This article will discuss what constitutes work in progress. This concept refers to enterprises producing any product. Let's start with the definition. So, work in progress is a product that has not passed all the stages stipulated by the
production process. This also includes products that are completely ready, but have not passed the appropriate tests, or lacking a complete set.
What is classified as work in progress?
Firstly, these are materials that arrived at the production units, but were not processed, as well as purchased semi-finished products, various components, with which assembly operations were not performed. Secondly, these are parts, components, various products that are related to marriage. Consider from the point of view of accounting such a category as work in progress. Account 20 - debit balance. It has the name "main production". It is important for specialists to have an accurate idea of โโthe amount of work in progress, because these data serve as the basis for assessing such an important economic indicator as cost. The entire process must be documented. It requires accurate detailing of the costs that arise at each stage. Such documents include all kinds of technological schemes, maps, detailed descriptions of processes carried out, and others. It is they that serve as the basis for the formation of estimates and estimates. Sometimes a problem arises in sharing costs related to finished products and work in progress.
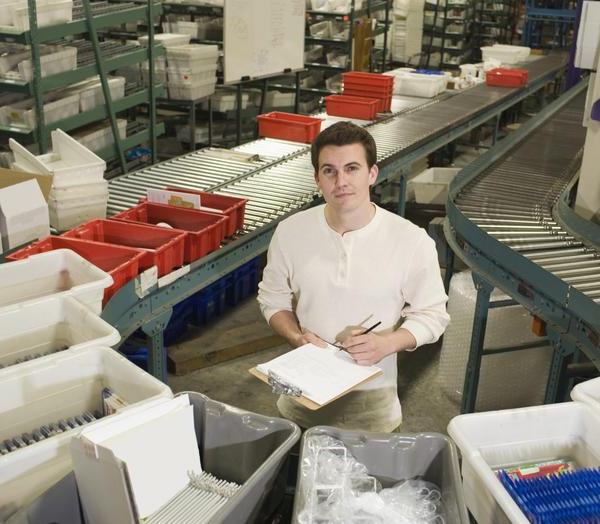
Then resort to methods of assessment of the actual, regulatory or planned size of
production costs. The calculation of this indicator for
direct costs or the direct cost of the used raw materials, semi-finished products and other materials is actively used.
Estimation of balances
Their number, as a rule, is determined in accordance with the data of the inventory. It is in the process of this operation that the state of unfinished products is established, two important indicators are calculated. This is the cost and quantity (volume) of materials consumed, as well as time costs (based on data presented in technological maps). Those balances that are formed at the end of the reporting period in mass and serial production can be estimated by the cost of the consumed materials, raw materials and other elements, as well as by direct costs or in the balance sheet at cost (both planned and regulatory).
If we talk about the unit, then the work in progress is reflected in the actual production costs. Information about them can be found in the balance sheet. It is fair to say that this is the accounting method that allows the company management to obtain the most reliable data. The important thing is that, in accordance with accounting rules,
finished products and work in progress must be valued using the same method.