In order to carry out gas welding without problems, the equipment must be equipped with a certain set of devices. One of the most important is the carbon dioxide reducer. This device is necessary in order to lower as well as stabilize the pressure of carbon dioxide, which comes from a gas cylinder.
Gearbox elements
A carbon dioxide reducer delivers carbon dioxide under a specific pressure. In addition, the same device shuts off the supply of volatile matter when it is necessary to finish welding. Structurally, this device consists of the following elements:
- gas inlet valve and sealing elements;
- chamber with a regulating type membrane;
- valve for gas discharge;
- two types of springs - top and control;
- fitting for connecting the welding machine;
- housing;
- two pressure gauges are required to monitor the pressure of carbon dioxide both at the inlet and at the outlet;
- shutoff valve.
The principle of operation of the device
It is best to consider the operation of a reducer for carbon dioxide on a conventional single-chamber device. Gas by pressure enters the inlet fitting. The incoming substance is controlled by pressure with a pressure gauge installed at the inlet. Once in the chamber, carbon dioxide exerts pressure on the spring, which is pressed down and thereby opens the passage into the chamber cavity. The carbon dioxide gearbox has a larger cross-sectional area than the nozzle's flow area, which causes the gas pressure in the chamber to drop significantly. The pressure drop is recorded by the second pressure gauge, which is considered the output.
Instrument adjustment
The adjustment of the gearbox to the carbon dioxide cylinder begins with the fact that it is necessary to adjust the tension of the main spring. To do this, there is an adjustment screw, and the tension force depends on what initial pressure is observed in the cylinder with a volatile substance. This spring will lower with the membrane under the action of carbon dioxide, passing this substance into the chamber to reduce pressure. This chamber is connected to a shut-off valve, as well as a hose, through which the gas flow will reach the torch of the welding machine.
Which gearbox for carbon dioxide to choose? When choosing this device, it is very important to pay attention to the fact that the membrane must be made of oil-resistant rubber, and it must also be very accurately positioned relative to the outlet. It is worth adding here that you can also use this type of gear manually. To do this, it is necessary to screw in or, conversely, unscrew the adjusting screw, based on the pressure gauge. Since a sharp increase in pressure in the chamber is possible, the reducer for carbon dioxide welding has a safety valve that protects the main membrane from rupture with a sharp increase in pressure. The safety valve will operate at the moment when the adjusting screw for some reason loses its tightness and more carbon dioxide than expected begins to flow into the chamber.
Design Features
To date, the main classification of gas reducers for carbon dioxide occurs according to three main criteria:
- The first is the number of working chambers of the device. To date, the majority of devices are available in a single-chamber type. However, if it is necessary to increase the functionality of the device in conditions of low ambient temperatures, for example, then it is better to use two-chamber devices. The working chambers in such units are arranged in a sequential manner.
- The second point on which the division into classes takes place is the working conditions. To date, three main groups are known - ramp, network and balloon. The ramp group of gearboxes is designed for operation in multipoint sites. Network devices, however, need power from a fixed network. Such a network is laid from a stationary carbon dioxide plant. In order to carry out welding work using carbon dioxide and a carbon dioxide reducer for a semiautomatic device at separate stations, balloon assemblies are used. However, such devices have lower specific gas flow rates, as well as a limited range of operating pressure.
- Gearboxes also differ in the principle of opening and closing the inlet valve. These elements can be either direct action or reverse. The principle of operation of the inlet check valve is discussed above, and as for the direct one, it is much less convenient in operation, which is why it is used extremely rarely.
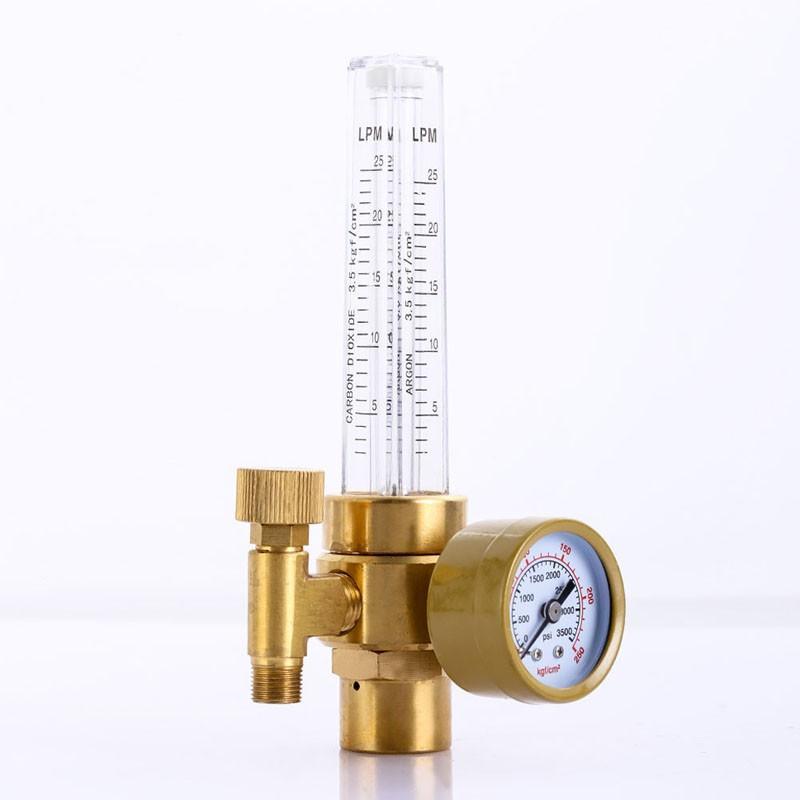
Is it possible to replace a carbon dioxide device with oxygen?
If we talk about the design, the gearbox for carbon dioxide is very similar to the gearbox for oxygen. The main difference between these devices is mainly in the way the valve is connected. Another difference is that a second pressure gauge is not always present with oxygen. Because of such small differences, the question often arises: is it possible to put an oxygen reducer for carbon dioxide or vice versa?
Instrument Requirements
Despite the fact that the equipment is very similar in design features, higher operating requirements are imposed on oxygen reducers. Such a difference is that O 2 , unlike CO 2, does not liquefy. Due to the absence of this effect, the pressure in the oxygen cylinder reaches 200 atm, while liquefied carbon dioxide is characterized by a maximum pressure of 70-80 atm. Because of this difference, if you install a carbon dioxide reducer on an oxygen cylinder, the sealing membrane will gradually break down. For this reason, such a replacement is not allowed, however, it is possible to carry out the replacement in the reverse order, that is, it is possible to install an oxygen reducer on a carbon dioxide cylinder.
Another significant difference lies in the method of attachment. Carbon dioxide reducers can be mounted with a collar, and oxygen reducers can only be attached with a union nut. This requirement is justified by the fact that with a CO 2 leak there is no danger of an explosion or a fire, as with an O 2 leak. Another small but important design difference is the cleaning filter, which is available in carbon dioxide gearboxes. The filter is intended not only for gas purification, but also in order to prevent the gas from being pushed back into the cylinder, where a surface cushion may form from gas that has left the liquefied state.
Gear Types
Today, domestic manufacturers produce several different models of gearboxes, among them such as BUO-5MG, BUO-5-4, BUO-5 MINI, UR 5-3, etc. However, among all types the most common and compact unit is like ur 6-6.
Features of the device UR 6-6
This model has certain features, because of which it has become so popular:
- Firstly, the case of this device is made of a special alloy, which gives a certain resistance to various thermal influences and mechanical loads.
- Secondly, the minimum indicator of pressure unevenness does not exceed 0.3.
- A fairly low pressure indicator is 1.2 MPa, at which a safety valve will already work.
- Like other devices, it has two manometers, which greatly simplifies the process of adjusting the gas pressure.
- The transmission capacity of this type of gearbox is much higher. It is capable of passing up to 6 m 3 of gas per hour.
- The cost of this device is about 1100 rubles, while the BUO-5-4, for example, costs 1700-1800 rubles.
Despite these differences, the process of selecting a gearbox is quite simple, since there is not much difference between them if you do not have to cook or cut metal at low temperatures. To work in moderate conditions, any device is suitable.
Heated Carbon Reducer
Today there are gearboxes from the manufacturer DINCONTROL, for example, the main difference of which is the presence of a heating system. These devices are intended not only to lower the gas pressure, but also to automatically control the flow of carbon dioxide. In addition, the equipment has a float-type rotameter and a gas heater. The presence of these elements provides accurate control of gas flow, as well as precise control of the welding operation time. In order to supply power to the heater, a 24 V AC power supply is required.
The case for such devices is made of very high quality metal, namely high-quality brass. The equipment is capable of ensuring safe operation with gas, the pressure of which will not exceed 200 bar. The gearbox cover is corrosion resistant and has a zinc coating inside. the presence of a rotameter on the device will detect even the smallest gas leak from the cylinder. There is also a safety valve that cannot be adjusted. It is configured for passive gear protection. Thanks to high-quality details, the device can be used in various types of climatic conditions. The temperature mode of operation is from -30 to +60 degrees Celsius.