Pressure in gaseous and liquid media is one of the most important indicators, the measurement of which is required for the maintenance of communication and technological systems. Work objects include various filters, piping systems, air conditioning and ventilation devices. Using a differential pressure gauge, the user reveals not only the characteristics of the operating pressure, but also gets the opportunity to record the difference between the dynamic indicators. The knowledge of this data facilitates the control of the system and increases the reliability of operation. In addition, differential pressure gauges are also used to measure the flow of liquid, gas or compressed air.
Principle of operation
In most pressure gauges, the technology for determining and calculating data is based on deformation processes in special measuring units, for example, in a bellows. This element acts as an indicator perceiving pressure drops. The block also becomes a differential pressure transducer - the user receives information in the form of moving the pointer arrow on the device. In addition, data can be presented in Pascals, covering the entire measuring spectrum. This method of displaying information, for example, is provided by the Testo 510 differential pressure gauge, which during the measurement process eliminates the need for the user to hold it in his hand, as special magnets are provided on the back of the device.
In mechanical devices, the main indicator is the location of the arrow, controlled by a lever system. The pointer moves until the differences in the system cease to influence a certain force. A classic example of this system is shown by a differential pressure gauge DM 3538M series, which provides proportional conversion of delta (pressure difference) and provides the result to the operator in the form of a unified signal.
Classification
Due to the complexity of the pressure measurement processes , the characteristics of the working media and further conversion, there are several options for differential pressure gauges for working in different conditions. By the way, a differential pressure gauge, the operating principle of which is largely determined by its design, is oriented by its device to the possibility of application in specific environments - therefore, classification is also made from this. So, manufacturers produce the following models:
- The group of liquid differential pressure gauges, which includes float, bell, pipe and ring modifications. In them, the measuring process is based on the indicators of the liquid column.
- Digital differential pressure gauges. They are considered the most functional, because they make it possible to measure not only the characteristics of pressure drops, but also the flow rate of compressed air, humidity and temperature. A striking representative of this group is the Testo differential pressure gauge, which is also used in environmental monitoring systems , in aerodynamic and environmental studies.
- Category of mechanical devices. These are bellows and membrane versions that provide measurement by tracking the characteristics of a pressure-sensitive element.
Two-pipe models
These devices are used to measure pressure indicators and determine the differences between them. These are devices with a visible level, which is usually presented in a U-shape. By design, such a differential pressure gauge is an installation of two vertical interconnected tubes that are fixed on a wooden or metal base. A mandatory component of the device is a plate with a scale. In preparation for the measurement, the pipes are filled with a working medium.
Further, the flow of the measured pressure begins in one of the pipes. At the same time, the second pipe interacts with the atmosphere. During the delta measurement, both tubes experience a measured pressure. A liquid-filled two-pipe differential pressure gauge is used to measure rarefaction, non-aggressive gas and air pressure.
Single tube models
Single-tube differential pressure gauges are usually used if it is necessary to obtain a high-precision result. In such devices, a wide vessel is applied, on which pressure acts with the highest coefficient. The only tube is fixed to the plate with a scale showing the difference data and communicates with the atmosphere. In the process of measuring pressure drops, the smallest of the pressures interacts with it. The working medium is poured into the differential pressure gauge until the zero level is reached.
Under the influence of pressure, a certain fraction of the liquid flows into the tube from the vessel. Since the volume of the working medium that has moved into the measuring tube corresponds to the volume emerging from the vessel, a single-tube differential pressure meter provides for measuring the height of only one liquid column. In other words, the measurement error is reduced . Nevertheless, and devices of this type are not spared the disadvantages.
Deviations from the optimal values may be due to thermal expansion in the measuring components of the device, the density of the working medium and other errors, which, however, are typical for all varieties of differential pressure gauges. For example, a differential digital pressure gauge, even taking into account corrections for density and temperature coefficients, also has a certain error threshold.
Membrane Differential Pressure Gauges
The main subtype of mechanical differential pressure gauges, which is also divided into devices with metallic and non-metallic measuring elements. In devices with a flat metal membrane, the calculations are based on fixing the deflection characteristics in the measuring component. A differential pressure gauge is also common, in which the membrane acts as a dividing wall for the chambers. At the time of deformation, the opposing force is formed by a cylindrical coil spring, unloading the measuring element. So there is a comparison of two different pressure values.
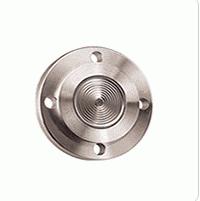
Also, some modifications of membrane devices are equipped with protection against one-sided exposure - this design feature allows them to be used in measuring overpressure. Despite the active introduction of electronics in the metrology industry as a whole, membrane measuring instruments remain popular and even indispensable in some areas. For example, the DMTs-01m high-tech differential pressure gauge of a digital type, despite its ergonomics and high accuracy, has a number of limitations on its use in conditions where the operation of membrane devices is possible.
Bellows versions
In such models, the measuring element is a corrugated box made of metal, supplemented by a spiral spring. The plane of the device is divided into two parts by a bellows. The greatest impact of pressure falls on the chamber outside the bellows, and the smallest - in the internal cavity. As a result of the action of pressures with different forces, the sensitive element is deformed in accordance with a value proportional to the desired index. These are classic differential pressure gauges showing the measurement results with an arrow on the dial. But there are other representatives of this family.
Other mechanical versions
Ring, float and bell devices for measuring the differential pressure are less common. Although among them there are relatively accurate scaleless and self-recording models, as well as devices with contact electrical devices. Data transmission in them is provided remotely again, by means of electric communication or due to pneumatics. To determine the expenditure indicators on the basis of variable differences, mechanical devices with summing and integrating additions are also produced.
Digital differential pressure gauges
Devices of this type, in addition to the main functions of measuring the difference in pressure, are able to determine the dynamic performance of working environments. Such devices are designated by marking DMTs-01m. The differential digital pressure gauge, in particular, is used in the ventilation control systems of production facilities, it allows calculating gas consumption indicators, taking into account temperature adjustments, and also taking into account average costs for the measured positions. The device is equipped with a microprocessor, which automatically records the measurements and accumulation of information on the gas duct. All received information about the results of work are displayed on the display.
Selection recommendations
Settlement operations with pressure indicators require the use of a reliable device that best meets the operating conditions. In this regard, it is important to determine the list of functions that the device will perform. For example, the Testo 510 differential pressure gauge is able to provide accurate readings with temperature compensation and provide data on a digital display. In some cases, a signaling model is required, so this option should be considered.
For the most correct data, you must first compare the characteristics of the device with the possibility of operation in a specific working environment. Not all devices can be used in oxygen, ammonia and freon environments. At least their accuracy may be low.