Bearings are technical devices that support rotary axles and shafts. They are able to receive radial and axial loads that directly affect the axis or shaft, and then transfer them to the frame, housing or other parts of the structure. The bearing of the bearing at the same time is to hold the shaft in space, giving it the ability to swing freely, rotate or move linearly with minimal energy loss. The performance, efficiency and, of course, the durability of the machine depend on the quality of this device.
Types of bearings
Based on the principle of operation, all devices are divided into gas-dynamic, hydrostatic, gas-static, hydrodynamic, magnetic, sliding and rolling. The last two types are usually used in mechanical engineering. The rolling bearing consists of a cage and two rings that separate them. A groove runs along the outer part of the inner ring and the inner part of the outer - this is the path along which rolling bodies (rollers or balls) ride when the device is involved in operation.
According to the perception of the load, radial (for radial and small axial load), thrust (for axial load), axial-radial (for axial and low radial load) and angular contact bearings (for combining axial and radial load) are divided.
By the number of rows for balls or rollers, single-row, double-row and multi-row devices are distinguished. Depending on the ability to compensate for the existing distortions of the shafts, non-self-aligning bearings, which allow mutual misalignment of the rings up to eight degrees, and self-aligning (misalignment up to four degrees) are divided.
Symbol
The Russian marking of such devices consists of a symbol standardized in accordance with GOST 3189-89, as well as a manufacturerβs code. Thus, the marking includes seven digits of the main designation (if the values ββof the signs are zero, it can be reduced to two characters) and an additional one located to the right / left of the main one. In the case of an arrangement on the left, it is always separated by a β-β sign (dash), and if on the right, it begins with some letter. Reading is always carried out from right to left, whether it is radial or thrust bearings.
GOST prescribes to place marking elements in a certain sequence. So, first a series of widths (one digit) is indicated, then a constructive variety (two digits), then a bearing type (one digit), a series of diameters (one digit) and a symbol for the inner diameter (two digits).
Where is the thrust bearing used?
There are very few machines without rotating parts. Parts such as drums, levers, wheels, axles, shafts, etc., as a rule, are always available - everyone who deals with cars knows this. This means that it cannot do without bearings. Any vehicle needs good care and periodic repair, and these devices have to be changed from time to time. But a thrust bearing is not only an indispensable attribute of a car, it is used in metallurgical, energy equipment, and mining machinery. Such designs can enhance the speed qualities of a particular part, so they are often used in centrifuges, car wheels, worm gearboxes, spindles and more.
Ball and roller thrust devices
Ball thrust bearing is designed to absorb axial loads, it is non-self-aligning. They produce single-row devices that perceive an axial one-sided load, and two-row devices perceive a two-sided one. Such structural units are used in vertical shafts, jacks, rotating centers of metal cutting machines.
The thrust roller bearing is used when a very large axial load is applied. These devices can be of three types:
- with tapered rollers - designed to operate at extremely high loads, increased rotation speeds, impacts;
- with cylindrical rollers - are used to work at low speeds, but at significant loads;
- with spherical conic rollers - have self-aligning properties, can bear significant axial and radial loads.
Roller thrust bearing is used in thrust blocks of piercing mills, extruders, heavily loaded vertical shafts, alternators. In addition, it is part of the rotary nodes of metallurgical equipment.
Angular contact bearings
These devices are also used in various fields of industry: machine and tank building, chemical industry and others. These structural units are capable of perceiving both types of load at once: both axial and radial. Its maximum value directly depends on the angle at which the rolling bodies come into contact with the raceways. It is possible to use an angular contact bearing having a four-point contact. However, it should be noted that in the general technical sectors, single-row and double-row devices are most widely used.
Varieties of angular contact bearings
Design units can be performed in different ways. The angular contact ball bearing may be open or have a protective metal washer or contact seal. Four-point contact devices have detachable outer or inner rings and are more suitable for axial loads. Angular contact ball bearings are often equipped with a glass-filled polyamide cage . But there are also structural units with a brass point or stamped steel separator. Such bearings absorb radial and axial unilateral loads. There is a bevel on the inner or outer ring on the side of the rolling bodies, therefore, often the number of rollers in this embodiment of the device exceeds the number of balls in the corresponding angular contact structural unit. This bearing is capable of absorbing a greater load than a radial bearing of a similar size.
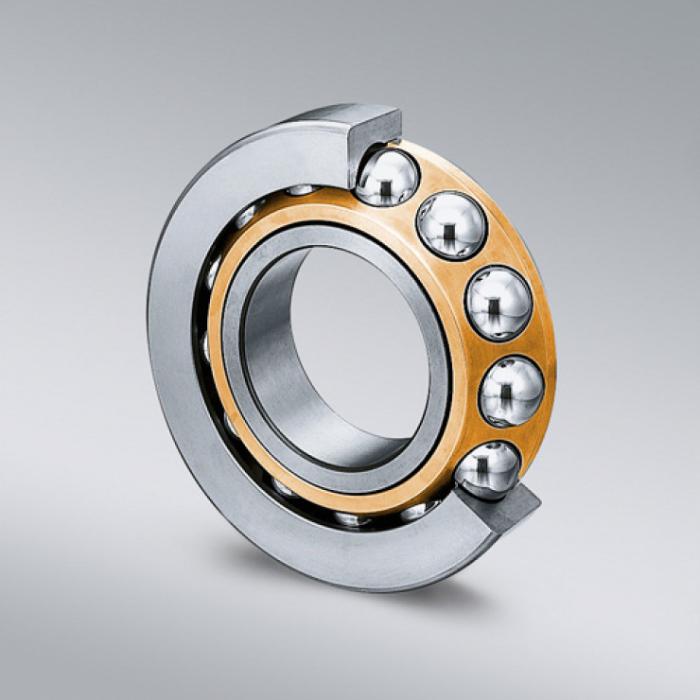
An angular contact roller bearing typically has a conical type rolling body. Due to the location of the rollers to the axis of rotation at a certain angle, this type of device is able to absorb combined loads. At the same time, the angular contact tapered bearing has a much lower permissible rotational speed than the structural unit with cylindrical rollers. The level of axial load acceptance is determined by the angle of taper: when it increases, the radial load decreases, and as a result, the effective axial load increases. If you want to use such bearings, you need to make sure that there is no misalignment of the bearing sockets and the shaft axis in which they are installed.
Variants of roller angular contact conical devices:
- 7000 - main;
- 27000 - with a high angle of taper;
- 97000 - two-row;
- 77000 - four-row.
Types 27000 and 7000
Designed for the perception of radial and axial unilateral loads. Such structural units need to adjust the axial clearances and the installation of the outer rings - both during installation and during operation.
Type 97000
These devices are capable of perceiving one-sided and two-sided radial and axial loads simultaneously. If you need to change the radial or axial clearance, the distance ring mounted in the middle of the inner rings is ground in the bearing. The maximum load in structural units of this type is 1.7 times higher than that which is permissible for single row bearings.
Type 77000
Devices of this type are designed to absorb significant radial and minor bilateral axial loads. Such a structural unit can withstand a much greater effect of radial forces than the corresponding single-row.
Bearing selection
When choosing the type and size of the device, the following factors should be considered:
- nature of the load (variable, shock, vibration, constant);
- required resource (in millions of revolutions or hours);
- direction and value of the load (axial, radial, combined);
- environmental conditions (dustiness, temperature, acidity, humidity);
- rotational speed of the ring of the structural unit;
- special requirements that depend on the design of the bearing (required dimensions, self-alignment properties, noise reduction, etc.).
Dimensions and accuracy classes
Such devices have dimensional series. In terms of overall dimensions they are divided into heavy / medium / light / extra light / ultra-light, and in width - into especially wide / wide / normal / narrow. The most common are medium, light and especially light varieties.
The accuracy classes of structural units are distinguished: super-precision / precision / high / elevated / normal. Bearings are also produced in which the accuracy class is below normal (the most inaccurate) or higher than super-precision (the most accurate). Depending on this parameter and other additional requirements, such as vibration level and so on, all devices are divided into categories: classes A, B, C.
In conclusion, we give a breakdown of the conventions of the types of bearings:
- 0 - radial / ball;
- 1 - radial / ball spherical;
- 2 - radial / roller with cylindrical short rollers;
- 3 - radial / roller with spherical rollers (barrel-shaped);
- 4 - radial / roller with needle or cylindrical long rollers;
- 5 - radial / roller with twisted rollers;
- 6 - angular contact / ball;
- 7 - conical / roller;
- 8 - persistent radial / ball, persistent / ball;
- 9 - persistent radial / roller, persistent / roller.