Gas lift production of oil and gas resources can be considered as a more progressive alternative to the traditional method of fountain well development. It is distinguished by elements of passive extraction of target materials, which is facilitated by gas energy. This feature of gas lift well operation also determines the specifics of the technical organization of the production process, which is directly reflected in the characteristics of the equipment used.
Principles of production in gas lift wells
The technology involves the rise of formation water or oil from the channel due to excess pressure in the well, which is created by gases. It also requires the connection of active mixtures - in particular, associated gas compressed by the compressor method. In some deposits, air under natural pressure also acts as an active agent. Using a compressor is optional. Its introduction into the technological process largely depends on the requirements for production volumes and the capacities of the equipment used. In any case, the main functional principle of the gas-lift method of operating the well is to ensure the process of aeration of a liquid resource. The pressure in the well will decrease as gasification builds up, therefore, artificial (compressor) compression of the mixture may be required to increase pressure. The volume of inflow on the surface directly depends on the current gas lift parameters, which can be regulated by working equipment.

Differences from the operation of fountain wells
By and large, a gas lift is the same fountain method of production, but with an additional stimulator of flow. Active gas is directed from the surface along the wellbore to the shoe, where the enrichment effect occurs, which reduces the effort required to raise the resource. Obviously, such a solution needs to connect additional capacities - including the function of pumping equipment. Moreover, in some configurations, a separate gas supply channel is also required. But there are fundamental factors in which it becomes impossible to operate the well in a fountain way. The gas-lift method of production is a non-alternative replacement for the fountain in the following cases:
- At high fluid temperature.
- With a high gas content of the extracted resource.
- In the presence of sand in the face.
- In the presence of salt deposits and paraffin.
In other words, everything that complicates the operation of pumping equipment during well servicing, to varying degrees, necessitates additional stimulation of raising the fluid resource.
The technology of using gas-air mixtures
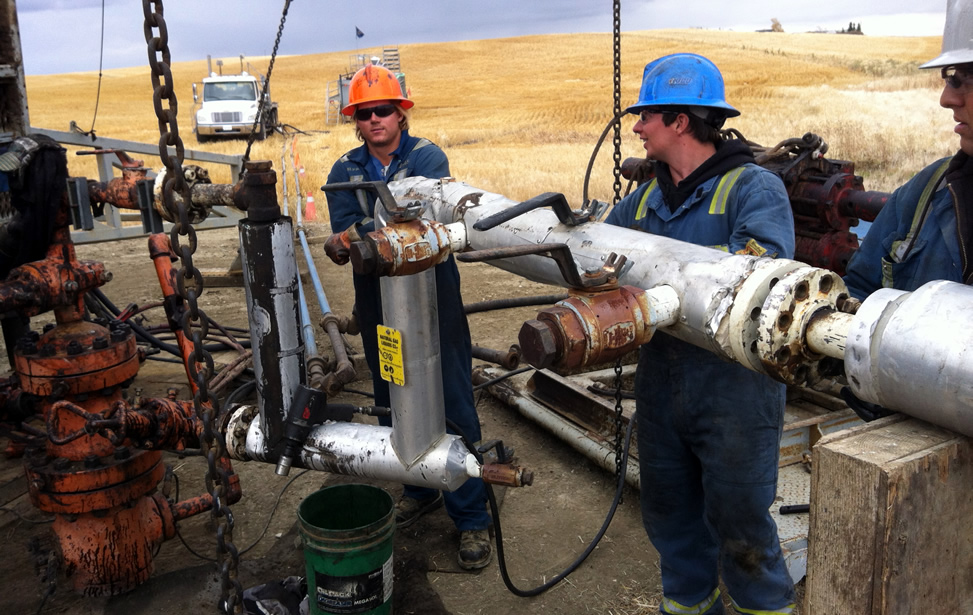
The launch of air into the well with the liquid contributes to the formation of a stable emulsion, but this is not enough for subsequent operations with the resource. Typically, surfactants are added in combination to heat and maintain sludge. In the process of separation already on the surface after extraction of the solution, conditions are created to prevent fire, since gas-air emulsions are easily ignited. As for the gas component, hydrocarbon mixtures are most often used. This decision is justified from an economic and technological point of view. The fact is that gas-lift operation of wells with hydrocarbon inclusion requires less resources to ensure separation and separation processes. On the surface, the enriched liquid itself is separated into conditioned pure oil and gas, which is explained by the low oxygen content in the composition. The spent hydrocarbon is then collected in a special reserve and disposed of. Depending on the quality of this gas, it can be used to produce unstable gasoline.
The device used equipment
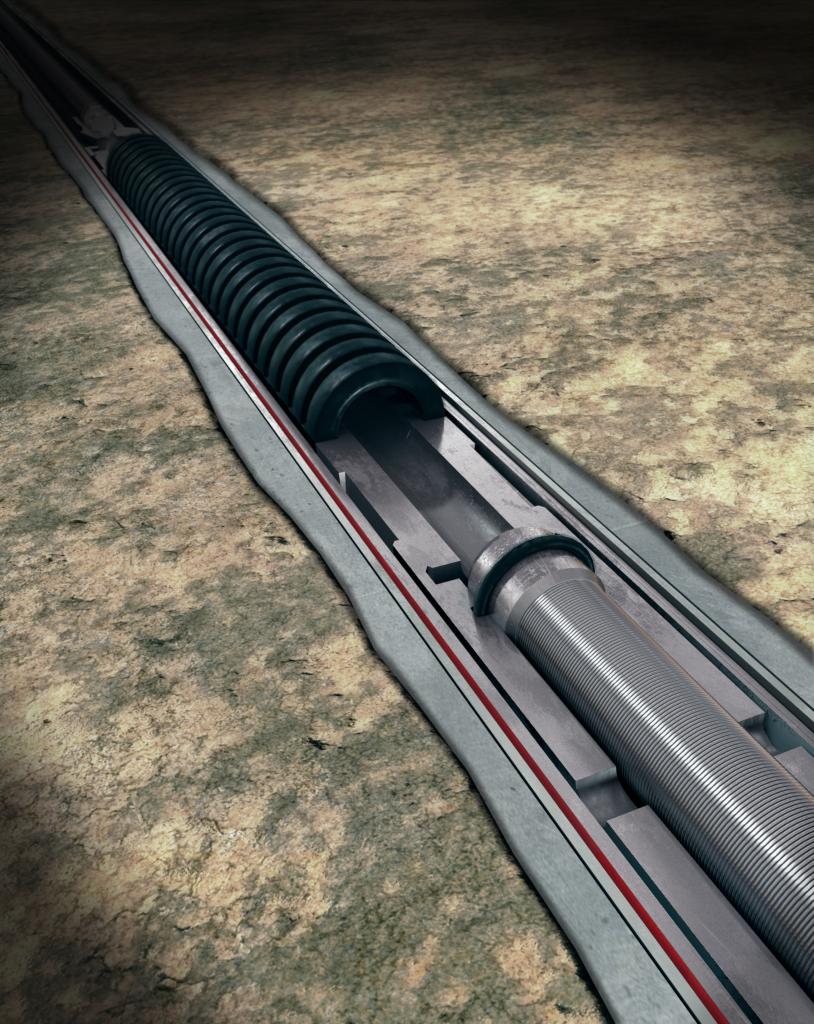
The infrastructural basis for the operation of the well is formed by annular rigging, directly pipes and pumps. This system provides the possibility of fluid flow inside the barrel and its further rise. The column of the raised liquid is regulated by shutoff valves with valves at several levels. By controlling this equipment, the operator can reduce or increase the power flow depending on the current parameters of gasification of the resource, which naturally affect the intensity of the rise. In the operation of fountain and gas lift wells, equipment for measuring performance indicators can also be used. In particular, manometers for determining pressure and multifunctional devices for taking hydrostatic and temperature indicators into account are used. To a greater extent, the presence of these devices is dictated by safety considerations, but knowledge of the pressure value is necessary as a factor in the regulatory process. In systems with automatic control, pressure gauges can, without operator intervention, affect the change in the flow movement parameters. Such a scheme is used in conditions of high-tech industrial development of deposits, where the flow rate is also compulsorily kept.
Preparation of equipment for work
Pipes and valves with associated accessories are allowed to the working process, which in principle are able to work under conditions of design pressure values. For example, according to the preliminary calculation results, the valves undergo special tests at the stands, where the accuracy of their operation and resistance to mechanical loads are evaluated. All technological equipment is subjected to hydraulic tests with loads in which the gas-lift well with specific characteristics will be operated. At this stage of preparation, the main parameter of the test is the tightness of the equipment.
Organization of the operational process
After successful testing, the equipment is sent to the well. The crosspiece of the mounting fixture is fixed on the flange of the column head. Next, the following components of the technical infrastructure are immersed in the barrel:
- Packer with nipple.
- Directly nipple.
- Downhole chamber (complete with valves).
- Shutoff valves.
At the final stage, the installation of ground reinforcement with crimping equipment and equipment for gas separation and removal is carried out. After connecting the pump, the gas-lift well is put into operation with the subsequent supply of a working agent. From this moment begins the constant monitoring of the state of the valves and pressure in the chambers of the well. When the liquid rises to the first working valve, the equipment automatically switches to steady state production.
Downhole chamber and its varieties
This functional device is a welded structure containing a nipple, a jacket, guiding elements and a pocket. Its base is an oval pipe with a window to which a pocket is welded. Guides for overflow are also located in the same part. The nipple, which is located inside the upper end of the shirt, is designed to fix the direction of the gas lift pocket with a valve. In the system of operation of a gas-lift well, the chamber occupies a place under the tubing - it is pointwise positioned under the current liquid level. In practice, cameras of different types are used, which differ in their construction device, installation method and the presence of additional regulatory equipment.
Well chamber operation
Before entering the working process, the camera is inspected and checked for leaks in the inlets. In some configurations, the device is previously docked to the well pipes through threaded connections. To supply gas through the chamber, special nozzles with valves are connected to the side openings on the housing. During the operation of equipment for gas lift wells by means of installed pipes and a bellows, aeration of the oil resource is carried out already at the bottomhole level to the desired coefficient. As the fluid rises, the gas flow rate can change by adjusting the position of the valves. In case of an accident or after the complete cessation of gasification of oil in the pockets of the chamber, a blind plug is mounted.
The device of gas lift valves
In this case, the valve acts as the central regulatory link, providing the function of regulating the process of enrichment of the liquid with gas. The design of this element is quite simple - the stem-saddle combination and the mounting fixture form its basis. With the gas-lift method of operating oil wells, a non-return valve can also be used. This modification contains in the design a housing and a locking tip, designed to completely stop the flow. Unlike plugs, the non-return valve does not change the position of its structure and, depending on current needs, can open to return fluid.
The principle of operation of gas lift valves
In normal condition, the valve holds the outlet openings of the chamber, constantly being under pressure of a gas-liquid mixture of a certain size. As the bellows load rises to the set value, the valve automatically opens. It releases the mass of the working agent into the liquid, maintaining this mode until the load again drops to the intended level. Also, the valve function during the operation of gas-lift oil wells can be controlled by the pressure of the injection gas from the back side. In such a system, an unbalanced scheme of controlled shutoff valves is used.
Conclusion
Using the traditional method of operating fountain wells is considered the optimal solution in most cases of field development. Its technical organization does not require the connection of sophisticated equipment, but in the context of systematic production at large fields, this system is irrational. In turn, production in gas-lift wells with periodic operation demonstrates technical and economic efficiency in the fields, where there is a decrease in flow rate at a level of less than 50 tons / day. The justification for the application of this method is determined by a more advanced system for regulating production by controlling the intensity of the rise of the resource. The ability to control overflows requires large technical and energy investments, but even in conditions of increasing organizational costs, gas-lift wells are more efficient.