Powerful precision machines are used in industry to process solid-state workpieces. They are characterized by a high frequency of rotation of the cutting tool, which allows for fine-tuning the product to the required dimensions. But it is impossible to qualitatively implement such operations without appropriate nozzles.
Traditional alloys, even made of tool steel, do not always withstand peak loads, which forces operators to look for more suitable consumables. Elbor boring cutters, or rather inserts that increase the reliability of the main processing element and increase the efficiency of mechanical action on the workpiece, can solve this problem.
Elbor Overview
The most popular material used in manufacturing as a cutting part is diamond. It has a high degree of hardness, withstands heavy loads and is characterized by durability. In turn, elbor can act as an alternative to a natural mineral. In terms of mechanical properties, it is practically not inferior to diamond, and in terms of hardness it is 3-4 times higher than traditional abrasive consumables. At the same time, the elbor as such is not fully cutting equipment.
The processing part has a prefabricated structure, the main part of which can be made of common solid-state and tool steels. At the end of such elements, the elbor plates for the cutters, which directly perform mechanical abrasive action, are fixed. These are inserts based on crystals, which are cubic boron nitride. The shape and dimensions of the patch plates may vary depending on the purpose and design of the supporting part.
Operational features of elbor equipment
Even against the background of carbide and mineral-ceramic incisors, the technical and physical properties of the elbor are impressive. Suffice it to say that it can demonstrate resistance to machining, many times higher than the performance of the above materials. This allows, for example, at a spindle speed of about 500 m / min, the correction of cast iron blanks. Thus, a rough mechanical refinement is manifested, but the elbor cutters can very well be used in the finishing formation of the contours of parts.
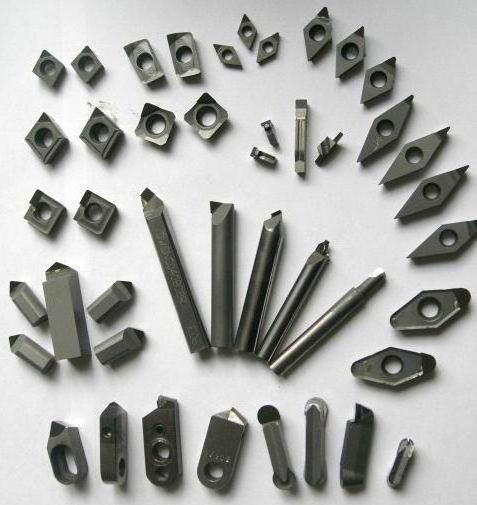
By the way, the depth of liquidation of the outer layer can reach 0.1-0.2 mm. The cutting ability of the elbor itself is characterized in that it takes less effort from the machine to complete the processing. On the one hand, this makes it possible to effectively cope with solid-state alloys, and on the other hand, in servicing less problematic workpieces, spend the minimum amount of energy resources of the equipment. Reducing the requirements for power potential is due to the peculiarities of the mechanical contact of the elbor with the surface of the workpiece.
Characteristics of elbor cutters in accordance with GOST
The structural parameters and dimensional characteristics of the parts are carried out in accordance with the general standards applicable to diamond brazed elements. In particular, you can focus on GOST under sections 13288 and 13297-67. In accordance with the technical requirements, the length of the product can vary from 40 to 125 mm. The step in this case will be 20 mm - that is, there are consumables of 40, 60, 80 mm, etc. In this case, the length of the working part itself varies from 10 to 40 mm - this indicator also determines the diameter of the functional base, which is the elbor cutter. GOST indicates that the thickness of the inner core of the part should be from 6 to 12 mm. The total diameter varies from 10 to 40 mm. That is, it can be both thin elements for fine grinding, and massive cutters for rough surface shape correction.
Processing conditions
To maintain optimal processing parameters, the creation of special conditions is required under which the equipment can provide a high-quality result. It is recommended to use cutters in the absence of vibration effects and the effect of beating. A high amplitude of vibration can lead to chipping of the linings.
One of the most common consumables of this type is an elbor boring cutter, through which the ends of workpieces made of hardened steel are refined. In such operations, experts advise performing multi-stage processing in different modes. Accordingly, depending on the requirements for the final result, different combinations of rough turning and fine grinding are used at a speed range of 60-80 m / min. When working with several planes, in which it is also planned to make holes for the bushings, it is recommended to first boring, and then proceed to drilling.
Positive feedback on details
In practice, the operators of machine tools provided with elbor components show a high degree of resistance with an effective mechanical impact on the workpiece. In a short period of time (compared with traditional carvers), users receive the product of the desired shape, regardless of the base material.
At the same time, the advantages of equipment in terms of maintenance are also indicated. This is the case when the tool has the effect of self-sharpening. That is, the elbor cutters maintain an optimal working condition without requiring special shape correction. For this reason, the risk of losing the desired geometry of the cutter due to improper editing is eliminated. At the same time, operators emphasize the absence of the need to take care of maintaining the temperature balance in the cutting part. The material copes with thermal stress loads, so water cooling may not be used.
Negative reviews
Since the elbor was originally developed as a material for sharpening, taking into account all the nuances of the process, there is practically no criticism of its performance. Unless it is worth noting the skeptical attitude of turners to cutters with overlays as such.
If in terms of the effectiveness of abrasive action they fully justify themselves, then the design features imply certain restrictions on the use of such elements. But this applies not only to elbor inserts for incisors, but also to diamond analogues.
Scopes of Elbor consumables
This equipment is used in almost all areas of metalworking industries. Depending on the specialization of the enterprise, the tool can perform sharpening, finishing adjustments, grinding operations, etc. It is important to emphasize that, unlike many traditional elements for metal processing, the elbor boring cutter effectively copes with both preliminary and final finishing of products. As for the range of target materials available for such processing, these include not only cast iron and hardened steels, but also high-strength mineral-ceramic billets.
Conclusion
Carvers of this type, of course, are impractical to use for most metal processing tasks that have average hardness. Moreover, soft alloys can be deformed with such a tool. Therefore, it is worth talking nevertheless about the narrow specialization of the Elbor cutter. The price of the tool also limits its use - an average of 1.5-2 thousand rubles.
It is obvious that household models of lathes with such consumables should not be equipped. However, if the working properties of conventional carbide cutters are lost, the user will have to turn to companies offering elbor sharpening services. If we talk about alternative options, then the same will be the same diamond cutter. It is more adapted to the common tasks of processing metal products of varying degrees of hardness. But in working qualities with respect to high-strength dense workpieces, diamond parts lose to Elbor.