When welding the structure using direct current, it is important to know that the quality of the seam will depend largely on the settings of the device. An important nuance is that in addition to the current regulator, it is necessary to choose the correct polarity. There may be only two types - this is the direct and reverse polarity when welding with an inverter.
What does direct polarity mean?
In order to achieve a high-quality weld during welding of various steels, it is important to know which polarity is suitable for the material to be processed. The general essence of welding with an inverter is that the apparatus must have sockets "+" and "-". Depending on which socket the mass will be connected to, and to which the electrode, the polarity will depend.
Direct polarity is connected in this way: the mass is added to the positive socket, and the electrode is added to the negative socket. It is important to know that the nature and polarity of the current will be due to the existence of the anode and cathode spots. During the presence of direct polarity during welding, an anode spot that is hotter will form on the side of the workpiece.
What does reverse polarity mean?
With reverse polarity it is logical that the connection of the mass and electrode is interchanged. That is, an electrode is connected to the positive socket, and the mass is connected to the negative socket. Here you need to understand that when connecting the sockets in this way, the anode spot will also form, however, it will not appear on the side of the workpiece, but on the opposite side, that is, on the electrode.
Important notice! Manual polarity is connected only when welding with an inverter, that is, in the presence of direct current. When carrying out the same process, but on alternating current, the polarity is changed up to a hundred times per second independently. Therefore, the connection method does not matter.
As you can see, the difference between direct and reverse polarity when welding with an inverter is that the anode spot will form in different places.
Polarity Selection Criteria
When changing the connection, the specialist changes the place of concentration of the heat, transferring it either to the workpiece or to the electrode itself. It is important to know that the socket with a plus is responsible for heating, which means that with direct connection, the maximum temperature will be observed at the weld. When reconnecting, the maximum temperature goes to warm up the consumable element. Knowing this feature, you can independently choose a connection scheme based on such a parameter as the thickness of the material. The choice between direct and reverse polarity during welding will greatly depend on the thickness of the metal product. If this parameter is medium or high, it is best to resort to direct polarity. This is because strong heating of the workpiece will provide a deeper seam, which, in turn, will increase the quality of the weld. Direct polarity is also used if necessary to cut pieces of metal. And, on the contrary, when welding less thin metal billets, it is recommended to use the reverse connection, since the material will not overheat, but the electrode will begin to melt much faster.
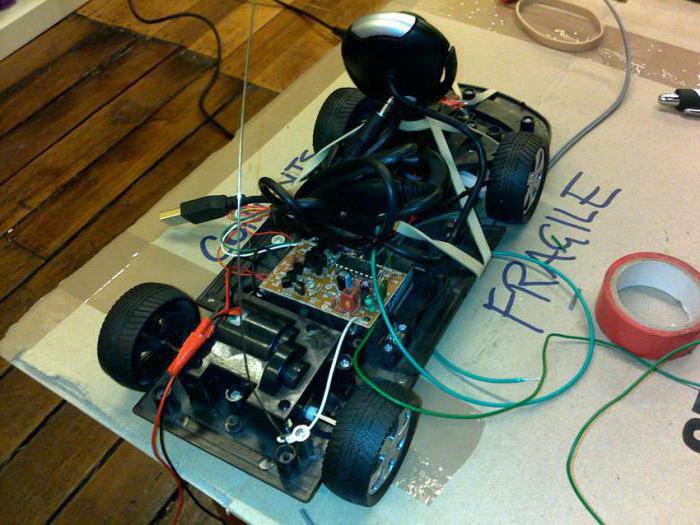
Metal type
Forward and reverse polarity during welding will also depend on the type of metal product that needs to be processed. It is important to understand that the ability to independently change the type of connection affects the efficiency of work with all kinds of blanks. An example is welding of stainless steel or cast iron. When working with such materials, it is best to use the reverse polarity, in which it will be possible to avoid strong overheating of the raw material, which eliminates the creation of a refractory weld. But, for example, for working with a type of metal such as aluminum, it is best to use direct polarity in welding. Since with little heating, it will be very, very difficult to break through the oxides of this raw material. Most often, for each material there is a recommendation that states what type of polarity is best to process this workpiece.
Types of electrode and wire
Another very important detail that must be taken into account when welding with an inverter of direct polarity or reverse is the type of electrode, which, like metal, has its own characteristics under different temperature conditions. Most often, the parameters are related to the type of flux used in the consumable base. Suppose there is a carbon-type electrode. It is impossible to use a reverse connection to work with such an element, since too much heating of a consumable of this type will overheat the flux and the product will become completely unusable. Only direct current welding with direct polarity can be used. Here, as in the case of metal billets, in order not to be mistaken, it is best to study the labeling and manufacturer's recommendations for working with each type of consumable separately.
Straight polarity properties
It is quite obvious that there are pluses when welding with direct and reverse polarity. If we talk about the first type of connection, then we can distinguish the following points:
- the resulting weld will be quite deep, but rather narrow;
- used for welding most metal workpieces, the thickness of which is higher than 3 mm;
- welding, for example, non-ferrous steel, is possible only with a tungsten electrode, as well as with a direct connection to the inverter;
- Direct polarity in metal welding also has a more stable arc, which, in turn, provides a higher quality of the weld;
- when using a direct connection, it is strictly forbidden to use electrodes that are suitable for welding with alternating current;
- Direct polarity has also proven itself in cutting metal workpieces.
Reverse Polarity Properties
Just as the direct polarity in welding has its strengths and weaknesses, the reverse connection can also be characterized by some properties:
- If you use DC welding, but make the reverse connection, then the seam will turn out not too deep, but very wide.
- The best quality of the weld is achieved only when working with metals having a small thickness, if the reverse polarity is used for welding thick raw materials, then the quality of the weld will be too unsatisfactory.
- When welding on the reverse connection, it is strictly forbidden to use electrodes that cannot be overheated.
- If the current strength decreases significantly, the quality of the seam will also deteriorate due to the fact that the arc starts to “jump”.
- Since the reverse polarity is most often used for welding high-alloy steels, it is necessary to be guided not only by the inverter welding rules, but also take into account the metal requirements for the duration of the working cycle, as well as for the metal cooling process.
Polarity reversal
After a person has studied in detail the features of welding with direct polarity, as well as with the opposite, it becomes quite simple to answer the question, why change it. Briefly summarizing, we can say the following:
The use of direct polarity is justified in cases of large metal thickness. Also, this type of connection is justified if non-ferrous metal welding occurs: brass, copper, aluminum. It is most important to turn your attention to working with aluminum, since its oxide film has a huge value of the melting temperature, which greatly exceeds the melting temperature of the raw material itself. In other words, we can say that the direct polarity during welding is a rough processing and connection of the structure.
The reverse connection, in turn, is used to work with thin steels. In addition, it is used in the processing of high alloy or stainless steel. These materials do not tolerate overheating, and therefore it is impossible to use melting with a high temperature. That is, work on the reverse connection is considered more subtle.
From this we can conclude that the answer to the question of why to change the polarity when welding with electrodes is that the quality of the weld seam, as well as the operability of the consumable itself, depends on this, since not all electrodes can be connected in the opposite way.
Conclusion
To summarize all of the above, the use of an inverter or a semiautomatic device for welding in everyday life is a very common thing. But here is the right choice of connection with direct current, as well as knowing what material should be cooked in what way - these are the basic information necessary for successful completion of work. If this knowledge is available, then the use of these tools will not be a problem.