The strength of the weld is determined by several factors. The first important indicator is the mode of welding two metal structures together. The second factor is the right consumable. The third parameter that determines the strength of the metal structure is the exact dimensions of the legs of the weld.
What is a leg
This name comes from the fact that if we consider the welding seam in the section, then with its perfect design it will look like an isosceles triangle. In this case, the leg will be the distance between the end of the seam of one part and the plane of the other part. At its core, the leg of the weld will be the leg of such an isosceles triangle, hence the name.
So, what is a leg, now itโs clear. It is important to understand that the strength of the joint will greatly depend on the value of the corner joint. However, it is important not to be mistaken. The fact that the weld leg is responsible for its strength does not mean at all that the thicker it is, the stronger the joint itself. In this case, it must be understood that too many deposited elements will lead to a deterioration in the characteristics of the connection. In addition, too much consumption of electrodes, gas, flux and additives will greatly increase the cost of such work.
Junction geometry
For the reasons that have been described above, it is very important to consider the geometry of the joint. The main parameter when connecting two metal structures will be that the leg of the weld should have large longitudinal section parameters.
For example, when welding two metal elements having different thicknesses, the dimensions of the weld leg should be determined by the part that has a smaller thickness. Most often, the dimensions of the weld leg are determined and measured according to pre-prepared templates. Today, welders use the most versatile tool for measuring the leg. Such devices are called "welder catheters."
This tool has the form of two thin plates, the ends of which have the shape of a notch, designed to determine different parameters of the leg. The specialist takes turns applying different sized catheters to the suture. Among them, there will certainly be one that will accurately repeat the geometry of the leg of the weld.
Seam shape
After welding, most often only two types of seam are formed.
The first type is an ordinary welding seam that looks like a roller with a convex surface. However, it is important to note here that this type of seam, according to experts, is not optimal. There are two reasons for this statement. Firstly, the stress on the structure will increase significantly inside such a seam, and secondly, the consumption of materials to create such a seam will increase significantly.
The second type of seam is considered ideal. It looks like a roller with a concave surface, however, to achieve such a performance when welding two structures is very, very difficult. In order to achieve this type of seam, it is important to properly configure the parameters of the welding machine, as well as maintain the same electrode flow rate. In order to fulfill both conditions, you need a specialist with a lot of experience in such work. It is worth adding that this type of weld is not used in the assembly of metal structures.
Dimensions of the corner joint
If we talk about the dimensions of the leg of the fillet weld, then, as mentioned above, the decisive factor will be the thickness of the parts being welded. For example, if there are parts with a thickness of 4-5 mm, then the size of the leg will be 4 mm. If the thickness increases, then the leg will have to grow.
A very important factor that affects the concavity or convexity of the weld bead is which electrode was used. This refers to the chemical composition of the consumable element. Suppose, if you use an electrode that, when used, becomes thick and viscous, you will end up with a convex roller surface. If the metal is liquid and spreading during the melting of the roller, then its surface will be concave.
Speed โโand mode of welding
In order to obtain the optimal leg of the weld during work, as well as ensure a strong connection, several points must be taken into account.
- The main parameters of the selected operating mode will be the current strength, as well as voltage. Specialists in this field know that if you increase the current strength and also create a stable voltage, then the weld will be deeper and will have a smaller thickness. If, in the process of operation, a stable current is maintained, but the voltage is changed, then the resulting compound will be less deep, but its thickness will increase. It follows the logical conclusion that the thickness of the leg of the weld will also change.
- The second factor is speed. If this parameter is not exceeded by more than 50 m / h, then the depth of joint welding will increase, and the thickness will decrease.
- If we do the opposite, that is, increase the speed, then not only the depth of welding will decrease, but also the thickness of the weld leg. Also, the characteristics of the metal formed inside the gap between the workpieces will be reduced. This is due to the fact that with rapid movement the heating of the bath is negligible.
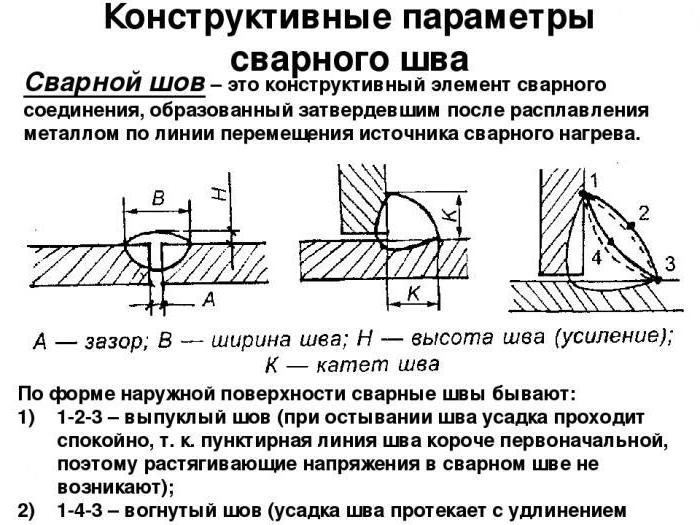
How to identify a weld leg
It is worth saying that it is not very difficult to do this. The basis of this statement is that in the section the given seam is an isosceles triangle, and the calculation of the leg of such a figure is a rather simple operation. In order to carry out the calculations, one can use the usual trigonometric formula: T = S cos 45ยบ.
T is the size of the leg of the weld, and S is the width of the resulting roller, or the hypotenuse of the triangle.
In order to determine the leg of a seam, it is important to know the thickness of the seam itself. This operation is quite simple, plus in this case, cos 45ยบ will be equal to 0.7. After that, you can substitute all available values โโin the formula and get the value of the leg with high accuracy. Calculation of the weld leg using this formula is one of the simplest operations.
Types of seams
To date, there are two main types of weld. It is important to understand that the seam and the weld are two different things.
- Welded butt seams. This type is used when connecting parts end to end, that is, the ends. Most often in practice, this type of weld is used in the assembly of pipelines, as well as in the manufacture of sheet metal structures. The use of this type of seam is considered the most economical, as well as the least expensive in terms of energy.
- There are also fillet seams. In fact, it is worth highlighting three types - angular, tee, lap. The cutting of the edges of materials in this case can be either one-sided or two-sided. It depends on the thickness of the metal. The cutting angle is in the range from 20 to 60 degrees. However, it is important to understand that the more the angle is selected, the more consumables will have to be spent, and the quality will also decrease.
Weld Configuration
Welds also differ in their configuration. Here, several types can be distinguished: longitudinal rectilinear and curvilinear, circular.
If welding of longitudinal seams will be carried out, it is very important to conduct thorough preparation of the metal surface, especially if the work will take place with a large length of the seam. When creating this type of seam, it is important that the surface is not wavy, and all burrs of the edges must be cleaned. Also an important detail will be the removal of moisture, rust, dirt or any other undesirable elements from the work surface before welding.
If ring welding will be carried out, then it is very important to adjust the operating mode of the welding machine. If the diameter of the product is small, it is important to reduce the current strength to achieve a high-quality weld.
It can be added that the resulting seams can be not only concave or convex, but also flat. Flat and concave types are best suited for those structures that are operated under dynamic loads. The reason for this was that this type of weld lacks a tangible transition from the joint itself to the metal.
GOST weld leg
GOST 5264-80 is a document that establishes the main types, structural elements, as well as the dimensions of all welded joints. However, it is important to note that this paper does not apply to the types of joints that are used to connect the pipeline.
One of the points of this GOST suggests that when welding butt-type welding and different thicknesses of parts, they can be connected in the same way as parts with the same thickness, if their difference does not exceed certain indicators.
This document also describes that it is permissible to offset the welded edges before welding in relation to each other. Also there are set the numerical parameters of the displacement, which are allowed at a certain thickness of the workpiece.
There is an appendix to this document, in which all the minimum dimensions of the legs of the weld are prescribed. It is worth adding that the bulge, as well as the concavity of the seam, can be no more than 30% of the value of its leg.