Instruments for analyzing the structure of materials are widespread in the areas of construction, production, and sometimes used by home craftsmen. Using such an apparatus, the user can determine the presence and parameters of a physical defect in the product. For example, to detect a crack, tear, deepening, large pores, etc. For such examination tasks, different device models are used, but magnetic particle flaw detectors are considered the optimal solution due to the combination of favorable working qualities. With a sufficiently high accuracy, the apparatus requires minimal effort in organizing the research process, has a wide field of application, and at the same time allows the detection of various types of structural violations in the basis of the material.
Principle of operation
Magnetic particle analysis technology refers to non-destructive testing methods. This is a group of flaw detection methods, thanks to which the operator records violations in the structure of individual sections of parts, structures, blanks, etc. The inspection is carried out by magnetizing the target zone with a field that is formed by the device under the influence of direct or pulsed current. If the material at a particular site is characterized by uniformity and normative indicators of density with hardness, the magnetic scattering field will not give signals indicating the presence of structural violations. Conversely, magnetic particle flaw detectors give appropriate signals about the presence of various kinds of discontinuities if there are deviations from the standard on the surface or inside the object. Especially for working on surfaces, auxiliary active agents are also used to visually fix cracks and other defects. For this, magnetic powders and liquids are used, the behavior of the particles of which also gives information about various structural violations.
Device device
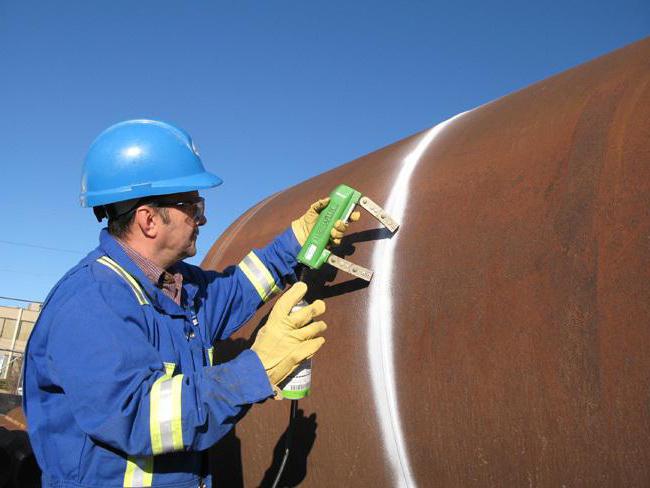
The basis of any equipment of this type is electromagnetic filling. It can be generators, converters and diffusers of currents acting on the background of magnets. For the parallel formation of the magnetic field, corresponding coils are also used. The configurations of the interaction of two power media can be different. At the moment, models are used to create pole, circulation and combined magnetization. Depending on the tactics of field formation, electric contactors, solenoids, electromagnets and other tools are involved. Magnetic-particle flaw detectors may also include additional devices for supplying consumable active material. They are not directly related to the control function, but in order to ensure user convenience, manufacturers complete the devices with such equipment. It can be sprayers, compressors, atomizers, containers for diluting powders, etc. And at the final stage, the work is done with the help of scanning, photographing and diagramming tools, which show the location points and characteristics of the structure defects.
Types of devices
The classification of flaw detectors is based on the configuration of the basic functional platform. Based on its composition, stationary, portable and manual devices can be distinguished. Representatives of the first category have the greatest opportunities. They not only include the full set of components necessary for comprehensive control, but depending on the version they can support different verification methods. According to its capabilities, a portable magnetic particle flaw detector may look like stationary counterparts, but it also suggests the possibility of movement. That is, such models are allowed for use as part of field events of a comprehensive verification of objects. As for manual models, then, in fact, this is a component of the flaw detector, designed to perform only one of its functions - magnetization of the target area.
Model MD-M
A basic solution that offers a standard set of tools for examining products for defects. In particular, this device analyzes the structure of welds, internal cavities of parts, and also penetrates into inaccessible zones. A feature of the device is the support of two control methods - by applying a field and due to the residual magnetization. The verification results are presented in the process of processing photographic materials in the form of magnetograms. Thus, the operator can map the location of defects in the inspected parts and structures. As for the device, the MD-M magnetic particle detector includes three modules provided by individual power supply units. The main one is the pulse current generator, which forms a magnetic field in the target zone. The solenoid module, in turn, provides magnetization of the part due to the direction of alternating current. An electromagnet is used to create a constant active field.
Model MD-2
A variation of a portable lightweight, but at the same time accurate and effective flaw detector, which is suitable for both industrial and domestic use. By means of this apparatus, it is possible to carry out a manual examination, automatically setting the parameters of a given current - again, constant, pulsed or alternating. After the operation is completed, the MD-2 magnetic particle flaw detector stores the applied characteristics in the memory cells and does not lose them even after shutdown.
The power supply of the device can be provided by a conventional 220 V network, and on-board power supply lines of the vehicle by 27 V. The current is regulated up to 5000 A, and its duration in pulsed mode is 1.5 ms. As in the MD magnetic particle detector, this model also has a โcurrent-pauseโ function. This means that the operator will be able to vary the magnitude of the current direction and the release of magnets with ranges from 1 to 10 s. There also remains the possibility of a stable force field with a different number of periods.
Model MD-12PS
A professional level flaw detector designed to detect surface transverse cracks. In particular, it is used to monitor the state of the elements of a rolling railway. Using the apparatus, locomotive wheelsets, shanks, clamps, automatic couplings, as well as large-sized parts made of magnetic alloys are checked. During operation, the device consumes up to 2.5 kW at a voltage of 220 V. High power allows the use of a magnetic particle detector MD-12PS to form a highly efficient field of 15,000 A / m. Therefore, there are wide opportunities for studying thick-walled structures with a detailed analysis of small elements. But, a mass of almost 60 kg does not allow the device to be used as portable.
Model MD-12PSh
Another version that is used specifically for working with rail. The features of this model of a flaw detector include the characteristics of the sensitivity threshold (length - from 5 mm and cutting width - from 0.02 mm), high magnetization voltage (up to 18000 A / m) and extended standard equipment. In the basic set with a magnetic particle detector MD-12PSh, the owner receives a cervical magnetizing device, a complete list of cable assemblies, a bath, a mug, a powder atomizer and lighting devices. Consumables and test samples for the control operation should be purchased separately.
Flaw detection suspensions
For simple control operations on surfaces in ferromagnetic materials , black oil compositions are used. Such suspensions are applied by spraying, watering or dipping. In order to provide contrast on dark details and structures, background light paint can be additionally applied. Granular powder concentrate is also widely distributed. With its help, an aqueous suspension is prepared, including surface-active particles, magnetic components and functional additives that improve the protective qualities of the active medium as such. For example, it can be inhibitors, plasticizers and anti-foam additives. The most accurate and technologically advanced magnetic particle flaw detectors does not make sense to use without high-quality colored powders with the first sensitivity class. These are dust-free compounds, which include iron oxides and coloring pigments, which allow you to create clear indicator patterns with detailed drawing of defectological maps.
Conclusion
Non-destructive testing methods are becoming more popular due to their advantages, which determines the relevance of magnetic particle research technology. Of course, this is not the only way to implement this kind of checks, but it has its own advantages, which are versatility and accuracy. According to these parameters, for example, the MD-2 portable magnetic particle flaw detector can well compete with ultrasonic monitoring instruments. Another thing is that the cost of devices limits their use in many areas. Stationary multifunctional models on the market are available for 300-400 thousand rubles. Portable and manual equipment can be purchased at prices up to 100 thousand, but it also has a much wider range of capabilities.