The Fe fe3c diagram (iron-cementite) is of extremely practical importance. After all, alloys based on iron and carbon are the most common and widely used material in the manufacture of machine parts and mechanisms. This is due to the fact that iron ore is much more common in nature than ores of other metals and elements in their pure form. The smelting volumes of ferrous alloys based on iron and carbon are ten times higher than the volumes of metallurgical production of non-ferrous metals. The Fe fe3c diagram for steel and cast iron allows you to set the mode of quenching, tempering, and annealing of parts and workpieces. If you did this without taking into account the structural features and phase composition, then the obtained properties will most likely not satisfy the design requirements, and the material itself will be either very hard and brittle, or too plastic and subject to wear.
Historical excursion
The founder of modern metal science is D.K. Chernov. He made a huge contribution to the development of the science of metals. In 1868, his scientific work devoted to the problems of obtaining products and steel and metallurgical production was published. All experts and historians of technical sciences unanimously argue that this work laid the foundation for a systematic and comprehensive study of iron and carbon based alloys.
In the aforementioned work, Chernov indicates that for iron-carbon alloys there are some critical temperatures, upon reaching which the properties of steel and cast iron change stepwise. He also revealed the dependence of the position of critical points on the carbon content. In other words, the scientist made the first attempts to construct the Fe fe3c diagram.
We should pay tribute to D.K. Chernov. He was able, without having any equipment at hand, to determine the position of critical points. He noted that when certain temperatures were reached, the glow pattern of the tested samples changed. This circumstance became the basis for a more in-depth study of the properties of metals and alloys.
The names of the phases and components of the iron-carbon alloys were assigned by the French scientist Osmond. He, like Chernov, was able to determine and fix the position of critical temperature points. Only he was guided not by the colors of red-hot, but by the readings of the pyrometer, which was invented shortly before he began the research.
The German scientist P. Gohrens managed to summarize the experience of his colleagues and build a Fe fe3c diagram close to its modern version at the beginning of the 20th century.
The most important discoveries were made in the last quarter of the 19th century. Of course, technology does not stand still, and today researchers have more advanced equipment. And yet, today we can only talk about the addition and refinement of information on iron-carbon alloys. The modern Fe fe3c diagram is not much different from its first options. Currently, only additions may be made. Although they are important (sometimes), they do not carry any fundamentally new information.
Structural components of the Fe fe3c diagram
The figure shows an iron-carbon diagram. The solubility of carbon in cementite is 6.67% by mass and 25% by number of atoms. Alloys that contain more than 7 percent carbon are not used in technology and therefore are not well understood. Only materials with a carbon content of up to 6.67 percent found practical application in engineering and other sectors of the national economy.
Above ABCD, the alloy of iron with carbon is in a liquid state of aggregation. This is the so-called liquidus line. Below the broken line AHJECF, the entire alloy crystallizes. Thus, all alloys below the indicated line exist in the solid state.
Iron, in addition to the ability to form chemical compounds with carbon (including Fe 3 C), may, depending on temperature, have various crystal lattices (allotropic modifications). With this in mind, the following phase components are distinguished in the diagram of alloys of the Fe fe3c system: austenite, ferrite, cementite, and the liquid phase.
Austenite Overview
Austenite is a solid solution of carbon in ferrum (iron) with an fcc lattice. In the Fe fe3c diagram, austenite is limited to the NJESG figure. This phase is indicated by the capital letter A, the Greek letter gamma γ, or the chemical formula Fe γ (C). However, austenite can exist not only in its pure form, but also form mixtures with other structural and phase components. Thus, the region of existence of austenite as such is not limited to the NJESG contour. At certain temperatures, austenite is formed at any carbon concentration (non-zero, of course).
Ferrite Overview
Ferrite is called iron with a body-centered cubic lattice (denoted by the symbols Fe α , simply α, or the capital letter “F”). The solubility of carbon in ferrite is negligible (not more than two hundredths of a percent). If you look at the Fe fe3c diagram, you can see that the ferrite region on it is indicated by the QPG and NHA contours. However, individual ferrite grains are also present in other areas of the diagram. In particular, the structural composition of hypereutectoid (carbon content less than 0.8 in a percentage ratio) steels is ferrite + perlite. It should be canceled that pure ferrite is also present in perlite. Perlite is known to be a mixture of thin ferritic and cementite plates. However, after a certain heat treatment, these plates coagulate (fold). This structure greatly improves cutting performance.
Cementite Overview
Cementite has a very high hardness. In the Fe3c diagram for steel and cast iron, the vertical line LKD corresponds to this chemical compound. Thus, cementite contains about 7% carbon (6.67, to be exact). The chemical formula is Fe 3 C. Thus, this chemical compound contains 25 percent carbon atoms, and the rest is iron atoms (one carbon atom per ferrum atom).
General information about the liquid phase
The melting temperature of steels may be different. Cast irons, as can be seen from the Fe fe3c state diagram, begin to melt upon reaching a temperature of approximately 1150 degrees Celsius (this value corresponds to the ECF line in the diagram). It should be noted that the melting points of cast irons are much lower than the melting points of steels, which led to the use of high-carbon alloys as the main casting materials to obtain products of complex geometric shapes.
Peritectic reactions in iron-carbon alloys
On the state diagram, Fe fe3c immediately catches the eye with three horizontal lines: PSK, ECF, and also HJB. These are the lines corresponding to the so-called peritectic transformation.
In the upper left corner is the HJB line. It corresponds to a temperature of approximately 1,500 degrees Celsius. Only iron and carbon alloys undergo this transformation, the carbon content of which does not exceed 0.5 percent.
As a result of cooling the liquid alloy below the indicated temperature indicator (or even when the temperature reaches 1499 degrees Celsius), the liquid and ferrite form austenite. At various carbon concentrations, the conversion result can be different: ferrite + austenite, 100% austenite, as well as liquid + austenite.
A similar invariant reaction proceeds when the horizontal ECF line is crossed (corresponding to a temperature of about 1150 degrees). In this case, austenite can form a mixture of ferrite and cementite. This horizontal extends only on the pig-iron section of the state diagram of Fe fe3c alloys, i.e., such transformations are absent in steels. The resulting mixture is called ledeburite (in honor of the German scientist Ledebour who discovered this transformation).
And finally, the third horizontal is PSK. It corresponds to a temperature of 727 degrees. When cooled, ferrite and cementite (Fe with Fe 3 C) precipitate from austenite. The state diagram shows that the transformations at the intersection of this line are characteristic of all sections. However, it should be remembered that this is true only for alloys of iron with carbon. If the alloy is alloyed with additional elements (chromium, manganese, nickel, etc.), then the fe fe3c alloy diagram can no longer be followed. Material science and its modern methods cannot give an exact and comprehensive answer to the question of why this is happening. It should be said that the transformation occurs both during heating and during cooling of the alloy. The decomposition product of austenite during cooling is the so-called perlite (a mixture of cementite and ferrite). When heated, the reverse reaction obviously occurs - cementite dissolves in austenite according to a certain (rather complex) mechanism.
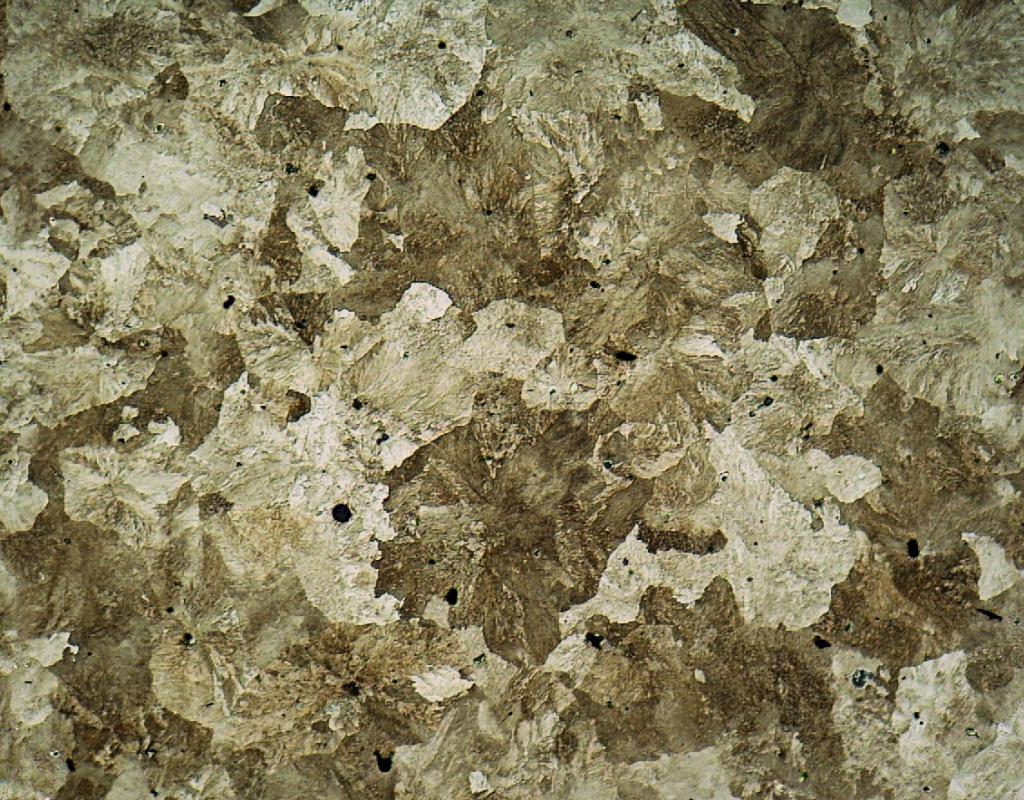
Features of crystallization of alloys of the steel section of the diagram
The crystallization of alloys that contain a small amount of carbon (less than one tenth of a percent) ends at rather high temperatures and corresponds to the AH line in the Fe fe3c diagram. The cooling curve is built according to generally accepted norms and rules: when crossing horizontal lines, lines are drawn at an angle of 180 degrees (horizontal). This is due to the so-called physical phenomenon of the secretion of latent heat. This phenomenon manifests itself in the fact that when the alloy cools down for a certain time, the temperature remains unchanged. The answer should be sought in the distribution of free energy of free atoms.
In an alloy containing 0.1 - 0.16 percent carbon, δ-iron crystals with a body-centered cubic crystal lattice begin to precipitate when the AB line is reached. The crystals mentioned occur in the liquid phase, and the centers of crystallization are non-metallic inclusions (this is characteristic of alloys with any concentration of carbon). With further cooling, the solid phase changes composition along the solidus line, and the liquid phase changes along the liquidus line. When the temperature reaches one and a half thousand degrees, the system is in equilibrium: the carbon content is 0.1% in the solid phase (corresponds to point H), and in the liquid phase it is 0.51% (corresponds to point B). At this temperature value, the peritectic transformation previously considered takes place. The result is a solid mixture of austenite and ferrite crystals. The alloy, which contains 0.16% carbon, as a result of cooling and peritectic transformation contains 100% austenite, without ferrite inclusions.
In that case, if the carbon content in the alloy is 0.15 - 0.5%, then a solid austenitic phase forms as a result of cooling below 1500 degrees Celsius, however, a certain amount of liquid remains in the structure (it depends on the percentage of carbon ) The crystallization process will be completed only when the solidus (JB) line is reached on the state diagram of Fe fe3c. In this case, the cooling curve can be drawn according to the general established rules for their construction. Moreover, after complete solidification, the alloy form a homogeneous phase structure consisting of austenite.
If the carbon content in the alloy is from 0.51 to 2.14%, then their crystallization occurs in the interval between the bounding lines JE and BC. After crossing the BC line, austenite crystals appear, which grow with decreasing temperature. Accordingly, during cooling, the carbon concentration in the liquid changes along the liquidus line, and in austenite - along the solidus line.
Features of crystallization of the cast iron plot
As you know, an alloy of iron with carbon with a content of the latter of 2.14 percent is cast iron. This distinction is not accidental. If we draw a diagram of Fe fe3c, it becomes clear that the boundary between steels and cast iron corresponds to the maximum solubility of carbon in austenite. Therefore, during the crystallization and solidification of steels in their structure there is no such component as ledeburite (this is a mechanical mixture of pearlite and cementite components, named after the scientist Ledebur). Ledeburite is very hard, and its presence in the structure of the material has a negative effect on a number of technological properties (first of all, the ability to deform under the action of loads). On the other hand, cast irons have very good casting properties (liquid cast iron manages to fill all the distant cavities of the foundry sand form before it begins to harden).
Depending on the speed and cooling conditions, ledeburite may have a different structure. So, with accelerated cooling, cellular ledeburite is formed. These are, in fact, cementite plates on which austenitic crystals are formed. Lamellar ledeburite consists of very thin cementite formations, separated by similar formations of ferrite. If you make a thin section of a sample of eutectic iron, which was cooled under certain conditions, polish it and etch it, then in the lens of a metallographic microscope you can see plates of ferrite and cementite, alternating between each other.
Structural and phase transformations after solidification of iron-carbon alloys
As mentioned earlier, iron has an interesting feature - the ability to rearrange atoms. The lattice of ferrum (iron) can be bcc (volume-centered) and fcc (face-centered). Researchers and scientists in the field of materials science argue that under ultrahigh pressure (several thousand atmospheres or more), iron atoms can also order and form a hexagonal close-packed lattice.
The transformations of the solidified alloy are described by the following lines of the diagram: NH, NJ, GO, OS.
The NH line is the boundary of high temperature ferrite and austenite. When the alloy cools, ferrite and cementite are formed from austenite. However, this is true only at very low cooling rates. If the cooling rate is higher than critical, then metastable martensite with incredibly large residual internal stresses will form by the shear mechanism.
The NJ line is also a kind of boundary between the existence of ferrite and austenite. When this line is reached, the phase transformation process is completed.
The MO line corresponds to a temperature value of 727 degrees. In some sources, it is also called the Curie point (in honor of the researcher who discovered this phenomenon). When heated above a temperature of 727 degrees Celsius, iron and steel lose their magnetic properties. This phenomenon is very interesting and has not yet been fully studied.
The GOS curve corresponds to the critical temperatures of the austenitic-ferritic transformation. The point AC 3 in the Fe Fe3c diagram indicates the temperature at which the conversion of ferrite to austenite begins to proceed. But the point AC 1 denotes the temperature at which the reverse transformation begins to take place - at the grain boundary of high-temperature austenite, pearlite formations nucleate and grow. The fact is that on the diagram lines indicate the equilibrium state. And in order for the corresponding transformations to begin to proceed, it is necessary to provide some supercooling, or vice versa - overheating.
Steel containing 0.8% carbon is composed entirely of perlite. The transformation of perlite into austenite and vice versa in such materials does not occur simultaneously, but in the temperature range. At the same time, carbon is redistributed to honey in two phases.
In the state diagram of the Fe fe3c system, the SE line corresponds to the maximum possible solubility of carbon in solution. This explains the beginning of the allocation of cementite from austenite. Cementite in this case is called secondary, since it is released from the solid phase. At certain carbon concentrations (this applies to cast irons), cementite is released from the melt. Such cementite is called primary. There is also tertiary cementite. But this is a separate issue. Upon reaching the GP line, the conversion of austenite to perlite is completed. This is if the alloy is cooled. When heated, everything is exactly the opposite, and upon reaching the indicated line at the grain boundaries, new austenite grains begin to nucleate and grow.
Carbon, depending on solubility, can change its concentration and is gradually redistributed. PQ. Fe fe3c . , , . , .
0,2 , . - . ( , ). . , ( , - , ).
, Fe fe3c, , . – . «».
. , . . , . . . , . . . , . .
Depending on the shape of graphite inclusions, cast iron is divided into gray (lamellar form), malleable (flaky graphite inclusions) and malleable (or bovine eye - spherical inclusions). The shape is determined by the annealing conditions, as well as by additives added to the melt.