hardens at a temperature of 70 ° C.
Vacuum chamber Main characteristics
As a rule, automatic molding in silicone molds is used on a production scale. Equipment, namely a vacuum chamber, allows you to control both temperature and casting speed. The operator does not require special skills and knowledge, since all control comes from the operational system, which has both automatic and manual switching. There is the possibility of editing a given program. Various camera modifications are capable of producing workpieces up to 5 kg (for example, the ST-02 camera). The unit is equipped with an elevator for lifting silicone molds. It is worth noting that the ST-02 system allows the use of both small and fairly heavy matrices.
Another option is the MCP camera. This equipment for molding in silicone molds makes it possible to produce parts with thin walls and a complex configuration. This process is carried out due to differential pressure. Then the resulting cast is extracted, and subsequently it hardens in air. Vacuum casting in silicone molds for some types of plastics is completed in heating cabinets, which ensure uniform heating of the air, and, accordingly, the workpiece.
Finishing cast billets
After the plastic mass has completely hardened, it is carefully removed from the mold. The surface is machined, the protrusions are removed and cleaned, roughnesses are ground. If necessary, the workpiece is coated with either paint or other protective material. It is necessary to clean the silicone mold, remove the remaining plastic. Then it is washed, preparing for subsequent use. It is worth noting that molding plastic into silicone molds involves the repeated use of matrices (from 20 to 80 times).
The main advantages of the method
Small-scale production is developing dynamically, it allows you to qualitatively assess the market, test products, create unique copyright works in small quantities. Silicone molds that are used in plastic molding make it possible to completely copy the texture, shape, design of the workpiece. The part is easily freed from the matrix, which can also be used repeatedly. Castings have a minimum number of surface defects, optimal physical and mechanical properties. In addition, in some cases, even metal can be poured into silicone molds.
But the main advantage that casting in silicone molds is the price. The providers of this service indicate that the final cost of the workpiece will depend on the plastic material and on the volumetric parameters of the part (for example, a workpiece of 10 * 10 * 10 cm in size can cost 1,500 rubles). Silicone itself can be purchased from 500 rubles per kilogram, plastic - from 700 rubles. The cost of metal forms is quite high, sometimes their use is simply inefficient (if the circulation is several units). And silicone matrices are also suitable for home use, it is not necessary to buy expensive equipment. It is only necessary to independently make a model, take into account the life time of polyurethanes (the period when they remain liquid and suitable for pouring), observe all the technological nuances - and molding in silicone form can be carried out even at home. According to calculations, the cost of one workpiece in this case is about 70-140 rubles.