Locksmith activities aimed at ensuring the smoothness of the surfaces of various materials represent a whole group of operations. These include common grinding, sawing, cutting and polishing techniques. Combining these methods of finishing surfaces is the use of abrasives with varying degrees and configuration of grit. In many ways it is similar to them, but scrubbing also has fundamental differences. This is a technique that allows you to obtain a smooth workpiece surface with high accuracy, which in the future will allow the master to ensure its tight coupling with other materials.
Technology Overview
The operation is most often used in relation to metal, but in some cases plastic and wooden surfaces are treated with similar methods. The essence of the technology is the elimination of pronounced bulges on the product. That is, with the help of a special tool grinding of irregularities is provided. To understand the degree of accuracy, it is worth noting that the height of the removed layer is calculated in microns. From an operational management point of view, scraping is a mechanical manual but not automated process. It uses bench tools, but machines and easel mechanisms do not yet have widespread use in this area. The peculiarity of the method is that it is also used in working with non-standard rounded surfaces, where radial slope accounting is required. For example, it can be curved and cylindrical products.
Preparing for Scraping
The use of scraping is due to the tasks of obtaining a highly precise surface in terms of smoothness. Therefore, the use of a specialized tool to achieve such a result when working with materials having a rough surface does not justify itself. Accordingly, the workpieces initially go through the stages of initial cleaning, as well as grinding and even polishing. The demand for recent operations is determined by the parameters with which specific locksmithing works are implemented and, in particular, scraping. Experienced craftsmen practice the use of calibration parts. These are blanks that are exemplary for the resulting product. Also at this stage, auxiliary equipment should be ready, with which the operator will carry out individual technological steps. For example, special primer oil or paint may be used.
Scraping technique
After completing the preparatory processing steps, the first thing to do is apply special paint to the work surface. Its task is to identify the lapping pattern, as well as to identify the most prominent areas on the surface. Sometimes large areas are zoned into separate sections, depending on the complexity of their bringing to the desired state. One way or another, according to the formed pattern, scraping is performed. This means that the processing is not carried out over a continuous area, but in a sense pointwise. The efficiency and quality of the resulting slice is determined by the frequency with which stripping is performed. After the planned volume of the cut was completed, the master makes another coating of the surface with paint, which again reveals the bulges and irregularities. Thus, quality control of scraping is performed. By the way, the operation cycle can be repeated several times depending on how much each session brings the surface of the workpiece closer to the sample.
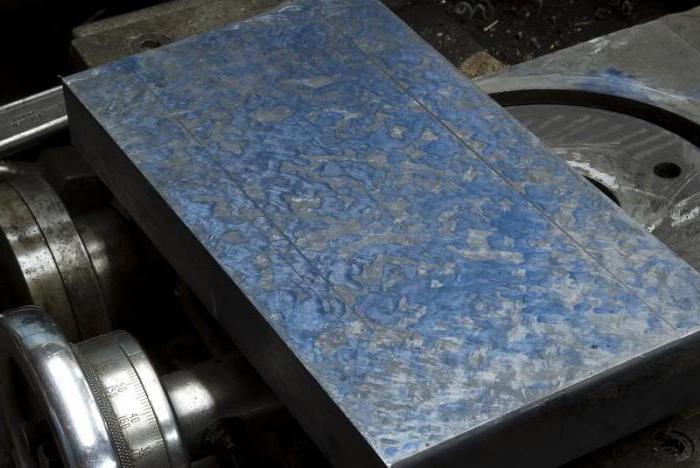
Technical Parameters of Scraping
And in the case of processing flat surfaces, and in fine-tuning curved products, the technology allows to obtain smoothness with an allowance for roughness of the order of 0.002 mm with a length of 1000 mm. For example, a site measuring 25 x 25 mm 2 may have up to 30 exit-treated spots. The number of spots also determines the level of accuracy of scraping. Thin are considered surfaces on which over 22 spots are present. Conversely, a product with no more than 6 spots on its surface will be considered rough. Again, the number of remaining islets treated with paint will be calculated over an area of ββ25 x 25 mm 2 . Depending on this parameter, types of scraping are also determined - between a thin and rough cut, precise and final refinements are also distinguished. Which result should be obtained in a particular case depends on the technical task. A thin cut with 30 spots is not always required. Rough processing is sometimes sufficient to fulfill the tightness requirements. But coarse scraping cannot be compared with a similar characteristic when grinding - in both cases we are talking about different orders of height of the remaining bulges.
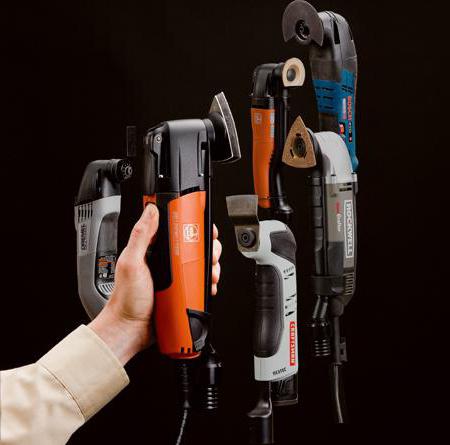
Tool used
In the classic version, the scraper is a metal rod provided with cutting edges. An important feature of the device is a base made of tool carbon steel. Thanks to such alloys, a metalwork scraper works effectively with most metal products. Also, some models can be equipped with special nozzle plates that differ in different properties - accordingly, the equipment is selected for specific tasks.
It has already been noted that mainly scrapping is carried out with a hand tool. This method allows you to get a high-precision quality result, but it has a minus - this operation is time-consuming, requires considerable physical effort. Therefore, if special quality requirements are not provided, use pneumatic and electric gauge machines. Mechanized scraping of parts due to the inability to adjust the pressure exerted on the surface does not always provide accurate processing, but it compares favorably with the manual method by the speed of operations.
Pros and Cons of Technology
The main drawback of scraping is the cost and complexity of the process. This is one of the most troublesome locksmith operations, which is resorted to only in special cases. Moreover, even manual equipment, involving the use of a simple tool for the device, will be expensive because of the need to use consumables in the form of scraper paint. The advantages, which are still many in this processing method, include obtaining a high-precision cut. Other metalwork cannot provide a similar effect (with the exception of technological equipment for grinding and polishing). But in this case too, the same drawbacks will occur - grinding machines with increased productivity operate on a different principle and are not always able to achieve a similar quality level of cut. And this is not to mention the cost of the equipment itself, which at a price can exceed pneumatic and electric scrapers.
Where is the metalwork scraper used?
Practice shows that scraping in the professional sphere of performing locksmithing occupies about 20% of all operations. However, the niche in which products manufactured in this way are used is rather limited. Basically, scrapers are used in the manufacturing processes of parts for machine tools, machines, industrial equipment, etc. It is important not to forget that scraping is a way of obtaining surfaces that are highly accurate in terms of smoothness. Moreover, the surfaces themselves can be curved. For example, high-quality bearings with optimal radial planes can only be obtained in this way.
Conclusion
The difficulty of bringing metal surfaces to a state in which there will be no irregularities even visible to the eye has also determined the high responsibility of the performer himself. The fact is that the highest-quality operation (scraping) involves manual revision, which directly depends on the skills of the master. An experienced locksmith must take into account a lot of nuances in the process. These include the selection of scraper paint, and the use of one or another tool stroke frequency, and other subtleties that will determine the merits of the final result.