Shaft type grain dryers are currently in high demand. They provide uniform and stable blowing of grain. Let us consider in more detail the design of a shaft grain dryer .
general information
The task of any equipment for drying grain is to properly blow grain and oilseeds to reduce moisture. This allows you to store the product for a long time.
With the right choice of the operating mode of the equipment, it is possible to create conditions for the ripening of grain and thereby improve its quality characteristics.
One of the main advantages of modern equipment for drying grain is the almost complete exclusion of the probability of spontaneous combustion of the product.
Mechanism of action
The principle of operation of a shaft grain dryer is as follows. Grain material (pre-cleaned) is fed into the mine. Air flows heated by the heat block pass through the product layer. They come evenly from the supply ducts, which alternate with the exhaust ducts. Boxes are staggered. They are open from below and have a tent-like shape.
Vertical boxes are installed above the boxes. Due to them, the incoming grain is divided into separate streams. This ensures uniform movement of the product along the height of the entire shaft and eliminates the creation of stagnant zones.
The spent heat carrier (air) is sucked through the exhaust ducts by a fan and sent to the cyclone.
An unloading device is installed at the output. It regulates the residence time of the product in the mine. Using a screw conveyor, the grain is fed into the 2nd stream of the elevator (lifting mechanism). Further, the product is sent either repeatedly to the mine, or to a container for dried grain.
In a shaft-type grain dryer, the chamber is divided into three vertical zones: the first and second for direct drying, and the third for cooling.
In the 1st zone, air temperature is controlled by the heat block nozzle. In this compartment of a shaft dryer , surface moisture is usually removed from the product. In the second zone, capillary moisture is eliminated. The temperature here is lower than in the first compartment. Temperature control in the second zone is carried out by gates in the inlet channel.
SZSh-16
This unit is installed in cleaning and drying complexes and is used for drying feed, seed and food grains.
The design of this shaft dryer consists of the following elements:
- 2 fans.
- Fireboxes.
- Exhaust pipe.
- Diffuser.
- Drying chambers.
- Bunkers.
- Nori.
- Grain-conducting pipes.
- Cooling columns.
- Gateway shutter.
- Unloading device.
- Branch pipe.
- The pipeline.
Firebox
This is an independent unit connected to a shaft dryer . It is mounted in a separate building.
The coolant is obtained by mixing flue gases with air or by heating the latter. In the first case, the efficiency of the unit will be higher. In this regard, heated air is used only when drying food lots of cereal crops and grain.
The coolant arrives through the pipeline and the inlet diffuser.
Drying chamber
It is a mine, the size of which is 980 * 1980 * 3650 mm. The shafts are mounted on a concrete base in such a way that the space formed between them is blocked by a supply diffuser. A pipeline is connected to it.
Diffusers are installed on the side walls of the chambers, which are used to exhaust the exhaust air. They are connected to the nozzle and the suction ventilation window. In the pipe there are blinds with a regulator.
Mine features
The design includes a frame, walls, five-sided boxes. In a row there are 8 boxes. The edge of each of them is directed up, and the open part is down.
The ends of the supply ducts are connected to the windows located in the wall facing the interspace.
Silos
They are mounted above the mines. Bunkers have a closed design.
Sensors of the lower and upper levels of grain material are installed on their vertical walls, which automatically control the unloading device. It is located in the lower zone of each mine.
Unloading device
It consists of a fixed tray box. There are 8 windows and a movable carriage on which the plates are fixed.
Under the action of a special mechanism, the back and forth movement of the carriage is carried out.
The regulation of the speed of grain in a shaft dryer is carried out by changing the gap between the plates of the carriage and the outlet windows, as well as the amplitude of the vibration of the plates. For each turn, a portion of grain is dumped into the hopper. The result is a continuous unloading of the dried product, the movement of the entire volume of the grain material from top to bottom.
The clearance is adjusted between 0-20 mm by raising and lowering the carriage. The amplitude of the oscillations is regulated by changing the relative position of the drive eccentrics.
Acceleration of unloading of grain material is provided by a special switching mechanism. With its help, the carriage moves to a large amplitude, as a result of which the outlet openings open completely.
Workflow Features
Wet grain is sent continuously by norias to the silo of each mine. The product enters the space between the boxes. When the grain reaches the upper sensor, the carriage drive is automatically turned on. Under gravity, the product in a shaft dryer begins to move down. When the hopper is emptied to the lower sensor, the carriage drive will automatically be switched off.
During the movement of grain down through it passes the coolant, heats it, evaporates moisture, carrying it away from the dryer.
The product is discharged into the next hopper, then enters the elevator and is sent to the cooling columns. After cooling, the grain enters the next hopper with a lock gate, then it is fed for further processing.
Process control
Periodically, it is necessary to take samples of grain to determine its moisture content and quality. To control the temperature, a special scoop takes 3-4 samples from different parts of the product in the lower boxes. The grain is poured into the box in which the thermometer is installed.
If the temperature is above the maximum permissible, the release of material from the dryer increases. If the humidity remains elevated, the product is sent for re-processing.
After 5-7 days of operation, the shaft dryer must be cleaned.
Dryer series "Vesta"
The VESTA shaft dryer is considered a universal unit. It can be used for processing cereals, legumes and oilseeds.
The unit is made of galvanized steel, which is highly resistant to aggressive environmental factors.
The tower of the car is conditionally divided into 8 zones, going from top to bottom. Each zone has its own purpose, however, they all perform one common task - free the grain from moisture.
The design of the grain dryer includes:
- Cleaning and distribution area.
- Drying hopper.
- Pre-heating compartment.
- The first heating zone.
- The tracking area.
- The second heating zone.
- Compartment for cooling.
- Unloading area.
At the inlet, the grain material passes through an air separator equipped with a spreading mechanism. At the same time, the grain is cleaned of impurities that appeared during transportation, and is evenly distributed over the entire area of ββthe dryer.
Process control is carried out in an automated mode. The unit is equipped with sensors:
- filling in;
- temperature control;
- heating;
- exhaust air;
- fire zones;
- cooling zones;
- unloading mechanism.
Features of core dryer
This unit is also called modular. Column grain dryers can be vertical or horizontal.
The units use the principle of transverse air flow (hot and cold) through a layer of grain material, which, in turn, passes between the walls made of perforated sheets.
Such grain dryers are called columnar or modular because of the design features of the layout. They consist of columns (modules), the number of which is determined by the performance declared by the consumer.
Work specifics
The mechanism of action of core dryers is quite simple. It consists in the following:
- Grain material is fed to the top of the unit. Here is a screw that distributes the product along the entire length of the machine. Columns are loaded alternately. The dryer may look like a round tower with double walls. In this case, the filling occurs under the influence of gravity, and the upper screw, respectively, is absent.
- The fan starts to pump air into the chamber, which is subsequently divided into 2 streams. One enters the mixing zone, the second is heated by the burner. In the chamber, both streams are mixed using reflectors. This ensures uniform temperature at any point.
- Due to the fact that the walls of the column are perforated, blowing grain is carried out at a constant temperature.
- In the lower zone of the dryer are metering devices. They are called rollers. Their rotation speed controls the time spent by the grain material in the columns. Thus, the necessary processing mode of the product is ensured.
- Unloading of grain material is carried out by the bottom scraper or screw conveyor.
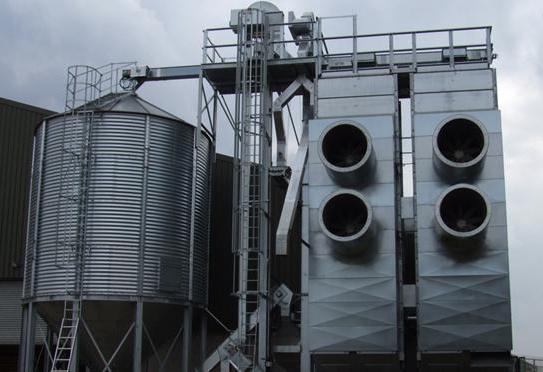
Flat perforated walls are under constant grain pressure. In this regard, a powerful and complex frame is provided in the dryers. When feeding grain material should be distributed along the dryer. Then it must be assembled. In this case, uniformity of the process in parallel sections should be ensured. To do this, the design includes paddle dispensers and screw conveyors.