The 676 milling machine is a universal equipment used for milling various parts. The unit can work with key, end, disk and other types of mills. The configuration of the machine makes it possible to mill workpieces horizontally and vertically, which significantly expands the capabilities of the unit.
Description
The multifunctional milling machine 676 can be equipped with a swivel-vertical spindle or its horizontal counterpart. The first option allows you to process parts using face and key mills, and in the second case, shaped mills, as well as disk and cylindrical analogues, are used.
The main difference between the equipment under consideration and similar machines is the presence of a second spindle head, which is adjustable in perpendicular planes. The unit in question can use both spindles at the same time. In addition to milling, the equipment is designed for drilling, coredrilling and boring.
In the industrial field, the 676 universal milling machine is used to perform a number of operations, namely:
- Carrying out processing of internal and external surfaces, including rotational bodies, by turning method.
- Cutting ledges and grooves.
- Turning the splines on the shafts.
- Formation of gear configurations.
Features
Milling machine 676 is classified as a high-precision milling machine (class H). Maximum processing accuracy is achieved if during operation there are no sources of vibration near the unit, the ambient temperature is within 20 ° C, and humidity is about 65%.
The equipment in question is used in single and small-scale production, mainly at machine-building enterprises and tool factories. The popularity of the 676 milling machine is influenced by a number of advantages compared to its competitors:
- The skeleton of the equipment is made of cast iron, has a large mass, providing reliable stability without vibration, which guarantees high-precision processing.
- The versatility of the equipment allows you to work with small workpieces and parts up to 0.8 m long and 0.25 m wide.
- The unit can be equipped with a grooving tip, with the ability to perform appropriate operations.
- The relatively small dimensions of the machine make it possible to place it even in an ordinary garage.
- The multilevel range of rotation of the spindle heads contributes to the optimal selection of metal finishing modes, depending on their hardness.
676 Milling Machine : Specifications
Below are the technical parameters of the equipment in question:
- The size of the horizontal / vertical desktop is 250 * 800/250 * 630 mm.
- The maximum weight set for processing the workpiece is 100 kg.
- The axial distance from the spindle to the table is 80-450 mm.
- Spindle extension - 125-375 mm.
- Spindle head travel along the X / Y axes (maximum) - 300/380 mm.
- Spindle speed (horizontal / vertical) - 1630/2040 rpm.
- The number of speeds is 16 pieces.
- Overall dimensions - 1200/1240/1005 mm.
- Weight - 1000 kg.
- Electric drive power - 3 kW.
In addition, the 676 universal milling machine is equipped with an auxiliary coolant supply system with a motor, from which an electric pump with a capacity of 23 liters per minute is activated.
Differences between the 676P and SF-676 models
Modification 676P from SF-676 differs slightly:
- Has an axis distance of 10 mm less from the table to the spindle.
- The vertical movement of the spindle head is 250 mm.
- The power rating of the main electric drive is 2.2 kW.
- Weight - 910 kg.
- Dimensions - 1260/1210/1780 mm.
The 676P universal milling machine belongs to outdated modifications, and is not available now. It can only be purchased in the secondary market.
Device
The bed of the machine 676 is made of cast iron, serves as a bearing base with the main structural elements fixed on it. On the left side of the bed there is a speed block and a feed box. On the upper surface of the skeleton, a headstock moves with a horizontal spindle installed. If necessary, a vertical spindle device is mounted on this element.
The support is mounted on vertical guides, the table on horizontal elements. The machine is equipped with a main horizontal table and an additional vertical counterpart. Workpieces with sizes up to 800 mm in length and 250 mm in width are fixed on the main workbench.
The electric drive of the unit is located in the lower part of the core, placed on a support in the form of a plate, inside of which a container for coolant is provided. All electric filling of the machine is located under the bed cover in the upper part. This design does not impede access to components for repair or maintenance.
The main functional parts of the milling machine are a support and a spindle head. The purpose of the support is to hold and move the desktop in the transverse-longitudinal plane. The element is driven by a running shaft transmitting torque from the power unit to the feed box.
The headstock aggregates with the feed box through drum gears, the spindle itself is mounted on radial and ball bearings. The accuracy of its movement provides an indicator holder.
Maintenance
The universal machine SF-676 requires regular maintenance. It is necessary:
- After 10 hours of operation, lubricate with special machine oil guides and spindles.
- Lubricate linear bearings every 40 hours.
- After 400 hours worked, inspect and adjust the belts in the feed box, as well as tighten the screw assemblies.
Before the first working start of the machine, it is necessary to check the reliability of the fixing of the safety covers, clean the working table of liquids and lubricants, turn on the unit and check its idle speed.
Health Check
This process begins with running the equipment at minimum speed, gradually increasing it to the maximum rate. On the main working transmission of rotation, the machine must work for at least two hours, while the spindle bearings cannot be heated above 50 degrees.
After checking the unit at idle, it is subjected to a load. The milling cutter must work at the maximum cutting force in the mode of short-term 25% overload. During normal operation in this mode, the appearance of vibrations is not observed and high processing accuracy is maintained.
Milling cutters for milling machine
The variety of cutter configurations allows you to select material in the most inaccessible areas, so that the part takes the required dimensions and shapes.
Milling cutters are classified according to the location of the cutters, the type of construction, direction, shape of the teeth, the method of attachment and the material of the cutting tool.
Modifications:
- Disk milling cutters are used for trimming workpieces, sampling grooves, metal, chamfering. The cutting part of such elements can be placed on one or both sides.
- Face mills work with step-type flat workpieces. The working part of the tool is the end face, its axis of rotation is perpendicular to the surface of the workpiece.
- A cylindrical metal mill for a milling machine can be with helical or straight teeth. The first option allows you to smoothly process the workpiece, and the second configuration - to trim narrow planes, so this tool belongs to the universal category.
- Corner options. Such milling cutters are used for processing inclined surfaces, have a conical configuration. Distinguish between one and two-angle modifications, characterized by the location of the cutting edge.
- End mills are designed to create grooves, contour grooves, ledges and processing mutually perpendicular parts.
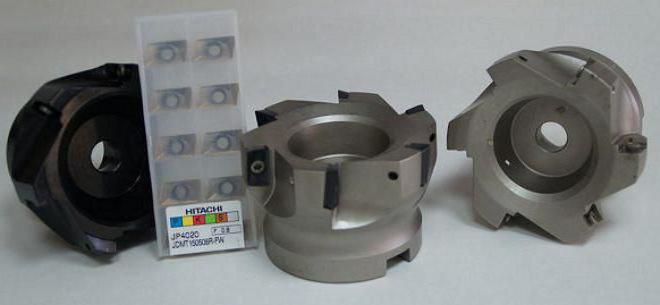
There are also shaped, worm and ring cutters. They serve for machining shaped surfaces and workpieces of extraordinary configurations and further expand the capabilities of the 676 machine.