Modern industry cannot be imagined without a material like steel. We encounter it at almost every step. By introducing various chemical elements into its composition, mechanical and operational properties can be significantly improved.
What is steel?
Steel is an alloy that incorporates carbon and iron. Also, such an alloy (photo below) may have impurities of other chemical elements.
Several structural states are distinguished. If the carbon content is in the range of 0.025-0.8%, then these steels are called hypereutectoid and have perlite and ferrite in their structure. If the steel is hypereutectoid, then the pearlite and cementite phases can be observed. A feature of the ferritic structure is its high ductility. Cementite has a considerable hardness. Perlite form both of the previous phases. It can have a granular shape (cementite inclusions, which have a circular shape, are located on the ferrite grains) and lamellar (both phases have the form of plates). If steel is heated above the temperature at which polymorphic modifications occur, the structure changes to austenitic. This phase has increased ductility. If the carbon content exceeds 2.14%, then such materials and alloys are called cast irons.
Types of steel
Depending on the composition, the steel can be carbon and alloy. A carbon content of less than 0.25% characterizes low carbon steel. If its amount reaches 0.55%, then we can talk about medium-carbon alloy. Steel, which in its composition has more than 0.6% carbon, is called high carbon. If, while the alloy is made, the technology involves the introduction of specific chemical elements, then this steel is called alloyed. The introduction of various components significantly changes its properties. If their number does not exceed 4%, then the alloy is low alloy. Medium alloyed and high alloyed steel has up to 11% and more than 12% inclusions, respectively. Depending on the area in which steel alloys are used, their types are distinguished: tool, structural and special steels and alloys.
Manufacturing technology
The smelting process has become quite laborious. It includes several stages. First of all, you need raw materials - iron ore. The first step involves heating to a certain temperature. In this case, oxidative processes occur. In the second stage, the temperature becomes much higher. The processes of carbon oxidation are more intense. An additional enrichment of the alloy with oxygen is possible. Unnecessary impurities are removed to the slag. The next step is to remove oxygen from steel, since it significantly reduces the mechanical properties. This can be carried out by diffusion or precipitation method. If the deoxidation process does not occur, then the resulting steel is called boiling. Calm alloy does not emit gases, oxygen is completely removed. An intermediate position is occupied by semi-quiet steels. Iron alloys are produced in open-hearth furnaces, induction furnaces, and oxygen converters.
Steel alloying
In order to obtain certain properties of steel, special alloying substances are introduced into its composition. The main advantages of such an alloy are increased resistance to various deformations, the reliability of parts and other structural elements increases significantly. When hardening, the percentage of cracks and other defects decreases. Often this method of saturation with different elements is used to give resistance to chemical corrosion. But there are a number of disadvantages. They require additional processing, the likelihood of flocs is high. In addition, the cost of the material increases. The most common alloying elements are chromium, nickel, tungsten, molybdenum , cobalt. The scope of their application is quite large. This includes engineering, and the manufacture of parts for pipelines, power plants, aviation and much more.
The concept of heat resistance and heat resistance
The concept of heat resistance refers to the ability of a metal or alloy to retain all its characteristics when working at high temperatures. In such an environment, gas corrosion is often observed . Therefore, the material must also be resistant to its action, that is, be heat-resistant. Thus, the characteristics of alloys that are used at significant temperatures should include both of these concepts. Only then will such steels provide the necessary work resource for parts, tools and other structural elements.
Features of heat resistant steel
In cases where the temperature reaches high values, the use of alloys is required, which will not collapse and give in to deformation. In this case, heat-resistant alloys are used. The operating temperature for such materials is above 500º. Important points characterizing such steels are a high endurance limit, ductility, which lasts for a long time, as well as relaxation stability. There are a number of elements that can significantly increase resistance to high temperatures: cobalt, tungsten, molybdenum. A mandatory component is chrome. It does not so much affect strength as it increases scale resistance. Also, chrome inhibits corrosion processes. Another important characteristic of alloys of this type is slow creep.
Classification of heat resistant steels behind structure
Heat-resistant and heat-resistant alloys are of the ferritic class, martensitic, austenitic and with feritic-martensitic structure. The first are composed of about 30% chromium. After special treatment, the structure becomes fine-grained. If the heating temperature exceeds 850 ° C, then the grains increase, and such heat-resistant materials become brittle. The martensitic class is characterized by such a chromium content: from 4% to 12%. Also, nickel, tungsten, and other elements may be present in minor amounts. They make parts of turbines, valves in cars. Steels that have martensite and ferrite in their structure are suitable for operation at constant high temperatures and long-term operation. The chromium content reaches 14%. Austenite is obtained by introducing heat-resistant nickel alloys. Steels with a similar structure have many grades.
Nickel Based Alloys
Nickel has a number of useful properties. It has a positive effect on the workability of steel (both hot and cold). If the part or tool is designed to work in an aggressive environment, then alloying with this element significantly increases resistance to corrosion. Heat-resistant materials based on nickel are divided into the following groups: heat-resistant and heat-resistant. The latter should also have minimal heat-resistant characteristics. Operating temperatures reach 1200º. Additionally, chromium or titanium is introduced. It is characteristic that nickel alloyed steels have a small amount of such impurities as barium, magnesium, boron, and therefore grain boundaries are more strengthened. Heat-resistant alloys of this type are produced in the form of forgings, rolled products. Casting of parts is also possible. The main area of their application is the manufacture of gas turbine elements. Heat resistant nickel-based alloys contain up to 30% chromium. They are quite well amenable to stamping, welding. In addition, the scale resistance is at a high level. This makes it possible to use them in gas pipeline systems.
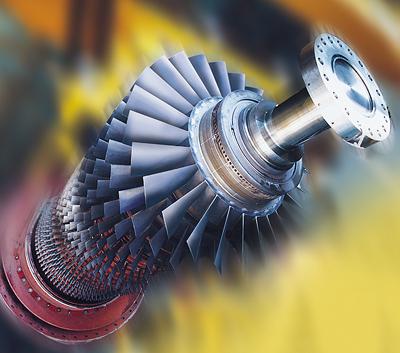
Titanium alloy heat resistant steel
Titanium is introduced in a small amount (up to 0.3%). In this case, it increases the strength of the alloy. If its content is much higher, then some mechanical properties deteriorate (hardness, strength). But plasticity is increasing. This facilitates the processing of steel. With the introduction of titanium along with other components, it is possible to significantly increase the heat-resistant characteristics. If there is a need to work in an aggressive environment (especially in the case when the design involves welding), then alloying with this chemical element is justified.
Cobalt alloys
A large amount of cobalt (up to 80%) is used for the production of materials such as heat-resistant and heat-resistant alloys, since it is rarely used in its pure form. Its introduction increases ductility, as well as resistance when working with high temperatures. And the higher it is, the higher the amount of cobalt introduced into the alloy. In some brands, its content reaches 30%. Another characteristic feature of such steels is the improvement of magnetic properties. However, due to the high cost of cobalt, its use is quite limited.
The effect of molybdenum on heat-resistant alloys
This chemical element significantly affects the strength of the material at high temperatures.
Especially effective is its use together with other elements. It significantly increases the hardness of steel (already at a content of 0.3%). The tensile strength also increases. Another positive feature that heat-resistant alloys alloyed with molybdenum have is a high degree of resistance to oxidative processes. Molybdenum helps to chop grain. The disadvantage is the difficulty of welding.
Other special steels and alloys
To perform certain tasks, materials that have certain properties are required. Thus, we can talk about the use of special alloys, which can be both alloyed and carbon. In the latter, a set of required characteristics is achieved due to the fact that the manufacture of alloys and their processing takes place using a special technology. Still special alloys and steels are divided into structural and tool. Among the main tasks for this type of materials the following can be distinguished: resistance to corrosion and wear, the ability to work in an aggressive environment, increased mechanical characteristics. This category includes heat-resistant steels and alloys with a high working temperature, and cryogenic steels that can withstand up to -296º.
Tool steel
For the manufacture of tools in production, special tool steel is used. Due to the fact that their working conditions are different, the materials are also selected individually. Since the requirements for tools are quite high, the characteristics of the alloys for their production are appropriate: they must be free from impurities, inclusions, the deoxidation process is well conducted, and the structure is homogeneous. It is very important for measuring instruments to have stable parameters and to counteract wear. If we talk about cutting tools, they work in conditions of elevated temperatures (edge heating occurs), constant friction and deformation. Therefore, it is very important for them to maintain their primary hardness when heated. Another type of tool steel is high-speed. Basically, it is alloyed with tungsten. Hardness is maintained up to a temperature of about 600º. There are also stamped steels. They are designed for both hot and cold deformation.
Scope of special alloys
There are many branches in which alloys with special characteristics are used. In view of their improved qualities, they are indispensable in mechanical engineering, construction, and the oil industry. Heat-resistant and heat-resistant alloys are used in the manufacture of turbine parts, spare parts for cars. Steel, which has high anti-corrosion characteristics, is indispensable for the production of pipes, carburetor needles, discs, all kinds of elements of the chemical industry. Railroad rails, buckets, tracks for transport - wear-resistant steels are the basis for all this. In the mass production of bolts, nuts and other similar parts, automatic alloys are used. Springs should be sufficiently resilient and wear resistant. Therefore, the material for them is spring steel. To improve this quality, they are additionally alloyed with chromium and molybdenum. All special alloys and steels with a set of specific characteristics can reduce the cost of parts where previously used non-ferrous metals.