High cost-effectiveness and efficiency of laser processing of metals has led to the fact that this method is used quite widely. Many industrial enterprises prefer this method. There are several different types of laser cutting. It is this operation that is the processing of metal products.
Cutting technology
During the application of laser metal processing, the product is exposed to such effects as reflection and absorption of laser radiation. Like any other production process, this proceeds according to a certain plan.
The first stage is the effect of laser radiation on the metal at a specific point. The second stage is that the metal first heats up under the influence of this beam, and after passing a certain temperature threshold it begins to melt. The third stage is marked by the fact that depressions appear on the boundaries of the melting of the metal. The last stage is that the energy emitted by the laser leads to the second stage of the procedure - boiling and further evaporation of the metal substance.
However, it is worth noting that in practice, according to the technology of laser metal processing, evaporation occurs only if the workpiece is made of a sufficiently thin metal. If it is necessary to process material with a sufficiently high density, auxiliary equipment must be used . Melting is carried out using gas, which acts as a secondary unit and helps to get rid of metal residues. This method is called gas laser cutting.
Laser design
The basics of laser metal cutting technology are also highly dependent on what the equipment is made of. Most often, the laser itself is structurally composed of three main parts. The first part is a special source of energy or a pumping system. The second part is the working fluid, which has the desired effect of stimulated emission. The last part is an optical resonator, which is represented by a set of several optical glasses.
Varieties of cutting equipment
The technology of laser cutting of metal, or rather, whether a particular processing method belongs to any type, is determined by the type of working element, that is, the laser, and also based on its power. There are currently three varieties of laser:
- Solid-state installations are those whose power is not more than 6 kW.
- Gas installations have a capacity of up to 20 kW.
- The most powerful units are gas-dynamic devices, the power of which starts from 100 kW.
The use of devices
Industrial enterprises most often resort to the use of solid-state laser metal processing. Cutting by such a device, or rather, laser radiation in this mode of operation, can take place both pulses and continuously. The main working fluid in such devices is ruby, glass with an admixture of neodymium or an element such as CaF 2 , that is, calcium fluorite. The biggest advantage of this setup is that it can create a very powerful laser pulse in a split second.
As for the use of gas lasers, they are most often used not at industrial facilities, but for scientific or technical purposes. When processing metal with laser machines of this type, a mixture of gaseous substances is used as a working fluid. Nitrogen, carbon dioxide and helium are used here. Atoms of these substances are excited by an electric discharge. This provides such positive qualities as monochromaticity, as well as directivity. These properties are the main advantages of a gas laser.
The highest power is in gas-dynamic lasers. The main working substance is carbon dioxide. The process proceeds as follows. First, the gas is heated to a certain temperature. After that, it is fed into a narrow channel in which the structure is expanded, as well as gas cooling. During this procedure, the necessary energy arises, which is used to carry out the laser cutting procedure.
What equipment for work consists of
The laser systems used for work consist of the following four key elements:
- A special emitter, in the role of which is a solid-state gas laser. It is important to note here that it must have suitable optical and energy parameters for the selected operating mode.
- Further, the presence of a system for moving and forming a beam and gas is mandatory. These elements are responsible for the transfer of radiation from the laser to the workpiece that needs to be processed, and is also responsible for changing the parameters of the gas supplied for operation.
- The third important element is the movement system. She is responsible not only for the movement of the laser, but also for the movement of the metal workpiece. Additional details in this system are the drive, motor and actuator.
- Naturally, such high-precision and insecure equipment has an automated equipment system - ACS. It is this system that controls the operation of the laser, as well as controls other systems of the machine. To carry out its work, it is additionally equipped with various sensors or the necessary subsystems.
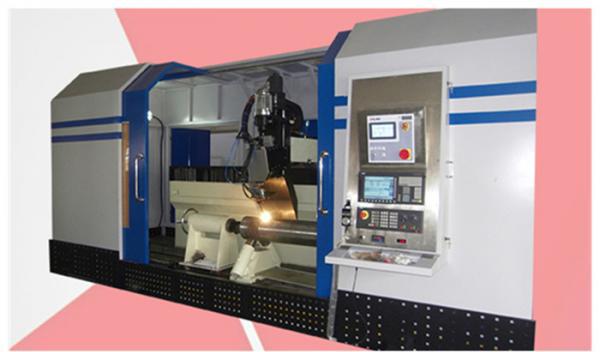
Thin metal work
Currently, laser metal processing is much more often used to work with sheet type of rolled metal. Raw parts with a large thickness are practically not processed by this method. Working with sheet metal also allows you to save some of the electricity.
It is also worth highlighting several advantages that this sheet metal cutting operation has:
- ensuring high accuracy of material supply, as well as the laser itself;
- on the surface of the part remains a minimum of contaminated space after work;
- a rather low probability that under the influence of the laser will cause any unnecessary harm to the workpiece;
- It is possible to create fairly complex and voluminous parts with high speed.
Laser Applications
Currently, the use of sufficiently high-precision equipment for laser cutting is necessary in order to create the following structures:
- the creation of a variety of parts for mechanical engineering;
- creation of various shelves, shelving and other structures used in the trading industry;
- some elements of the chimney, stoves and boilers are created using laser cutting;
- forged fences and some details for gates and doors;
If we take into account all the advantages of laser processing of metals, it becomes clear why many enterprises are switching to this particular method of working with thin sheet metal.
Laser processing of metal from rust
The principle of rust removal using laser equipment is based on the known physical properties that arise from the interaction of metal and bright light radiation, such as a laser. In accordance with these laws, pure metals will reflect light radiation, but the presence of any chemical impurities will, on the contrary, absorb light radiation. Chemicals include more than rust. Hydride films and other contaminants can also be removed in this way.
During the absorption of laser radiation by a metal surface, one of three scenarios occurs:
- Heating takes place without phase transformations. In this case, a layer of chemical contamination, which is affected by directed photon beams, will absorb and exfoliate them.
- Possible heating followed by melting of the substance.
- It is possible that heating will be accompanied by further evaporation of the substance from the surface.
Laser rust cleaning technology
Given the possible development options, we can say that there are two ways along which the process of cleaning from rust can proceed. In the first case, the technology of using the laser is "soft", that is, the surface layer will be separated from the metal base in the form of flakes. The second case is called "hard." It is characterized in that the rust present on the surface of the metal simply evaporates when exposed to the laser.
Depending on the chemical composition of rust, its melting temperature is from 1580 to 1640 degrees Celsius. In other words, it is necessary to develop a temperature that will exceed even the rate required for steel melting. In order to achieve the desired indicator, it is necessary that the laser power in the coverage area reaches 10 6 W / cm 2 . In this case, the diameter of the ion-photon beam should be at least 100 mm. With such indicators, it becomes possible to effectively remove the oxide film with a thickness of 50 to 75 microns. This is quite enough to remove rust from the surface of the metal.
Rust remover
Naturally, it is impossible to use the same rust removal equipment as for cutting. It is also worth noting that the price of laser processing of metal from rust is quite high. The cost varies, but the minimum amount is within 10 thousand rubles, and also depends on the area of ββthe metal billet that needs to be processed.
Currently, the most popular equipment option is a portable machine. It consists of two separate modules. The first module is a satchel with a power source, and the second module is a laser head with a sludge trap. Both modules are interconnected using fiber optic cable. In addition, a video system is also included in the set of such equipment, which allows you to monitor the progress of the rust removal process.
Do-it-yourself laser types for cutting metal
As varieties, the same settings are used as in industrial enterprises. However, some of them are too powerful and complex to be able to make them yourself. For this reason, only the simplest and most low-power solid-state laser is popular. Although it will be fair to note here that the power of a solid-state self-made laser does not compare with the power of a similar type, but a production option. However, such an installation is quite suitable for domestic use, moreover, it is much cheaper.