Only if it is possible to count on the profitable work of the company, when the production lines and workshops at any given time are sufficiently supplied with raw materials, and the sales department is provided with finished products. It will be possible to avoid downtime if we correctly approach the planning of the warehouse at the enterprise. This issue is considered by several areas of logistics, the problem is studied in sufficient detail, so that with a thorough assessment of the issue, you can create a model warehouse that eliminates downtime. I must say that warehouse planning is inherent in all modern successful companies.
Features of warehouse planning
Careful warehouse planning involves taking into account all aspects of the premises. Particular attention is paid to the time intervals allotted to various operations. It is careful work over time that allows us to deliver all the necessary items to the warehouse through production planning, to ship goods from it not only efficiently, but also quite flexibly. In this case, all orders in the internal information system are taken into operation. With proper warehouse planning, shipping and taking positions takes quite a bit of time, due to which standards set in advance are observed.
The main goal pursued by the planning of a warehouse of spare parts, products, exclusive ceramics, and anything else is to turn the organization into a strong competitor in the market, which is achieved through effective activities that benefit the economic entity.
Where do we start?
Regardless of whether you plan to plan the warehouse of a wholesale company or need to work only with storage points for retail companies, the approach has common standards. It all starts with an assessment:
- turnover;
- level of service;
- cost of inventories;
- volume of purchased items.
To whom to entrust?
As logistics professionals say, it is better to entrust the planning team for the operational and utility rooms of warehouses to a team specially formed for this task. To do this, the personnel department forms a project team, and the document turnover department pays special attention to the work processes at the enterprise that are currently active and documents them.
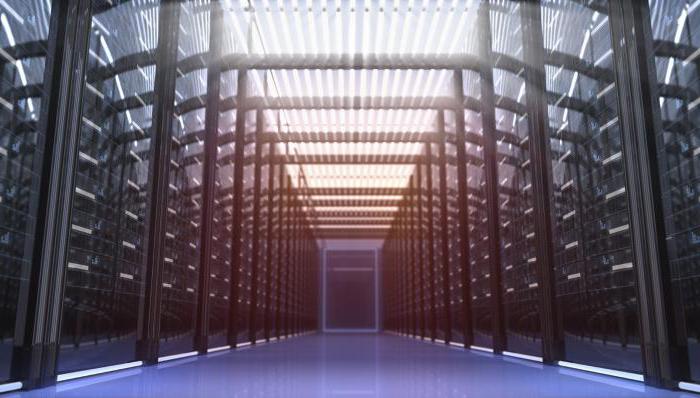
Quite often, aspects of fire safety when planning a warehouse force not only to revise plans regarding how to arrange offices inside, but even to completely reorganize the warehouse. In addition, such processing allows us to rationalize the room, to make it more consistent with the standards of our time and the particularities of the organization. It is a widespread practice when planning a warehouse at sawmills, factories, and other manufacturing enterprises to update equipment, machinery and equipment used in the storage system. Recently, the most frequent option is the installation of automated systems to reduce labor costs and reduce the likelihood of errors due to the human factor.
What to look for?
Starting planning the warehouse of finished goods, inventories or other resources, it is necessary to pay attention to a number of common important aspects. In particular, the workflow begins with an estimated calculation, but gradually the working group works out ever-smaller details, so that planning covers all the working moments.
It is necessary to thoroughly work on the planning of the warehouse, not losing sight of any any significant aspects. Moreover, the results should be such that at the end of the work they can be implemented without much work. For such planning to reflect in detail the real state of affairs in the company, it is necessary to have an up-to-date complete information base reflecting everything that happens inside it.
In turn and in detail
Warehouse planning is a thorough assessment and miscalculation of various options for organizing a room. Each of the projects proposed by the working group is evaluated by a selected expert and submitted to the management of the company for consideration. This helps to decide in favor of the most successful solution.
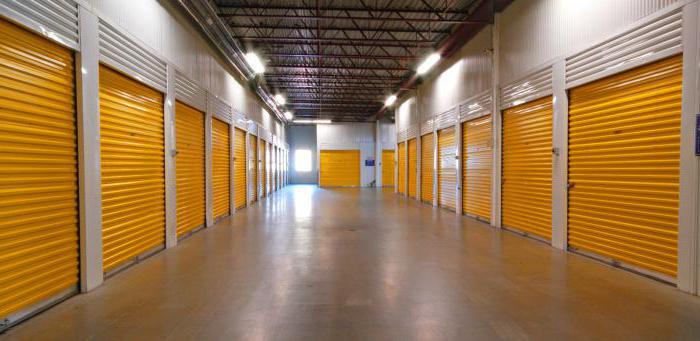
Planning the logistics process in the warehouse begins inside and gradually "moves" out. This means that first the working group studies the issues of inventory, equipment, technological solutions used within the warehouse, designs the movement of flows of inventories, and only then selects a building in which all this can be implemented with minimal cost and maximum efficiency. However, at the opening of a new building, the planning of the logistics process in the warehouse does not end. It is necessary to familiarize all working personnel with the developed information system, as well as to support the work process in real time. This means that several responsible specialists are selected from the working group of designers. Their task will be to control operations within the warehouse, measure quantitative performance indicators and develop options for improving the completed project, and in the future, a complete reorganization taking into account changing conditions.
Project: what and how?
Warehouse planning always involves a detailed study of the project, which includes:
- statement of purpose;
- analytical activity;
- development of a plan;
- implementation of the plan;
- working start.
Warehouse planning: everything is interconnected
The planning process is usually divided into several stages, but take into account the relationship between them. This means that the steps are not sequential, but parallel. So, at one point in time, the working group deals with the storage, moving inventory, the choice of premises and technologies, machines. At the same time, phasing is needed to achieve a balance between these aspects.
All components are interconnected. Keeping this in mind when planning a warehouse, competent specialists always control how the change in one aspect is reflected in others. The most effective approach is considered iterative, when a cycle of sequential actions is formed that is repeated each time as soon as at least one indicator changes.
Planning: what happens?
Work begins with preliminary planning, during which an approximate model is created. It is developed, focusing on budget estimates, the direction of the project. The data known at this stage allows us to formulate decisions on which subsequent actions are based. But the further you go, the more accurate the information you need to use.
The next stage is forecasting the amount of resources necessary for the correct operation of the enterprise. To do this, you need to have a budget estimate and have a fairly accurate idea of โโthe direction of the project. After that, you can begin detailed planning.
In detail and in details
When the working group reaches the step of detailed planning, according to the standards adopted in logic, it works with the following stages:
- selection of a place for a warehouse;
- planning of internal and external territories;
- study of the premises inside;
- analysis of the need for equipment, inventory;
- forecasting the capacity of personnel, warehouses;
- planning of individual operations.
How to miss nothing
It is important for the working group to control the movement within the planned warehouse of information and materials. One of the reliable ways to not lose any attention is to document all business processes, as well as simulate information flows and all processes within an enterprise. Additionally, functional descriptions can be worked out. This is most effective when using specialized databases.
At the same time, it is not recommended to start work from a bay-flank. According to professionals, it is first necessary to draw up a business plan for at least five years, but many world-class scientists agree that for a more or less stable company, the plan should cover the next decade. At the same time, it is necessary not only to take into account existing trends, but also to forecast a change in demand, the direction of improvement of the enterprise.
Spend: a lot or a little?
In most cases, warehouse planning takes up quite a bit of finance - not more than 15% of all costs associated with creating a new warehouse, but usually even less. But this is not a reason to underestimate him! It must be remembered that the preliminary planning stage is the time when the working team collects the largest possible amount of data. If it is not possible to accumulate the required amount of information, this will soon lead to a slowdown in work and an increase in costs, and also reduce the efficiency of the work of the group responsible for planning.
Warehouses are different
Speaking about the planning of storage facilities, it should be noted that these may differ significantly from each other. It depends on a number of factors. Trading enterprises, for example, have different levels of technical equipment, differ in organizational features and approach in the field of technology. This means that such premises are planned in different ways, that is, it will be wise to introduce classification into groups.
The main criteria:
- position regarding material flows ;
- functions assigned to the warehouse;
- assortment of positions;
- technical features;
- mechanization;
- number of floors;
- organizational management forms;
- transport.
Theoretical aspects
When planning, the working group creates such a project in which, with the exact implementation, the goods are in the best accessibility with respect to the consumer (buyer). At the same time, the plan is divided into two parts: sites on which reserves are stored, as well as sites designated for other purposes. It is believed that the most rational ratio of these areas is 2: 1, that is, the areas used for storage should be twice as large as those intended for auxiliary tasks.
When planning warehouses, they try to apply only the most rational methods of stacking, stocking, while positioning relative to each other so that there is no other influence and spoilage due to undesirable proximity. Close to each other, they try to place such goods for the movement of which you can use similar equipment.
General warehouse
That it can be described as the most common type of warehouses in the trading companies of our country (and not only). In this warehouse there are areas:
- production, where work operations are mainly performed;
- auxiliary, used for the maintenance of containers, pallets, containers;
- technical, where various devices, communications are installed. This also includes pantries, places of work of repairmen;
- administrative, household.
The features of the technological process, of course, greatly affect what the structure and layout of the storage area will be. Already at the design stage, the working group forms a complete list of the premises necessary for a particular warehouse, and also displays a proportional ratio of the areas to each other. At the same time, they strive to organize a continuous workflow, divided into flows that do not interfere with each other.
Warehouse: how to choose?
Choosing a room, many solve the problem quite simply: they estimate what area is needed, rent a suitable building. Rarely do companies seriously consider the future, especially small ones. But you need to understand: the interests of the company can change rapidly.
In recent years, there are more and more opportunities to cover sales markets that were not yet available a year or a couple of years ago, but along with this, competition has increased and working conditions have changed. These aspects have an impact on the rental industry. Therefore, a company that does not want to spend money in vain should analyze the future and only then make a decision in favor of a specific option.
Question Features
The first thing that is worthy of attention in this matter is the geographical location of the area of โโinterest. You will probably have to transport positions between warehouses if the company has several buildings, and these costs must be taken into account in advance. The more expensive the logistics cost, the higher the company will have to make a price tag, which ultimately can lead to the potential buyer going to a competitor. This is an incentive to reduce logistics costs.
But the situation with production warehouses is a little simpler. Typically, the company equips all warehouses on the territory of the plant, factory, which reduces the cost of money and time for transportation of positions. But the problem remains the selection of the optimal size. The most difficult task is planning distribution, supply warehouses. In any of the options, the working group predicts the costs associated with the considered opportunity, the company's revenues, calculates the ratio between them, allowing us to understand how this warehouse will be beneficial for the enterprise.
What will you have to spend money on?
First of all, they estimate the costs associated with transport. These investments are considered initial, this includes work on the creation, repair of roads, the purchase of vehicles, the construction of facilities for downtime, and car repair. In addition to this category include expenses associated with the sending, delivery of positions.
Another cost item associated with warehouse planning and translating the plan into reality is construction itself. Operating costs are also predicted in advance. This group of investments includes money spent on equipment. Do not forget about repairs, utility bills, wages. An assessment of these expenses should be prepared already at the planning stage.
More is better. Or not?
In general, a large warehouse is more profitable than a small one. It is customary to estimate the cost of a warehouse specifically: per ton of stored goods. Since the value is the smaller, the larger the room, it can be assumed that large warehouses are always preferable to small ones. At the same time, combining several small storage facilities located in different places in the companyโs possession into one large warehouse will provoke an increase in transportation costs, as delivery will become less profitable. But the presence of small warehouses is a step towards the buyer, since transportation costs are reduced, delivery time is reduced. On the other hand, the costs associated with the construction of facilities and their use (communications, personnel) are becoming more.
How to find a middle ground? Experts recommend evaluating the following aspects:
- density of competition;
- proximity to the buyer;
- proximity to suppliers of raw materials;
- living standards in the region;
- the ability to equip warehouses with staff;
- planned salary level;
- transport capacities;
- taxation;
- profit.
Additionally, they analyze whether the potential warehouse will be located near the railway, a large city, specify the cost of land, the difficulty of obtaining permits. A careful analysis of these factors helps to identify which option is more profitable: the creation of one large warehouse or several small ones.