In recent years, polyester resins have gained great popularity. First of all, they are in demand as leading components during the production of fiberglass, durable and lightweight structural materials.
Resin Production: Phase One
Where does the production of polyester resins begin? This process begins with the distillation of oil - during this process various substances are released: benzene, ethylene and propylene. They are necessary to obtain antihydrides, polybasic acids, glycols. After cooking together, all these components create the so-called base resin, which at a certain stage must be diluted with styrene. The last substance, for example, can be 50% of the finished product. As part of this stage, the sale of finished resin is also allowed, but the production stage is not yet finished: we should not forget about saturation with various additives. It is thanks to these components that the finished resin gains its unique properties.
The composition of the mixture can be changed by the manufacturer - here a lot depends on where exactly the polyester resin will be used. Specialists select the most optimal combinations, the result of this work will be substances with completely different properties.
Resin Production: Phase Two
It is important that the finished mixture is solid - they usually wait until the polymerization process reaches its end. If it was interrupted, and the material was on sale, it is only partially polymerized. If you do nothing with it, the polymerization will continue, the substance will surely harden. For these reasons, the shelf life of the resin is very limited: the older the material, the worse its final properties. Polymerization can also be slowed down - refrigerators are used for this, hardening does not occur there.
In order for the production stage to be completed and the finished product to be obtained , two important substances must also be added to the resin: the catalyst and activator. Each of them performs its own function: heat generation begins in the mixture, which contributes to the polymerization process. That is, a source of heat from the outside is not required - everything happens without it.
The course of the polymerization process is regulated - the proportions of the components are controlled. Since an explosive mixture can result from contact between the catalyst and the activator, it is customary to introduce the latter into the resin solely as part of production; before use, the catalyst is added, it is usually supplied separately. Only when the polymerization process is completely completed, the substance hardens, we can conclude that the production of polyester resins is completed.
Source Resins
What is this material in its original state? It is a honey-like, viscous liquid, the color of which can vary from dark brown to light yellow. When a certain amount of hardeners is introduced, the polyester resin first slightly thickens, then becomes a gelatinous state. A little later, the consistency resembles rubber, then - the substance hardens (becomes non-melting, insoluble).
This process is called curing, as it takes several hours at normal temperature. When the resin is in a solid state, it resembles a tough, durable material that is easy to paint in a wide variety of colors. As a rule, it is used in combination with fiberglass (polyester fiberglass), it acts as a structural element for the manufacture of various products - such is polyester resin. Instructions when working with such mixtures are very important. Every point must be observed.
Main advantages
Cured polyester resins are excellent structural materials. They are characterized by hardness, high strength, excellent dielectric properties, wear resistance, chemical resistance. Do not forget that during operation polyester resin products are environmentally friendly. Certain mechanical qualities of mixtures that are used in conjunction with fiberglass resemble structural steel parameters in their indicators (in some cases, even exceed them). The manufacturing technology is cheap, simple, safe, since the substance cures at ordinary room temperature, even the application of pressure is not required. Emission of volatile and other by-products does not occur, except perhaps a slight shrinkage. Thus, in order to manufacture the product, expensive bulky installations are not needed, and there is no need for thermal energy, as a result of which enterprises quickly master both large-tonnage and small-tonnage production. Do not forget about the low cost of polyester resins - this figure is two times lower than that of epoxy analogues.
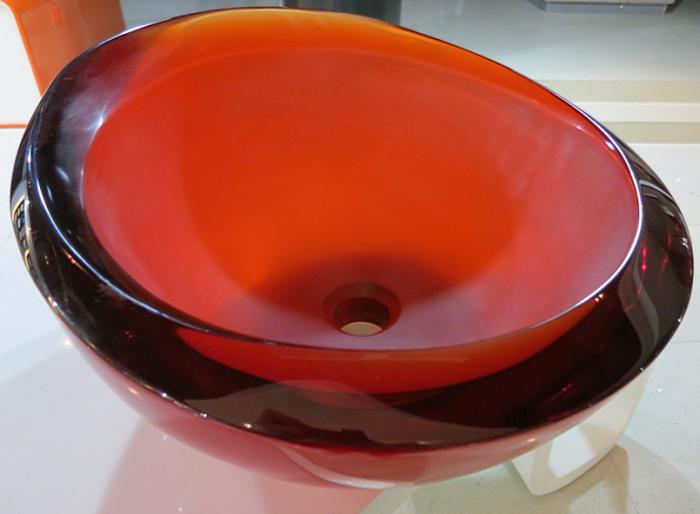
Production growth
We cannot ignore the fact that at the moment the production of unsaturated polyester resin is gaining momentum every year - this applies not only to our country, but also to general foreign trends. If you believe the opinion of experts, this situation will certainly continue in the foreseeable future.
Resin Disadvantages
Of course, polyester resins also have some disadvantages, like any other materials. For example, styrene is used as a solvent during production. It is flammable, is very toxic. At the moment, such brands have already been created that do not have styrene in their composition. Another clear downside: combustibility. Unmodified unsaturated polyester resins burn just like hardwoods. This problem is solved: powder fillers (low molecular weight organic compounds containing fluorine and chlorine, antimony trioxide) are introduced into the composition of the substance, sometimes chemical modification is used - tetrachlorophthalic, chloroedic acid, some multimers are introduced: vinyl chloroacetate, chlorostyrene, and other compounds that contain chlorine.
Resin Composition
If we consider the composition of polyester unsaturated resins, here we can note a multicomponent mixture of chemical elements of different nature - each of them performs certain tasks. The main components are polyester resins, they perform different functions. For example, polyester is the main component. It is the product of the polycondensation reaction of polyhydric alcohols, which react with anhydrides or polybasic acids.
If we talk about polyhydric alcohols, then diethylene glycol, ethylene glycol, glycerin, propylene glycol, dipropylene glycol are in demand here. Adipic, fumaric acids, phthalic and maleic anhydrides are used as anhydrides. Molding a polyester resin would hardly have been possible if the polyester, when ready for processing, had a low molecular weight (about 2000). In the process of forming products, it turns into a polymer with a three-dimensional network structure, high molecular weight (after the initiators of curing). It is this structure that provides chemical resistance, high strength of the material.
Solvent monomer
Another required component is a solvent monomer. In this case, the solvent has a dual function. In the first case, it is required in order to reduce the viscosity of the resin to the level that is required for processing (since the polyester itself is too thick).
On the other hand, the monomer takes an active part in the process of copolymerization with polyester, due to which the optimum polymerization rate and a high curing depth of the material are ensured (if we consider the polyesters separately, their cure is rather slow). Hydroperoxide - the very component that is required to be solidified from liquid - this is the only way that polyester resin acquires all its qualities. The use of a catalyst is also required when working with polyester unsaturated resins.
Accelerator
This ingredient can be introduced into the composition of polyesters both during manufacture and when processing occurs (prior to initiator input). For curing polymers, the most optimal accelerators can be called cobalt salts (cobalt octoate, naphthenate). Polymerization must not only be accelerated, but also activated, although in some cases it is slowed down. The secret is that if you do not use accelerators and initiators, free radicals will independently form in the finished substance , due to which polymerization will occur prematurely - right during storage. To prevent this phenomenon, do not do without a curing inhibitor (inhibitor).
The principle of action of the inhibitor
The mechanism of action of this component is as follows: it interacts with free radicals that periodically arise, as a result of the formation of low-activity radicals or compounds that do not have a radical nature. The function of inhibitors is usually performed by such substances: quinones, tricresol, phenon, some of the organic acids. Small amounts of inhibitors are introduced into the polyesters during manufacture.
Other additives
The components described above are basic, it is thanks to them that it is possible to work with a polyester resin as a binder. However, as practice shows, in the process of forming products, a sufficiently large number of additives are introduced into polyesters, which, in turn, carry a variety of functions, modify the properties of the starting material. Among these components, powdery fillers can be noted - they are specially introduced to reduce shrinkage, reduce the cost of material, and increase fire resistance. It should also be noted fiberglass (reinforcing fillers), the use of which is due to an increase in mechanical properties. There are other additives: stabilizers, plasticizers, dyes, etc.
Glass Mats
Both in thickness and in structure, fiberglass can be different. Glass mat - glass fiber, which is cut into small pieces, their length varies between 12-50 mm. The elements are glued together using another temporary binder, which usually acts as a powder or emulsion. Epoxy polyester resin is used for the manufacture of glass fiber mats, which consist of fibers arranged randomly, while fiberglass with its appearance resembles ordinary fabric. To achieve the maximum possible hardening, different brands of fiberglass should be used.
In general, glass mats have less strength, but they are much easier to handle. When compared with fiberglass, this material better follows the shape of the matrix. Since the fibers are quite short, have a random orientation, the mat can hardly boast of great strength. However, it can be very easily impregnated with resin, because it is soft, while it is loose and thick, somewhat resembling a sponge. The material is really soft, it can be molded without problems. Laminate, for example, which is made of such mats, has remarkable mechanical properties, has high resistance to atmospheric conditions (even within a long period).
Where to use glass mat
Mat finds its application in the field of contact molding, so that it is possible to produce goods of complex shapes. Products made from such material are used in a variety of areas:
- in the field of shipbuilding industry (construction of canoes, boats, yachts, fish cutters, various internal structures, etc.);
- glass mat and polyester resin are involved in the automotive industry (various machine parts, cylinders, vans, diffusers, tanks, information panels, cases, etc.);
- in the construction industry (certain elements of wooden products, the construction of bus stops, dividing partitions, etc.).
Glass mat has a different density, as well as thickness. The material is divided by the weight of one square meter, which is measured in grams. There is a fairly thin material, almost airy (glass), also exists thick, almost like a blanket (used to ensure that the product has found the required thickness, obtained the required strength).