Physical properties, in particular, the hardness of any material, depend not only on its chemical composition, but also on the volumetric molecular structure. A vivid example is a diamond consisting of the same carbon atoms as a regular pencil lead. Iron can also become softer or harder, depending on how its crystal lattice is formed. This property of his has been known to people for a long time, and, as often happens, it was initially widespread in weapons technology.
Metal hardening has long been practiced in the manufacture of swords and sabers. The art of the gunsmith was to create a blade that would not break in battle, and would remain sharp for as long as possible. A knight’s sword, a saracen saber, a treasure trove of a Russian knight or katana samurai met these requirements, and the technology of their production was brought to a high art level.
The metal is quenched by heating it to a temperature called critical. Its value corresponds to a state of the material in which there is an increase in entropy, leading to crystalline changes. To fix this position, the item needs to be cooled quickly enough. Of course, such a description of the process is extremely simplified, in fact, the technology is usually much more complicated. However, it is in this way that the metal is quenched at home in those cases when the purchased tool, for example, an ax, dulls too quickly. It should be remembered that it is impossible to repeat this procedure many times, otherwise the metal will "get tired", its internal molecular bonds will weaken, and except for remelting, it will not work for anything.
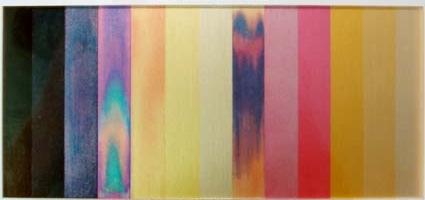
As in any other business, one cannot rely on the principle “the more the better”. To obtain the desired properties of the subject, it should be heated to the desired temperature. Unfortunately, a thermometer cannot be used. The method used for thermal control is also very ancient. The temperature is determined by the color of the glow, and when it is reached, the quenching of the metal proceeds to the next phase - cooling, for which water or oil is used.
Comprehension by scientists of the effect of induction has opened a new page in metalworking technologies. It turned out that the depth of the heated layer depends on the frequency of the current.
In the diagram, arrows show the heating zones of the part and the passage of the pick-up lines.
Surface hardening of metal has become possible. The detail is brought to white heat not by immersion in a fire, as it was in the Middle Ages, but by resistive heating by currents induced by a coil that does not have direct contact with it. This technology provides unique, at first glance, contradictory properties: on the outside, the product can be solid, and inside plastic. Surface induction hardening is used in cases where strength is required and fragility is unacceptable.
In 1936, our compatriot, Professor V.P., became the author of the theoretical basis and methodology for the practical application of this technology. Vologdin. In addition to physical advantages, this development is also economically advantageous, since almost all the energy emitted by the inductor is used to heat the workpiece.