Welding is a technological process for obtaining reliable joints by heating the edges of the parts to the melting temperature. Manual arc - its most common form. This method is highly productive, versatile, technologically simple and available at home.
The essence of RDS
The edges of the parts to be joined are melted due to the released heat by an ionized stream of particles between the cathode and the anode - an electric arc. Ionization occurs due to the presence of current and a short circuit between the two poles with constant or variable characteristics.
The tool used to create and burn the arc is an electrode - a rod of metallic or non-metallic origin. Work can be performed by one or several rods with the possibility of creating an additional arc between them (three-phase arc welding). The ionized stream of electrons is surrounded by vapors from the tool and its coating, the melting metal of the parts to be joined, the results of their interaction with air. The types of electrodes for welding are determined taking into account all the characteristics inherent in a particular material.
Classification of rods by material
At its core, all welding tools for RDS are divided into melting and non-melting.
- Melting: metal tools made of cast iron, steel, aluminum, copper (depending on the type of metal being welded). The rod acts as a cathode or anode, and also acts as a filler material to fill the weld pool and form a seam.
- Non-consumable: carbon rods, from graphite, from tungsten; perform only the primary function; additionally used filler metal wire; Tungsten is needed for argon arc welding.
Among the first group, the
main types of electrodes are distinguished:
- Without cover. This type of tool is not used for RDS.
- Covered. The appropriate coating is used to maintain arc stability, protect the metal from burnout, from the influence of gases, increase the mechanical characteristics of the seam by natural alloying (ingress of alloying elements from the melting rod into the weld pool).
Application by type of work
The types of electrodes for manual arc welding listed above have individual applications depending on the method of work.
Carbon uncoated electrodes - the primary welding invention that belongs to N. N. Benardos and dates back to 1882 - are used in modern times. Features: direct current, direct polarity, additional filler wire feed, stable arc, the rod burns slowly, carburization does not occur. The use of reverse polarity reduces the characteristics of the arc and the seam (it is carbonized).
Metal electrodes are the next invention in the field of welding technology, which belongs to N. G. Slavyanov (1888). Together with them prototypes of modern welding machines were born. Welding using melting rods has found wider application in industry and has been actively developed. Today it is used in manual arc, automatic and semi-automatic (submerged arc) welding.
Due to the high melting point of 3422 ยฐ C, a tungsten electrode is used as non-consumable in argon-arc welding. Thus, specific types of electrodes correspond to different welding technologies.
Distribution by purpose
Appointment is that characteristic according to which absolutely all known electrodes are distributed. Types and application of rods is indicated by one letter (GOST 9466-75):
- structural steels, including low alloy steels with a strength of 60 kgf / mm 2 (600 MPa) are marked with the letter โUโ in the marking - carbon;
- alloyed structural steels having a strength of 600 MPa - "L";
- high alloy structural steels - โBโ;
- heat-resistant alloy steels - โTโ;
- alloys with special properties, which are characterized by surfacing - "N".
The purpose is indicated in the expanded stamp.
Rod Coatings
Coatings of various composition and origin are used in individual cases for various materials. The following types of electrode coatings are used:
- Sour "A". Contain ferromanganese and ferrosilicon. They are used for direct or direct current. They are characterized by high melting rates. Better to use for lower seams.
- Rutile "P". Contain rutile (titanium dioxide), carbonates, aluminosilicates, ferromanganese, water glass. Welding seams of any position and type with direct or direct current. As a result of successive chemical reactions, protective slag is formed that prevents the elements from burning out. Good quality welded joints, low toxicity.
- Cellulose "C". The composition includes cellulose, manganese ore, talc, rutile, ferromanganese. Shielding gases form around the arc and weld pool. For all seams; high speed of work; good quality; overheating should not be allowed; large spray losses. Used for permanent pipe connections .
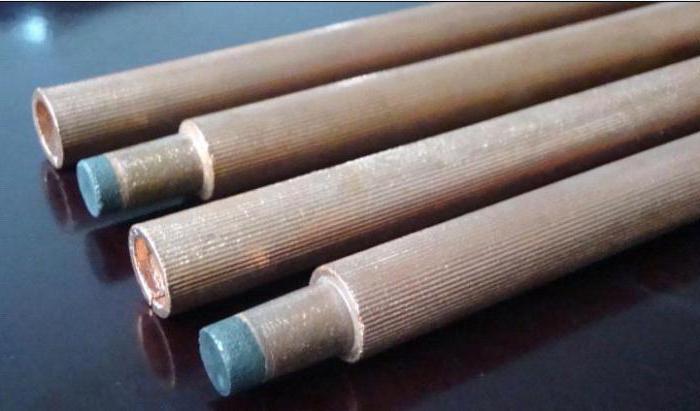
- The main "B". It contains calcium carbonates and fluorides. The formation of protective carbon dioxide occurs due to the reaction of carbon from carbonates with combustion oxygen. It is advisable to carry out work under direct current with polarity in the opposite direction. During welding under a variable, a low-quality seam is obtained, additional technologies are required to increase its mechanical characteristics.
- Other "P". Contain alloying elements. The quality of the seam is improved by introducing into it a certain amount of alloying elements from the melting electrode.
- Special Contain liquid glass with resinous substances. Protect from moisture. They are used for welding under water.
All coated electrodes have specific uses. The main type of coating is rutile due to its versatility. Coatings perform protective functions by deoxidizing the alloy in the weld pool, adding alloying elements to it, forming a halo of protective gases or slag. This avoids the lower quality of the weld than with the materials of the edges of the parts, and ensures the formation of solid welded joints.
Requirements for tools established by GOST 9466-75
- Electrodes must be made of quality material.
- The coating should be solid, not have significant defects (the existence of small dents and cracks without blisters and porosity is allowed).
- High mechanical resistance to accidental shock loads.
- Different types of coating of the electrodes should be uniformly melted, not crumble, not form uneven islands, not spray over acceptable characteristics.
- The core should ensure the formation of a high-quality weld: without cracks, pores, local excess of deposited metal.
- A rational choice in accordance with all the necessary parameters and adherence to technology is the key to the formation of a reliable, durable connection.
Rod selection based on size
A novice welder is more familiar with the types of electrodes that are determined by size. The diameter of the tool with which the work will be carried out is selected strictly in accordance with the thickness of the welded part. It is not encrypted, but is clearly indicated in the marking of the instrument. The length of the electrode is also fixed in accordance with its diameter. It is important to understand the length of the stripped bare end of the tool.
Thickness of prepared edges, mm | Diameter of electrode, d, mm | Electrode length mm | Stripped bare end length, mm |
up to 2 | 2 | 200-250 | 20 |
from 3 to 5 | 3-4 | 300-450 | 25 |
from 6 to 8 | 4-5 | 350-450 | 25 |
from 9 to 12 | 5-6 | 350-450 | thirty |
from 13 to 15 | 6-7 | 450 | thirty |
For home welding, the most commonly used types of electrodes for arc welding with a diameter of 2-4 mm. Thick rods are applicable in repair shops and in production.
Coating thickness
It has its designation in the marking of the instrument. It is determined by the ratio of its ratio D (mm) to the thickness of the rod d (mm). It is distributed in 4 groups:
- thin โMโ (coefficient up to 1.2);
- average "C" (the coefficient has values โโranging from 1.2 to 1.45);
- thick "D" (coefficient - in the range of 1.45-1.8);
- Extra thick โGโ (coefficient value over 1.8).
The results of the work are affected not only by the types of coatings of the electrodes of manual arc welding, but also by the thickness of the coating layer itself, as well as the dimensions of the rod. Correct selection of the electrode size ensures good work speed, high-quality parameters of the arc and the formed joint.
The choice of rods depending on the type of seam and its spatial position
Seams have several classifications:
- Depending on the action of the main forces: flank, frontal, oblique, end.
- In accordance with the position of the parts to be welded: butt, corner, tee, overlay joints.
- Depending on the presence of bevel edges: with bevel, without bevel.
- In accordance with the position in space: lower, upper, horizontal, vertical.
The choice is affected by the spatial position of the seam. Its type is indicated in the marking of the rod.
- 1 - for welding in all positions;
- 2 - exceptions apply only to vertical seams from top to bottom;
- 3 - for the lower seams horizontal at the vertical plane, vertical from bottom to top;
- 4 - for the lower seams.
The seam type relative to the spatial position is taken into account when determining the current values.
The influence of the electric parameters of the arc on the choice of welding tools
Welding can be carried out under direct or direct current, direct (โminusโ on the electrode, โplusโ on the product) or reverse polarity. The choice depends on the material being welded and its properties. The type of current is determined by the power source.
As the main equipment that generates and (or) converts current, transformers and oscillators (reduce the network voltage to the required values), converters and rectifiers (convert the alternating current of the network to direct current of the welding process) can be used.
The parameters necessary for ignition of the arc are significantly different from those that are traced during its maintenance. The voltage required to quickly arc is called open circuit voltage. Consider the voltage values โโnecessary for ignition of the arc and to maintain its burning.
Type of current | Open circuit voltage, V | Voltages for maintaining the arc, V |
Variable | 50-80 | 20-30 |
Constant | 45-50 | 16-25 |
The types of welding electrodes differ depending on the network characteristics and are indicated by numbers from 0 to 9:
- 0 - only for direct current of reverse polarity;
- 1-9 - for any currents;
- 1, 4, 7 - any polarity;
- 2, 5, 8 - straight line;
- 3, 6, 9 - reverse;
- 1-3 - open circuit voltage 50 V;
- 4-6 - 70 V;
- 7-9 - 90 V.
The choice affects the features of the technology and the quality characteristics of the seams. So, the smallest penetration depth is provided by working with variable network parameters. It is used for unpretentious materials and simple designs. When welding with an arc with constant characteristics and reverse polarity, the depth of the weld pool and the mechanical properties of the weld are 50% higher than even with direct polarity. Use for stubborn materials and responsible designs.
Current Definition
In manual arc welding, it can be different - from 30 to 600 A. The required value is selected depending on the diameter of the working electrode and the type of weld relative to the spatial position. It is calculated as follows:
- For the lower seams: I = d * k.
- For the upper ones, I = k * d * 0.8.
- For horizontal - I = k * d * 0.85.
- For vertical joints - I = k * d * 0.9.
where I is the current strength, A;
d is the diameter, mm;
k is the coefficient, A / mm.
The coefficient depends on the diameter of the rod:
- for electrodes with a thickness of 1-2 mm - k = 25-30 A / mm;
- 3-4 mm - k = 30-45 A / mm;
- 5-6 mm - k = 45-60 A / mm.
Increased strength speeds up the welding process. Excessive values โโcan lead to overheating of the edges, excessive burnout of components, deterioration in the quality of the weld.
Marking
In order to consider all the nuances of marking, it is important to give a standard example in accordance with GOST 9466-75 and 9467-75: (E42A-UONI-13 / 45-3,0-UD) / (E432 (5) -B10).
- Brand: UONI-13/45.
- Type: E42A - electrode for RDS, provides a weld strength of 420 MPa with increased ductility (A).
- 3.0 - diameter 3 mm.
- U - for welding carbon steels and low alloy structures.
- D is a thick coating.
- E432 (5) - indices in which the characteristics of the compound and the deposited metal are encrypted.
- 43 - tensile strength not less than 430 MPa;
- 2 - elongation of at least 24%;
- 5 - welding is possible at temperatures up to -40ห; this ensures the minimum allowable impact strength of the metal 34 J / cm 2 .
- B - the main coating.
- 1 - spatial position of the seam: any.
- 0 - welding only by an arc with constant characteristics and direct polarity.
The use of various types and brands of welding tools
Everything discussed above relates more to the marking of electrodes for RDS steel. It is important to give examples of the rods used for a variety of ferrous and non-ferrous metals. Below are their most common types.
The types of electrodes are distributed depending on the metal being welded and the specified typical mechanical characteristics of the weld.
Low-alloy carbon steels are welded with rods of the types:
- E42: brands ANO-6, ANO-17, VCC-4M.
- E42: UONI-13/45, UONI-13 / 45A.
- E46: ANO-4, ANO-34, OZS-6.
- E46A: UONI-13 / 55K, ANO-8.
- E50: WCC-4A, 550-U.
- E50A: ANO-27, ANO-TM, ITS-4C.
- E55: UONI-13 / 55U.
- E60: ANO-TM60, UONI-13/65.
High strength alloy steels:
- E70: ANP-1, ANP-2.
- E85: UONI-13/85, UONI-13 / 85U.
- E100: AN-XH7, OZSh-1.
High-strength alloy steels: E125: NII-3M, E150: NIAT-3.
Metal surfacing: OZN-400M / 15G4S, EN-60M / E-70Kh3SMT, OZN-6 / 90Kh4G2S3R, UONI-13 / N1-BK / E-09Kh31N8AM2, TsN-6L / E-08Kh17N8S6G, OZSh-8 / 11M3UF11.
Cast iron: OZCh-2 / Cu, OZCh-3 / Ni, OZCh-4 / Ni.
Aluminum and alloys based on it: OZA-1 / Al, OZANA-1 / Al.
Copper and alloys based on it: ANTs / OZM-2 / Cu, OZB-2M / CuSn.
Nickel and its alloys: OZL-32.
From the above list, we can conclude that the marking system is very complex, while it is based on approximately the same principles of encoding the characteristics of the rod, its coating, diameter, and the presence of alloying elements.
The quality of the welding joint depends on a rational technological scheme. What types of electrodes to choose are influenced by the following factors:
- The material to be welded and its properties, the presence of alloying elements and the degree of alloying.
- The thickness of the product.
- Type and position of the seam.
- Specified mechanical properties of the joint or weld metal.
It is important for a novice welder to navigate the basic principles of selecting and marking tools for steel welding, as well as to operate with the distribution of the grades of rods according to their purpose, to know the main types of electrodes and to rationally apply them during welding work.