Machining is a process during which the dimensions and configuration of workpieces and parts are changed. If we talk about metal products, then special cutting tools, such as cutters, broaches, drills, taps, mills, etc. are used for their processing. All operations are performed on metal-cutting machines according to the technological map. In this article we will find out what are the methods and types of machining of metals.
Processing methods
Machining is divided into two large groups. The first includes operations that occur without removing the metal. These include forging, stamping, pressing, rolling. This is called pressure or impact machining . It is used in order to give the necessary shape to the workpiece. For non-ferrous metals, forging is most often used, and for ferrous - stamping.
The second group includes operations during which part of the metal is removed from the workpiece. This is necessary to give it the necessary size. Such metal machining is called cutting and is performed using metal cutting machines. The most common processing methods are turning, drilling, coredrilling, grinding, milling, reaming, chiselling, planing and pulling.
What determines the type of processing
Making a metal part from a workpiece is a laborious and rather complicated process. It includes many different operations. One of them is metal machining. Before proceeding with it, they draw up a technological map and make a drawing of the finished part, indicating all the necessary sizes and accuracy classes. In some cases, a separate drawing is also prepared for intermediate operations.
In addition, there is roughing, semi-finishing and finishing machining of metal. For each of them, the calculation of cutting conditions and allowances is performed. The type of metal processing as a whole depends on the surface being machined, accuracy class, roughness parameters and part dimensions. For example, to obtain a hole according to the H11 quality, rough drilling is used with a drill, and for a semi-detailed deployment to accuracy class 3, you can use a reamer or a vertical drill. Next, we will study methods for machining metals in more detail.
Turning and drilling
Turning is performed on the machines of the turning group using cutters. The workpiece is attached to the spindle, which rotates at a given speed. And the cutter fixed in the caliper makes longitudinal-transverse movements. In new CNC machines, all these parameters are entered into the computer, and the device itself performs the necessary operation. In older models, for example, 16K20 longitudinal-transverse movements are performed manually. Turning of shaped, conical and cylindrical surfaces is possible on lathes.
Drilling is an operation that is performed to make holes. The main working tool is a drill. Typically, drilling does not provide a high accuracy class and is either rough or semi-finished. To obtain holes with a quality below H8, use deployment, reaming, boring and countersinking. In addition, after drilling can also perform cutting internal threads. Such metal machining is performed using taps and some types of cutters.
Milling and grinding
Milling is one of the most interesting methods of metal processing. This operation is performed using a wide variety of milling machines on milling machines. Distinguish between end, shaped, end and peripheral processing. Milling can be both rough and semi-finished, and fair. The smallest degree of accuracy obtained during finishing is 6. With the help of milling cutters, various keys, grooves, wells, hooks are machined, profiles are milled.
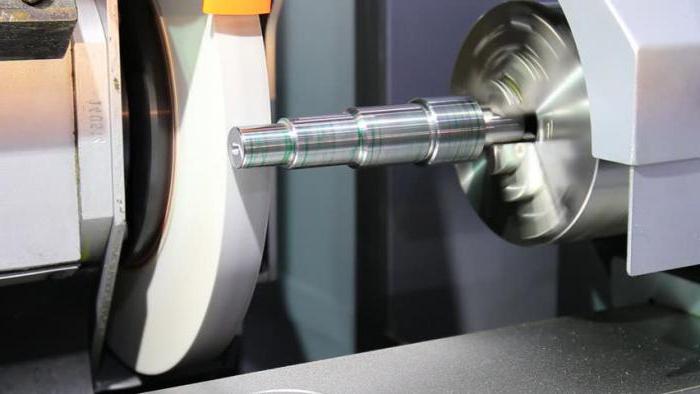
Grinding is a mechanical operation used to improve the quality of roughness, as well as to remove an excess layer of metal up to a micron. As a rule, this processing is the final stage in the manufacture of parts, which means that it is finishing. For cutting, abrasive wheels are used, on the surface of which there are a huge number of grains having different shapes of the cutting edge. With this treatment, the part becomes very hot. In order for the metal not to deform and not crack, use cutting fluid (SORZ). Non-ferrous metals are machined using diamond tools. This allows you to ensure the best quality of the workpiece.