Firing technologies for industrial and building materials are used in various industries. Thin operations of thermal processing of materials require the use of special structural solutions. One of them is a fluidized bed furnace (KS), characterized by a complex design and multifunctionality.
Scopes and purpose of the equipment
The peculiarity of the use of furnaces of this type is due to the specifics of utilization, processing and production of industrial raw materials. As the target material, magnesite, brucite, zinc concentrates, serpentinite, slimes of magnesium production, oxide-chloride elements, etc. can be used. For example, an expanded clay bed furnace is characterized by the fact that it performs several operations at once to obtain the desired product - in particular, firing, drying and cooling procedures are being implemented. A distinctive characteristic of KS furnaces is the process safety in terms of environmental protection.
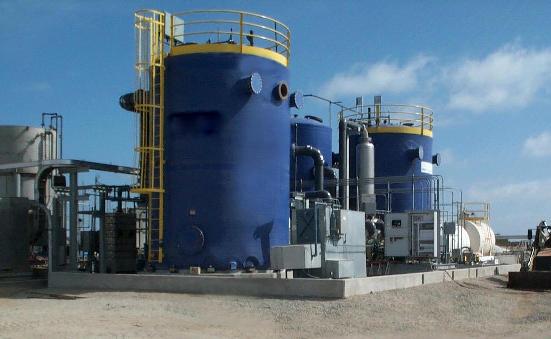
After disposal of the material, its neutralization is achieved without dangerous consequences for the local environmental background. Also produced vapors mainly consist of carbon dioxide and water condensate. As for the directions of operation, the KS furnaces are used in the production infrastructure of chemical, metallurgical, construction and other enterprises. Also at the points of engineering and communication services for gas distribution networks there are similar furnaces.
Technical device of KS furnaces
For firing and disposal of most raw materials and waste products, designs are used, which are based on a cylindrical vertical shaft. Some models have a variable cross section. The average dimensions are 9-12 m in height and 6-8 m in diameter. The shaft itself is welded on steel sheets, the thickness of which reaches 12 mm. A typical lining with small fireclay bricks is used inside the structure. The working base of the fluidized bed furnace is formed by an air distribution hearth (feed panel) with an air duct.
Depending on the specific project, this part can be performed heat-resistant, wirelessly and ensuring uniform air flow throughout the interior of the structure. In addition, a typical system of KS furnaces includes loading openings, nozzles, gas exhaust channels, auxiliary service platforms, cooling devices and other components.
Fluidized bed zone arrangement
In this part of the design, the main working procedures and reactions go through. Here is the hearth, chamber and drain thresholds. The last two devices in order to increase the residence time of the boot material are located on different sides of the structure. The prechamber usually has an area of the order of 15-20 m 2 . In the same area is the bunker for the charge. Models of an industrial fluidized bed kiln are designed for the simultaneous content of raw materials with a daily supply. The movement of material between different functional blocks is provided by belt feeders. Management of this mechanics can be mechanical and automated. The latest equipment allows you to control the boot process remotely using the remote control.
The principle of operation of the unit
By itself, the fluidized bed forms an air buffer zone of increased thermal stress, in which thermal reactions with soaring solid particles can be carried out. The retention of granular material in the air is achieved due to the ascending gas flows supported by the nozzles. During operation, the liquid and solid phases of the fluidized bed are interleaved. For example, the upper level is similar to the behavior of fluids that are in a calm state. Particles with a harder structure sink down the fluidized bed furnaces.
The principle of operation of the unit is based on several operations that can be performed sequentially - these are the stages of heating, drying and burning. At the same time, the procedure for distillation of volatile substances, as well as the removal of carbon residues, can be performed. The most demanding operation in terms of resource costs is heating and drying. On average, they are performed at temperatures of 100-200 ° C. The combustion process requires maintaining the temperature in the flare at the level of 500-1050 ° C, but by this moment the furnace is already at its optimum working state after heating.
Fluidized bed furnace loading
Loading and access to the boiling zone can be carried out in three ways, depending on the design:
- Directly inside the boiling zone. The feed is carried out by the capacity of dual augers, which are located below the discharge threshold. This method is beneficial by reducing dust formation during the boot process, but requires more space and energy.
- Outside on the surface of the layer. A rare loading pattern that is used only in high power furnaces.
- Through the prechamber. The method is used in domestic fluidized-bed furnaces, providing advantages in the form of a uniform and continuous supply of the target material into the chamber.
In principle, the feeding process is quite simple, but in conditions of large-scale production at a high loading speed, requirements for operator temperature control may increase. For example, there are problems of reducing the heating rate, because of which the supply of raw materials to the hopper on automatic control systems also stops.
Temperature condition of the KS furnace
Each type of concentrate requires its own heat treatment mode. Often, suitable firing parameters are selected empirically, but in accordance with the standards should also take into account the chemical and mineralogical properties of the raw material. So, for concentrates with a high content of lead, iron and silica, moderate temperatures are used. This minimizes unwanted silicate formation and sintering of the material. The average modes of such processing are in the range of 900-1000 ° C. Comte
the role of the temperature of the fluidized bed furnace is usually carried out by thermocouples, which are fixed at the points of the working zone. In each layer, a slight deviation of the order of 15-20 ° C is allowed. Manual temperature control also provides for the operation of water cooling - this method is often used in foreign enterprises.
Fugitive parameters of the KS furnace
It has already been noted that air flows play one of the key roles in the work process of this equipment. At a minimum, they carry out two functions: maintaining the optimal pseudo-liquid state of the feed and oxidizing the sulfides during firing. Providing sufficient conditions for the flow of the main working processes is possible only with the support of the corresponding pressure of the air flows. For example, a pressure of 15-16 kPa at a flow rate of 10-12 m / s will be enough to support a 100-cm fluidized bed of the furnace.
The principle of operation of units with a draft device allows for vertical air circulation, but it is important to consider that exceeding the pressure level in this circulation circuit can lead to blowing of the material outside the boiling zone.
Conclusion of products of combustion
To exhaust the exhaust gas, a system of cylindrical nozzles is used, which, by the principle of drawing, cover the entire boiling zone. And again, the volumes of absolute burning output are not comparable with those of other industrial kilns. This is due to several stages of post-processing. So, there are stages of secondary processing of the combustible organic part of the charge with the burning of carbon residues of the fluidized bed in the furnace. The process continues the calcination of the ash sediment at temperatures of 700-1050 ° C. Before the mechanics unload the waste, gas deodorization occurs, which also determines the reliability of the KS furnaces. And only after that the service personnel takes out the remains of unburned ash outside the work site.
Unit design calculation
When calculating KS furnaces, several parameters are used, among which the properties and characteristics of the target raw material, as well as the requirements for the volumes of exhaust gas with the formation of dust fractions. Based on these data, performance indicators of functional units of the structure are also determined. In industrial systems, the calculation of a fluidized bed furnace is usually done on the basis of a standard production volume of 50 thousand m 3 / year, for which the following operating parameters will be relevant:
- The density of the raw material fraction is 540 kg / m.
- The temperature regime in the heat treatment zone is 350 ° C.
- The temperature in the firing chamber is 1105 ° .
- The temperature of the production raw is 10 ° C.
- The air temperature is 16 ° C.
- The utilization rate of the unit is 0.9.
- Losses during the calcination process - 12%.
Pros and cons of KS furnaces
Aggregates with fluidized bed support have many advantages due to high performance, functionality and flexibility in structural adjustment. Especially the latest models are conveniently equipped with modular layout options, which allows integrating the furnace station into the infrastructure of enterprises with individual design at minimal cost. As for the operation process itself, the advantages of firing in fluidized bed furnaces are low fuel consumption, the possibility of using small fractions (0.6-2 mm) and technical reliability. The high quality of the finished product of processing is also noted, but this applies only to certain materials.
If we talk about the disadvantages of KS furnaces, the main thing will be a high coefficient of dust removal of the charge. The dust carried away from the heating units makes up 25% of the total output. This effect is explained by the activity of exhaust gases, which carry fine particles. In large enterprises, dust collectors are fought with cyclones installed behind furnace structures. On the return circulation channels, these units return dust to the furnace or ash pan.
Conclusion
In Russia, equipment for industrial firing has long been in high demand, and today there is considerable potential for the design and manufacture of modern KS furnaces. In particular, the TAGMET enterprise specializes in the manufacture of limestone calcining facilities. Integrated development offers NPP Calcite. In particular, the employees of this enterprise apply new technologies for processing fine-grained material, which expands the range of applications of fluidized bed furnaces.
Envirotherm, the manufacturer of industrial equipment, also offers a number of innovative solutions. Without loss in volumes and speed of release, the units of this company provide multi-stage gas purification and efficient combustion of fluidized bed sediments. Ultimately, environmental friendliness of all derivative components with air is achieved. Also, many enterprises offer comprehensive modernization of existing but outdated KS furnaces with the possibility of partial replacement of working modules.