Different materials are used to cover the grounds and garden paths. If earlier the stone formed the basis of this segment, nowadays even rubber panels with wood can be used for such flooring. But it is, rather, design variations on the theme of street paving, and in practical terms vibropressed pavers have almost no competitors. The material has long been established in its niche and, which is noteworthy, generally retains the classic manufacturing technique. Actually, a simple production technique makes it possible to produce paving stones even in artisanal conditions. But in any case, to obtain a high-quality result, it is necessary to observe technological subtleties using suitable equipment.
Paving stones in the paving family
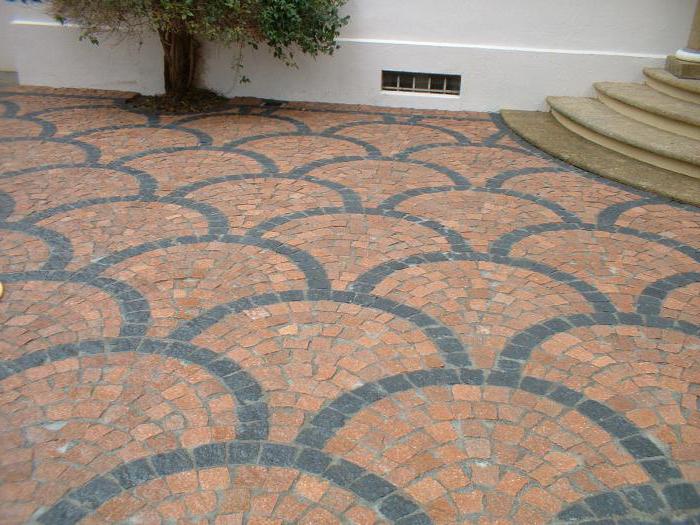
Paving stones are usually called the material from which the area or track is laid out. However, in the classical sense, this term still refers to the coating itself. Also, stone of certain sizes, from which paving is made, can be attributed to paving stones. Against the background of improving technologies for the construction of roads and pedestrian pavements, the requirements for flooring elements have also changed. Thus, paving stones entered the general group of paving slabs. In any case, the production techniques of these materials overlap in many ways. The differences are in the compositions. Thus, the manufacture of pavers usually involves the use of dense stone, clay or limestone. In the simplest versions, concrete can also be used. Under the condition of high-quality manufacturing, it is possible to obtain wear-resistant and durable elements for coatings with different characteristics. There are also modern variations in which emphasis is placed on the decorative effect.
Vibrocompression technology
There are several methods for the manufacture of pavers, but the most common is vibrocompression. To implement this technology, special forms for paving stones are used, which form a matrix located on the platform. The main task of the equipment is to ensure high-quality compaction of the mixture structure through vibrations. A punch is also used with the mold. This is a kind of piston, which also contributes to the compaction of the solution through oscillatory movements. Thus, the function of pressing the mass is fulfilled, from which elements for coating are subsequently made.
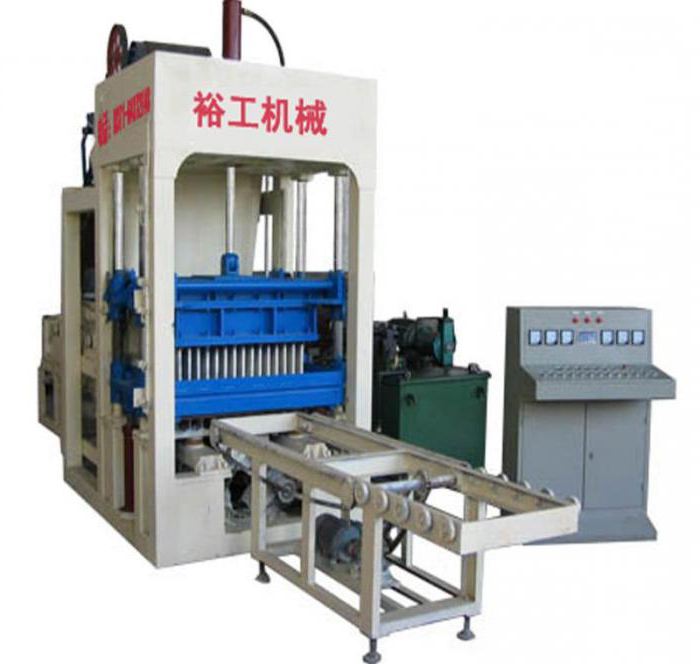
Externally, the design of such equipment is a cellular matrix, which is quite possible to make with your own hands. However, the industrial production of paving stones involves the connection of fairly powerful engines, which provide the effect of vibrocompression. The characteristics of the future tile depend to a large extent on the quality of the power impact. True, the composition also plays an important role.
Hyperpressing Method
As in the case of vibropressing, this technology aims to ensure the maximum possible compaction of the mixture, from which in the future should be a dense and strong paving. Only approaches to achieve this result differ. Hyperpressing also involves in the process of implementing the form for pavers, but in the very effect on the mixture does not provide for a vibration effect. The main stimulation occurs under the influence of high pressure, which is the press. Depending on the required properties of the material, the load on the mixture can vary in the range from 150 to 250 kg per 1 cm 2 . The choice of parameters of the force action also depends on the components of the composition. It is worth noting that pressure acts on the solution in the matrix both during the setting process and during the polymerization, that is, hardening. It is this technological nuance that gives the paving stones increased compressive strength.
Hyperpressing Equipment
As noted above, the use of technology requires a special press, which will exert pressure followed by compaction. The most common hydraulic units with single and double acting. In the first case, the machines are equipped with one cylinder, which provides an action on the matrix. The work of double-sided units provides for the impact on the form itself and on the punch. That is, in this case, a more productive production of paving stones is realized, although the quality may suffer from double exposure. True, double-sided machines provide not only a quantitative increase in production indicators, but also increase individual quality characteristics. In particular, the use of such a press minimizes the gradient of compaction. Also, the design features of this technique eliminate the need for pallets.
Stone blocks production by vibrocasting
This is one of the most technologically sophisticated methods for the production of pavers. This is explained by the requirements for the initial mass, and the need to use several principles of processing the solution. In contrast to previous methods, in this case, heating of the material is also provided in order to accelerate the polymerization. But the basic principle remains traditional. Like the solution from which vibropressed pavers are made, the mixture for this technology is initially laid in a special form. But instead of the usual matrix, a vibrating table with a vibrating surface is used. Due to the vibration effect, the compaction effect is again achieved, after which the material is transferred to the room where the evaporation heaters work. In such conditions, blanks for future pavers dry and gain optimal strength. As a rule, the final acquisition of performance occurs in a month.
Equipment for vibrocasting
A central place in the production complex is occupied by a molding vibrating table, which, through a special drive, excites vibrations of the mixture. As a result, the solution compaction function is performed. As a rule, a vibratory paving machine is supplied without a transformer; therefore, equipment should be provided with appropriate electrical equipment in a separate order. Depending on the requirements for the production process , transformers with a power of 2.5-5 kW are used. To simplify production, sometimes electric vibrators are also used, with which it is possible to supplement installations for compaction of solutions. A feature of this combination is the possibility of sifting loose mixtures through a vibrating unit and, at the same time, providing a compression seal.
Features of the manufacture of clinker pavers
Like a regular clinker, paving stones of this type are more likely to resemble bricks, but with enhanced strength properties. This is achieved largely through the use of special grades of clay. The production of clinker pavers itself is oriented not on compaction processes by means of vibrating and pressing machines, but on firing technology. The manufacturing process begins with the grinding of the primary composition, after which the mixture is extruded into molds through a special extruder.
This is followed by the first exposure to thermal radiation. Forms are placed in special chambers, where the mass is heated from different sides. At the final stage, the production of paving stones in the form of clinker involves firing in furnaces at temperatures up to 1200 ° C.
Features of the manufacture of granite pavers
The technological process of forming pavers from granite is also fundamentally different from the above methods. In this case, the machining of whole stone is realized by means of sawing machines. That is, manufacturers do not use any mixtures and modifying additives, which allows counting on the ecological purity of the coating. As a rule, the production of granite pavers involves smooth processing of the stone along the edges in order to form square or rectangular smooth elements. But for various reasons, the use of fragments with uneven edges can be justified - this is the so-called chipped paving stones.
Conclusion
Qualitatively laid paving stones are capable of performing their functions for decades, without collapsing and without deforming under mechanical stress. But, unfortunately, not every material of this type is associated with durability. Depending on the technology used for the production of paving stones, one can form an opinion on the possible operational qualities of the product. If you need inexpensive and versatile material, then it is worth giving preference to cement-lime tiles, which is best suited for the design of sites and paths in a private house. Clinker pavers are suitable for the same purposes, but at the same time they provide a decorative effect. If paving strength comes to the fore, then it is more advisable to bet on granite paving stones.