Chemical, mechanical, and electrical external influences often occur in metal product operating environments. As a result, with improper maintenance of such elements, as well as ignoring safety standards, there may be risks of deformation and damage to structures and parts. This is due to the occurring processes of corrosion and erosion of metals, which in the long term contribute to the complete destruction of the structure of the product.
Why does rust appear
In a corrosive reaction, conditions for structural failure of metal products create contact with chemical and electrochemical media. In the first case, the material comes into contact with petroleum products, coal, salt and other minerals. Electric current is not involved in this case. The main operating environment may be dry gas or non-conductive liquid. The greatest destructive effect is exerted by light grades of petroleum products like kerosene and gasoline. In particular, sulfur compounds and acid residues present in their composition may affect the hull of an offshore shipping tanker.
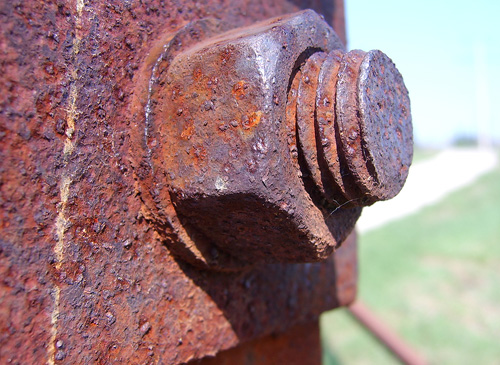
In electrochemical corrosion, an electric shock also occurs. Complex destruction with metal erosion will also be accompanied by mechanical wear. The situation may be complicated by the fact that external factors will themselves be determined by the characteristics of the natural environment - for example, chemical reactions with electrolytes can take place in sea water. The metal case itself is a material heterogeneous in structure, which leads to the presence of microvoltaic pairs. They, together with the metal sections of the structure, act as anodes, creating conditions for the process of corrosion.
Causes of erosion
In general, erosion is understood as mechanical wear, as a result of which the product can vary in size, shape, weight and other characteristics. What causes metal erosion? Physical processes of external influence, which reduce the strength of microvolumes of the surface layer of a structure or an individual part. Moreover, influencing media are not only mechanical factors such as direct contact with solid abrasives.
It can be both thermal, gas, and chemical active media, and they can act both independently and as an additional factor of wear. For example, gas flows contribute to the movement of solid particles in the delivery circuit of working mixtures through the pipeline, which have an indirect destructive effect on metal surfaces.
Methods of protecting metals from corrosion
Practice shows that 80% of the conditions for protecting materials from corrosion are laid down even at the stage of surface preparation. The remaining 20% ββis provided during operation. Approximately the same ratio of the effectiveness of protective measures is also noted during metal erosion, when means are used to minimize wear on the workpieces.
The main directions of creating corrosion protection include structural, passive and active. Structural protection is determined by the use of special alloys based on stainless steel, Corten steel and colormet. Active methods involve changing the structure of a material with a double electric layer - a method of electrochemical protection. As for passive methods, they provide for the use of special coatings that prevent the formation of a corrosion element.
Varieties of metal heat treatment
A group of methods for the technological processing of metal billets, which also focuses on the structural change of the surface layer in order to protect against corrosion damage. The following types of processing are distinguished:
- Annealing. Heat treatment in which the metal is heated, followed by smooth cooling.
- Quenching. The target products may be steels and their alloys. During quenching, the structure recrystallizes, and after the material is held at the critical temperature, cooling follows. A component that has undergone such processing forms a nonequilibrium structure, which is the limiting factor in choosing this method.
- Vacation An alternative method of heat treatment of metal with respect to quenching, which can also serve as an auxiliary step in structural changes. In any case, during its implementation, excessive stresses of steel are removed, which leads to an increase in anticorrosive qualities.
- Normalization. Processing similar to annealing. The difference is that during annealing, cooling occurs in the furnace, and during normalization - in the air.
Methods of protecting metals from erosion
The main direction in protecting metal materials from erosion is the development of special coatings. In particular, metallization in the form of applying an anticorrosive alloy to a workpiece increases the chemical and mechanical properties of the structure. As a result, wear is reduced, and the design of the part can maintain its previous performance characteristics.
Non-metallic wear-resistant coatings for specific applications are also being developed. For example, metal erosion formed under rubbing surfaces is often found in vehicle parts. For this kind of protection, diamond-like, ceramic and combined compositions with increased strength and hardness are used.
Features of protection against gas erosion
In this case, the emphasis is not on the mechanical protection of parts, but on chemical and physical isolation. Can be used as special modes of content and storage of materials, and special lubricants that prevent erosion of metals. Methods of protection against wear and its prevention are based on thermal insulation.
Materials such as pure chromium and Nairit grade NT are used in this direction. The disadvantage of chromium is that it is characterized by a lack of viscosity and ductility. For this reason, it is rarely used as an element of structural insulation. As for nairite, gumming liquid mixtures are made on its basis, through which monolithic wear-resistant seals are formed.
The method of protection by thermal spraying
This is a universal protection technology, which is suitable in the case of corrosion prevention, and when isolated from factors of mechanical wear. The technique of its application is that zinc particles are applied to the surface of a part with a gas jet. Unlike other metallization methods, this method forms a protective layer up to tens of microns thick. Thus, erosion processes occurring in the nodes of engineering equipment, as well as in transport networks and highways of large oil pipelines, are prevented.
Conclusion
The processes of negative impact on metal structures force operating companies to spend considerable amounts on their maintenance. In this case, the most effective means of protection, as a rule, are more expensive. On the other hand, preliminary studies of the conditions of use of products for risks of rust or metal erosion can minimize such costs. The fact is that many technical and protective properties of critical structures are laid at the stage of alloy selection. By alloying and introducing modifying additives even at the stage of manufacturing the part, it is possible to provide it with optimal protective qualities.