Metallurgical production is simply unthinkable without the use of coke, which provides energy for the melting of iron ore in the mine blast furnace. However, the coke production process itself is quite laborious and lengthy. To create it, special industrial units under the name "coke oven batteries" are being built. Their device, purpose and characteristic features will be discussed in this article.
Definition
Coke oven batteries are a whole metallurgical complex whose main purpose is to produce coke in the required volume for its subsequent transportation to blast furnaces. These production facilities can vary in size among themselves, but in any case their size is very impressive.
Design
The device of coke oven batteries is as follows. The main elements of these furnaces are the so-called coking chambers. It is in them that the process of laying raw materials takes place. There are more than a dozen coking chambers in the furnace. Also, the heating gaps in which the combustion of fuel proceeds can be considered the most important elements of the battery. The approximate linear dimensions of the coking chamber are as follows:
- Length - from 12 to 16 meters.
- Height - 4-5 meters.
- Width - 400-450 millimeters.
In general, the complex, thanks to which coke oven batteries have the ability to work continuously for a long period of time, includes the following components:
- The receiving hopper, which receives raw coal.
- Coal mixing and crushing department.
- Distribution tower.
- Loading trolley.
- Coking chamber.
- Coke ejector.
- Extinguishing car.
- Extinguishing tower.
- The platform onto which the cooled finished product is unloaded.
The very same furnace for the production of coke in general has in its composition:
- Chambers for loading coal charge.
- Heating wall with heating duct system.
- Gas distribution system and air supply.
- Regenerator for heating air and exhaust gas.
- Shutoff valves and mechanisms.
Classification
Coke oven batteries, depending on the operating mode, are periodic and continuous. These batteries can be heated:
- Exclusively blast furnace gas.
- Only coke oven gas.
- A mixture of blast furnace and coke oven gas.
A battery heating circuit may include:
- The cross over channel thanks to which gases have an opportunity to get between piers.
- Pair channel for recirculation.
Heating gas for the battery is supplied to it in two versions:
- On the side, when coke oven gas flows through the cornea (gas distribution channel), and air and blast furnace gas flows through the hearth channels of the regenerator.
- Below on a special air distribution network.
A few words about the regenerator
This special heat exchange device allows the coolant to come into contact with the clearly marked surfaces of the coke oven. It is important to note that a hot heat carrier heats a cold wall and nozzle, and after that they, in turn, transfer heat to a cold heat carrier.
There are other types of heat exchangers, which are called "recuperators". In them, cold and hot fluids carry out an exchange of energy between themselves through a wall specially constructed between them. In this case, first, hot gas flows go down, and then the flap valves are triggered, so that a cold air stream starts to rise from the bottom up.
Methods of fuel economy in coke production
The coking process itself is quite energy-intensive, which is caused by the consumption of a very large amount of fuel. Therefore, to reduce the consumption of its consumption, the following methods are used:
- Use the technology of dry quenching of coke. Thanks to it, the thermal energy of the product is spent on heating steam or water. In particular, about 1 GJ of heat in the form of steam is obtained from one ton of finished coke.
- Modernization of the used regenerators for maximum heat production from combustion products. So, for example, it is quite possible to increase the heating area of the nozzle.
- Calculation of the optimal time interval between valve switching. It goes without saying that the more often they switch, then ultimately this will make it possible to reduce the volume of regenerators and heat loss in them. At the same time, it is worth noting that too frequent actuation of the valves will inevitably lead to their rapid failure and additional load on all adjacent nodes and parts.
- The charge heating and dry quenching of coke is carried out simultaneously.
Technological process
Coke production is very difficult. Therefore, to understand how this works in real conditions, it is worth knowing the technological cycle as much as possible.
The coke plant always starts with a coal tower. It is in it that the raw material enters. At the bottom of the tower there are special shutters. Through them, the coal is transported to the receiving hoppers of the coal loading machine. In order to exclude the possibility of coal hanging inside the tower, compressed air is supplied over its entire height, which is supplied by intermittent pulses and guarantees the collapse of the charge adhering to the tower walls. The tower should certainly be filled at least two-thirds of its volume.
The coal loading machine is filled either by volume or by weight. The process of filling is controlled by scales. Coal is fed into the furnace immediately after the delivery of the finished coke. In this case, the charge is fed through the top. At the moment of loading the coke oven, the person responsible for this - the hatchway - turns on the furnace itself in the gas collector and activates the injection. The entire boot process takes three to six minutes.
After that, the furnace is carefully sealed, and the process of heating the mixture begins. The technology for the production of coke in coke oven batteries provides for the following temperature processes:
- At 100-110 ° C, coal is dried.
- In the range 110 ° - 200 ° , hygroscopic and colloidal-bound moisture, occluded gases are released.
- At 200 ° - 300 ° , thermal preparation proceeds, which is accompanied by the formation of gaseous products of thermal degradation and the elimination of thermally unstable oxygen-containing groups.
- 300-500 ° - temperature range at which a plastic state occurs. Gas and steam are liberated intensively, and a liquid phase is formed.
- 550-800 ° - medium temperature coking. The synthesis is intensifying.
- 900-1100 ° - high-temperature coking.
Shipment of coke from the furnace
A coke oven battery, the principle of operation of which is described in this article, requires special preparation before issuing finished products from it. At least twenty minutes before the start of the dispensing, the furnace is necessarily cut off from the gas collector and communicates with the atmosphere by opening the riser lid.
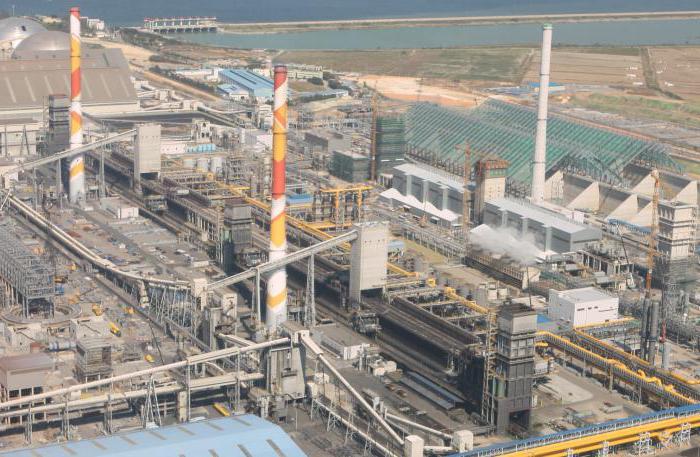
After that, the door of the furnace is removed and the coconut is pushed out of the chamber into the quencher using a special rod. Moreover, if for some reason there is a delay in the planned issuance of coke for more than ten minutes, then the doors should be installed back into place. It is strictly forbidden to open the riser caps prematurely, as this can cause serious collapse of the lining inside the battery. In addition, the oven doors must be cleaned of graphite and resin before and after the process of issuing finished products. Extinguishing coke in a special carriage is a mandatory procedure, because without this operation the finished coke can again ignite.
Calculation of coke oven batteries provides that furnaces must have a working and repair period. During the working cycle, coke is dispensed, and during the repair cycle, all units and equipment are serviced, cleaned, and so on.
Essence
At the initial stage of coking, coal is dried, all adsorbed gases are removed from it and decomposition starts. At the moment of transition of coal to a plastic state, sintering begins - a process that is crucial for the entire coking cycle. At the third stage, the semi-coke undergoes calcination and hardening. It is the viscous mass that builds up resistance to the movement of gases on their way into the gas collector, due to which coking pressure is formed, which in practice is compensated by the shrinkage of the already formed coke.
Conservation
"Why can not stop coke oven batteries?" - this is the very question you can often hear from the lips of a person who is far from the intricacies and nuances of coke production. The thing is that these units are oriented to work under certain conditions (high temperature, abrasive wear, etc.) and in case of an unscheduled stop without proper preparation, these furnaces are able to lose their internal masonry, which simply collapses. However, in practice, sometimes it is necessary to suspend the operation of the coke oven battery and perform certain conservation measures. How it works - to describe for too long, you only need to indicate that there is the so-called "cool" and "hot" conservation. Which option to choose from is decided directly by the head of the enterprise, depending on the current situation and the reasons for the suspension of the unit.