Centrifugal casting is a method of manufacturing blanks-castings, which is based on the effect of centrifugal forces on the molten mass of material. The foundry, engaged in the manufacture of shaped billets and rough castings, has a wide variety of casting methods: in chill molds, in sand and clay molds, according to special lost wax patterns, under the influence of pressure, etc. But centrifugal casting is optimal for the quality of the casting.
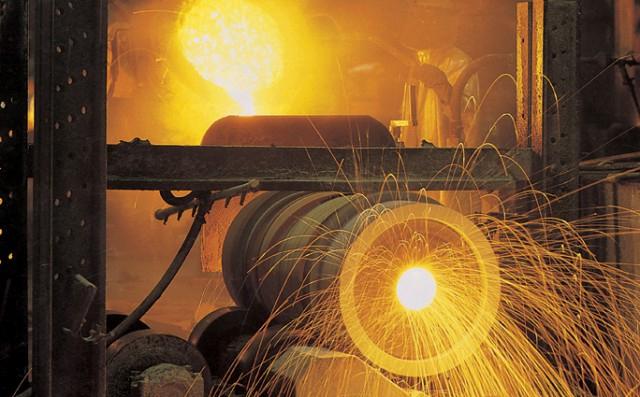
In fact, the method consists in the fact that, under the action of centrifugal force, the molten material spreads uniformly on the inner surface of the mold and, crystallizing, forms a preform with the necessary parameters. You should not think that this method is applicable only to metals and their alloys. In fact, the molding of plastic products has become extremely widespread. But polymeric materials have a number of features that must be considered when working with them. Injection molding is often carried out under pressure, which ensures high precision products.
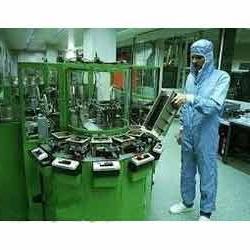
In most cases, different types of castings are used to obtain metal castings. At the same time, centrifugal casting has several advantages: the absence of hollow shells and slag inclusions in the obtained casting, high density of the material, increased wear resistance of the metal, which is achieved due to the uniform structure, etc. The main advantages of this method are the saving of material on the workpiece and a significant reduction in the complexity of the whole technological process. process (due to the maximum approximation of the casting to the finished product).
Centrifugal casting has a number of "minuses". These include: inaccurate obtaining of free surfaces of the workpiece, a tendency to segregate material, the high cost of forms (due to increased requirements for dimensional accuracy).
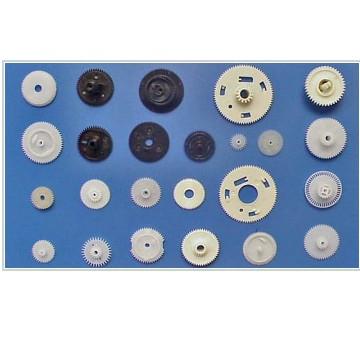
The centrifugal casting method uses special machines. They differ in the direction of the axis of rotation - vertical, horizontal and with an inclined axis (although the latter are rarely used). Machines with a vertical axis are used to produce small lengths of workpieces with insignificant step differences (rings, pistons, bushings, etc.). Machines with a horizontal axis of rotation allow to obtain high-precision long-length castings with a wall of the same thickness. A similar method produces cast iron pipes. This method is the most common. Using centrifugal casting, it is possible to produce pipes with walls from 80 to 300 mm (depending on the equipment used). The only thing worth remembering is that with this method, internal stress arises in the workpieces. Therefore, after receiving the castings, annealing is necessary.
Other blanks for parts that are bodies of revolution are also obtained by centrifugal casting. The high-precision casting method is especially popular in the manufacture of non-ferrous metal blanks (this method saves expensive materials).