The connection of metal structures by welding is the most common method in construction, instrumentation, production of machines and mechanisms. In the welding process, two surfaces are joined after the base metal is melted by heat. An additional fused element is used, which, after cooling and crystallization, forms a weld or surfacing. Welding material is introduced into the workspace by a melting, current-carrying, non-consumable electrode or gas welding. In the process, materials for welding perform the work:
- during melting, moving in an arc, being in a bath, solidification protect molten metal;
- alloy and deoxidize metal, regulating the chemical composition of steels;
- remove oxides, slags, phosphorus and sulfur from the seam filling;
- release suture mass from nitrogen and hydrogen.
Classification of materials for welding
A large number of materials required for joining metals by welding make it difficult to accurately classify, but the main welding materials are divided as follows:
- filler wire for welding and surfacing;
- for arc welding, piece electrodes;
- wire and plate electrodes for slag welding;
- additive additives of a non-continuous, continuous, tubular section;
- filler filaments, rolled, elongated cast rods and wire, powder coated surfacing tapes;
- flammable gas or oxygen;
- welding equipment, compressor;
- gas cylinders;
- a generator for producing acetylene from calcium carbide or an acetylene cylinder under pressure;
- pressure reducer to reduce the pressure of the welding gas;
- torches for welding, hardening, surfacing with a set of necessary types of tips of different diameters;
- rubber hoses for moving oxygen;
- fluxes and powders for welding.
Melting wires, plates and rods
This type of electrode is used for welding in shielding gases, submerged arc, electroslag. Steel wire, as a welding material, is divided into high-alloy, low-carbon and alloyed. In total, 77 types of similar products are determined by assortment. Selecting the required grades, change the chemical composition of the seam. Typically, a wire composition similar to the metal being welded is used. The characteristic of the welding material must comply with GOST and is indicated on the packaging.
Alloyed and low-carbon steels for the manufacture of wire are divided into copper-plated and non-copper-plated. For manual welding use a wire chopped into pieces with a length of 360 to 400 mm. It is supplied to the consumer in coils weighing from 20 to 85 kg. All coils are equipped with labels indicating the manufacturer and technical parameters of the wire.
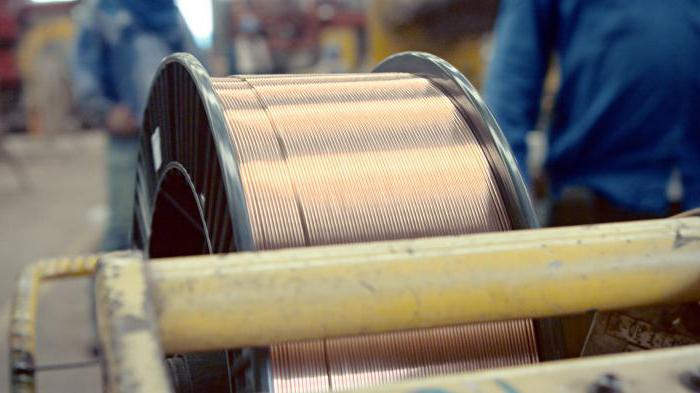
Plates are used for electroslag welding. Manual arc welding is performed using an electrode metal rod with a special coating called an electrode. The electrodes are divided depending on the thickness and composition of the applied layer and the quality of manufacture. In terms of thickness, a particularly thick, medium and thin coating is distinguished. Three groups in GOST are used to divide the electrodes depending on the accuracy of manufacture and the content of sulfur and phosphorus in the coating composition. The type of welding material coated with stabilizing, binding, deoxidizing, alloying components is indicated by the letters:
- coating with acid additives - A;
- The main classic option is B;
- coating with the addition of cellulose - C;
- mixed materials in the surface layer - P.
Non-consumable welded rods and electrodes for machine welding
To connect surfaces in shielding gases, special welding materials are used. The definition of such welding is given as a process using an electric arc between the electrode and the surface as a heat source. Round tungsten electrodes with a diameter of 5-10 mm supply electric current to the arc region. Pure tungsten is used as the material or additives of oxides of lanthanum, yttrium, and sodium dioxide are added. Tungsten itself cannot be replaced with cheaper metal, since it is the most refractory, with a high boiling point (5900 ยบ) and is used for welding with direct and alternating current.
Oxygen application
Oxygen is heavier than air, it contributes to the combustion of gases and vapors at high speed, while heat is released and a high melting point is reached. The interaction of compressed oxygen with fatty oils and lubricants leads to spontaneous ignition and explosion, therefore, work with oxygen cylinders is carried out in clean conditions, without the danger of such pollution. Storage of oxygen-type welding consumables is carried out in compliance with fire safety standards.
Oxygen for welding is technical, obtained from the atmosphere. The air is treated in special separation apparatus, carbonic impurities are removed, the final product is dried. Liquid oxygen for transportation and storage requires special containers with increased thermal insulation.
Use of acetylene
Acetylene is a compound of oxygen with hydrogen. This combustible gas is in a gaseous state at normal temperature. Colorless gas contains impurities of ammonia and hydrogen sulfide. The flammable component of the material is dangerous. Welding pressure of more than 1.5 kgf / cm 2 or accelerated heating up to 400 ยบ is enough for an explosion. Gas is produced by electric arc discharge, which contributes to the separation of liquid combustible components or the decomposition of calcium carbide by moisture.
Acetylene Gas Substitutes
Requirements for welding consumables allow the use of vapors of liquids and other gases. They are used if the heating temperature is twice the melting rate of the metal. Combustion of different types of gases requires a certain amount of oxygen entering the burner. Combustible substances instead of acetylene are used because of their cheapness and the possibility of widespread production. They are used in various fields of industry, but the use of substitutes is limited by their relatively low heating limit.
Wire and welding fluxes
For welding, an unknown wire of an unidentified grade is not used. The surface of the filler wire is smooth, free from rust, scale, grease. It is selected according to the melting index, which is lower than this characteristic for welded steels. One of the qualitative properties of the wire is its gradual melting without a sharp release of spray. As an exception, if there is no required wire, strips of cut metal from the same material that connects are used to weld brass, lead, copper, stainless steel.
When welding metals, such as aluminum, magnesium, copper, brass, cast iron, there is an active interaction of color casting with oxygen from the atmosphere or oxidizing flame. The reaction leads to the formation of oxides with a high melting point, which create a harmful film and hinder the transition of a substance on the surface to a liquid state. A welding material called flux, consisting of a paste or powder of the appropriate composition, is used to protect the surface of the molten mass. The material is boric acid, calcined borax. Fluxes are not used when welding alloy steels.
Safety water locks
Devices for protecting the rubber pipe and gas generator from the return of return fire from the burner are called a shutter. The requirements for welding consumables determine that the water shutter is designed in such a way that it does not ignite the oxygen or acetylene mass in the hole of the torch or torch. A water lock is always present in the equipment, this is a fire safety requirement that must be met.
The shutter is placed between the torch and the burner, according to the instructions it is in good condition and is periodically filled with water to the required level. This fixture is central to the welding equipment chain.
Cylinders for storage of compressed gases
Cylinders are made in the form of cylindrical steel vessels. The conical hole in the neck area is closed by a shut-off valve on the thread. The connection of the walls of the cylinder is made in a seamless way, the material is alloyed and carbon steel. External coloring makes it possible to recognize the type of gas placed inside. Oxygen is transported in blue vessels, acetylene cylinders are painted white, a yellow-green hue indicates the hydrogen content, the remaining combustible gases are placed in red containers.
On the top of the cylinder are written passport data of gas. The requirement for the storage of welding consumables prescribes to install cylinders vertically and fasten to the wall with a clamp. The valves of oxygen storage cylinders are made of brass, the use of steel is not allowed due to corrosion of materials in a gas environment. The cranes of acetylene gas cylinders are made of steel, it is forbidden to use copper and alloy with a copper content of more than 70%. Acetylene in interaction with copper forms an explosive mixture.
Gas reducers
Such a welding material as a reducer serves to relieve gas pressure from the cylinder and maintain the indicator at a constant level during the entire operating time, regardless of the decrease in the pressure of the substance in the cylinder. Reducers produce two-chamber and single-chamber. The former work more productively, maintain constant pressure and do not freeze with prolonged use of gas mixtures. To supply gas to the burner, rubber hoses with fabric gaskets are used, which undergo a preliminary test for strength and head pressure, as there are special documents. Hoses for oxygen and acetylene are used separately. To supply kerosene and gasoline use sleeves made of a material resistant to gasoline.
Material Requirements for Welding
For any type of welding, materials are used in accordance with strict standards, which clearly indicate the requirements for acceptance and control. All batches that went to the manufacture of welding materials in the factory are supplied with a certificate indicating the technical indicators:
- manufacturer's trademark
- symbols consisting of letters and numbers showing the brand and type;
- serial number of the party of melting and change;
- an indicator of the surface state of the electrode or wire;
- the chemical composition of the alloy indicating the percentage;
- mechanical characteristics of the weld;
- net weight.
The general requirements for all electrodes are steadily burning arc, well-formed seam. The metal of the obtained surfacing corresponds to a predetermined chemical composition, the core melts during operation evenly, without splashing and release of toxic substances. The wire contributes to the production of high-quality welding, slag is easily removed from the surface of the seam, the seam coating is durable. Electrodes retain technical parameters for a long time.
Every part is important for the welding process. The use of high-quality materials in the work plays an important role in the process of stable and durable metal joining.