Most often, to work with metal blanks, a person needs a machine for bending metal. This is a fairly simple device, but its benefits can hardly be overestimated. In addition, making it yourself is quite possible. This will save a significant amount of material resources, but it will also require certain knowledge, skills and, of course, time.
Description
A machine for bending metal, as its name implies, is used to produce bent metal parts. It is worth adding that, in addition to this function, it can also have one additional - cutting material. Such machines are most often used to make strips of metal. In addition to these two functions, the presence of such a machine will allow the production of various kinds of shaped metal. The advantage of using a metal bending machine is that it allows you to change the shape of the material at any desired angle, but it does not harm the surface coating or protective layer of the product.
Work on the unit
You can work on such a machine not only with steel products, but also with copper, brass, aluminum and iron. If a workpiece made of any material is characterized by the fact that its thickness is less than 0.8 mm, then its width must be at least 40 cm, but also not more than 2.5 m. With such dimensions, the height of the shelf (for folding) should be no more than 2 cm. If you want to cut workpieces with the same thickness, it is important that their width is from 80 mm to 40 cm and no more.
Another important condition that must be observed in order to work on a metal bending machine is the absence of defects on the surface of the sheet that will be bent. Compliance with this condition is important so that those parts and product samples that will be produced on a do-it-yourself machine do not inferior in quality to those blanks that are produced on an industrial scale in factories. In order to protect the polymer or paint coating on the material itself, it is recommended to install silicone or rubber substrates on the machine.
The design of a do-it-yourself sheet metal bending machine
A homemade machine for bending metal products has a rather simple, but very functional design, consisting of several basic elements.
Knife. Since the machine has an additional cutting function, this part is also the main one. It should be installed on movable rollers, and is intended for cutting workpieces. It is important to note here that this element must be made of very strong steel, according to the Rockwell scale, the strength level should be about 100. The service life of such a product is quite large, but it will be difficult to sharpen it. But this drawback is completely offset by the fact that the knife will allow you to cut a huge amount of linear meters of material before dulling. To make it easier to move the rollers, a weighting material should be installed on them.
Machine parts
A do-it-yourself metal bending machine should also have several of the following components:
- A necessary part is a work beam (table). The purpose of this element is quite understandable, it plays the role of a work surface on which the workpiece lies. The beam width can be almost any. It is worth noting that if the dimensions are quite large, then a machine for bending metal with your own hands can be turned into a full-fledged workbench. Masters recommend making or covering the surface of the beam with rubber or silicone, so as not to scratch the surface of the workpieces.
- Next is the sheet bending machine itself. The design is quite simple and should be made in the form of a frame made of wood material, and also have a weighting agent.
- It is necessary to acquire various supports and stops that will prevent the material from slipping.
- Another important element is the stops for folding the sheet. These parts will adjust the bend width of the sheet and set the bend angle.
- In order to cut the workpieces, it is recommended to add stops to indicate the width of the cut.
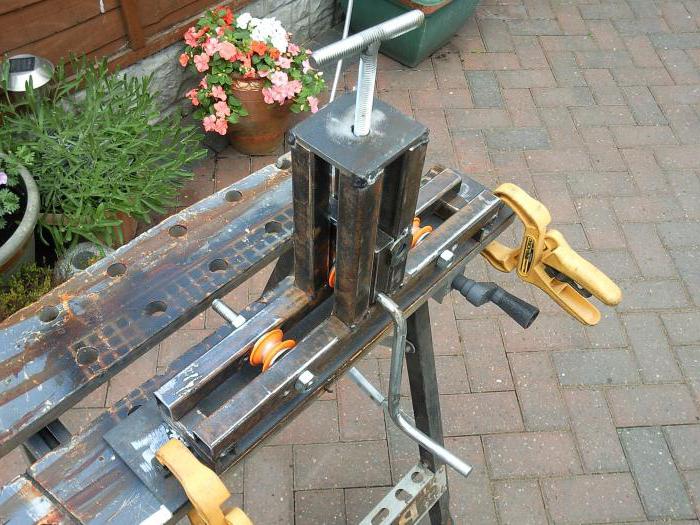
Start of manufacturing a homemade metal bending machine
It is recommended to start work by drawing up a diagram of the unit. It is also necessary to purchase and manufacture all the necessary elements and parts before proceeding with the assembly. The first thing you need to buy is two pieces of channel number 5 and number 6 with the same length. Also, these two elements must have a straight edge. These elements are used to prepare the base. Piece No. 5 is used for clamping, and No. 6 is used to equip the base. To choose the length of the channels, it is necessary to start from the length of the workpieces with which it is planned to work, this parameter must coincide. Most often, experts recommend taking a length of about half a meter. This is enough to make almost any part that can be useful in everyday life.
Machine manufacturing and assembly
Further, for the manufacture of a machine for manual bending of metal, it is necessary to make holes on the channel, which is clamping. The number of holes should be from 2 to 4, and their diameter should be equal to 9 mm. The hole closest to the end of the workpiece blank should be 3 cm from the edge. Another important point is that the clamping device should be shorter than the base by about 5-10 cm. In order to make a punch for crimping, you must have at your disposal a corner whose profile thickness will be greater than that of future workpieces. The lever handle is best made from materials such as rebar or timber. If a beam is used, then its cross-section should be no less than 15 mm, and if a beam is taken, then its dimensions should be no less than 50x50. The shape of the lever is recommended to be made U-shaped. This element is attached to the corner using welding or bolts.
Final work
After all the previous manipulations have been completed, you can begin to manufacture such an element as cheeks. They are made of rolled steel, and the thickness of the parts should be about 5 mm. It is important that these elements have chamfers, the thickness of which should be equal to 0.6 cm. The length of this section should be from 3 to 3.3 cm. It is important that the ends of the punch are also provided with chamfers with parameters such as 0.5 cm depth and 3 cm in length. They must be removed from the punch to ensure the installation of the axis. The production of such an element as an axis is carried out from metal rods whose diameter is 1 cm. The axis is fixed by welding. When installing, it is necessary to ensure parallelism of the axis line with respect to the edges of the angle. All this finished construction, together with the punch, is connected using a vise. When combining, it is important to ensure that the free shelf of the corners is located in the same horizontal plane in which the free channel shelf is located.

After that, the assembly work can be considered completed. In order to check the operability of the machine, it is recommended to take a mild steel blank with a thickness of up to 1.5 mm. It is worth noting that the price of a machine for bending purchased metal can reach up to $ 2000.
Sheet bending process
The design of a homemade machine can also consist of such parts as a bed, a flywheel nut, a sheet for bending, a clamp, a clamp, a punch for crimping. In order to work on this type of machine, certain knowledge and skills are needed. The advantage of using this unit is that it will allow you to keep the metal in integrity, in contrast to the same welding.
In the process of bending the metal, the following occurs: the outer layers of the metal workpiece are stretched, but the inner ones, on the contrary, are compressed. It is important that for bending a metal workpiece, it is necessary to apply such a force that will be greater than the ultimate elasticity of the material. With the help of metal bending machines, just this condition can be achieved. The advantages of the finished product, that is, bent sheets, include the following factors:
- the presence of high strength of the final product;
- the possibility of obtaining an integral structure without welds, bolts, etc .;
- eliminates the possibility of corrosion, as there is no damage to the metal during bending;
- the ability to get the right angle, without creating a weld.
Conclusion
The presence of such equipment at home greatly simplifies the work with metal blanks. However, when operating this device, it is extremely important to know and adhere to safety precautions. The price of a do-it-yourself sheet metal bending machine will also be significantly lower than the purchase price. You will have to spend only on those materials that are not at hand and you have to buy them.