The gas transportation infrastructure, in addition to the pipeline network, contains many technological stations that perform various monitoring and regulation tasks. Most of them are installed on trunk lines, but less critical nodes are also found in branch circuits with a small diameter. One of the most common objects of this type is the ShRP gas regulator. The decoding of this station can be represented as follows: “Cabinet Regulatory Point”.
Node assignment
Devices are more often used as part of central communication and engineering networks. In fact, installation is carried out wherever a physical pumped fluid can be serviced under pressure. Gas pipeline and distribution networks, in particular, are targets for the application of ShRP. What is this in terms of functionality? This is a regulator, which in the basic version is used to automatically maintain pressure within specified limits. But this is not the only task of such devices. Models expanded in functionality also control gas filtration, can turn off the flow, etc.
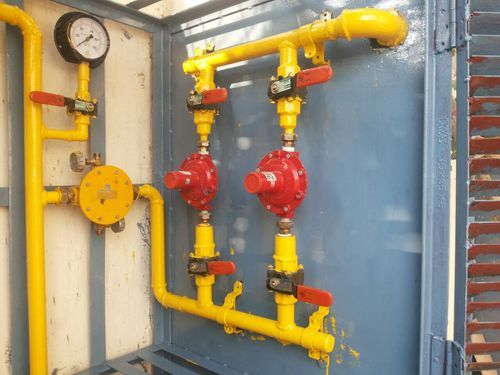
It is important to emphasize the differences between ShRP and pressure gauges. Conventional pressure meters only record its level and in technologically advanced versions they can send signals about an excess or decrease in the indicator to the control panel. In turn, the regulation point fully automates the gas supply process within a specific section. In some stations, a metering unit is also used, which records input and output data on the volume of gas mixture consumption. This set of tasks already depends on the specific device and the configuration of the ShRP.
ShRP device
The station is a collapsible metal cabinet, the basis of which is formed by a reduction line with the necessary valves. The simplest models have only one control loop, provided with a two-stage pressure regulator and a ball-type valve to completely stop the flow of the gas mixture. Working equipment in the cabinet is fastened with special brackets and clamping mechanisms. But the practice of using multifunctional ShRP designs is also practiced. This type of cabinet control unit may include the following components:
- Locking devices.
- Filtration unit.
- Pressure regulator.
- Safety relief and shutoff valves.
- Solenoid valve for regulating gas in normally closed and open circuits.
- Equipment for the bypass circuit with disconnecting devices.
- A group of pressure gauges (installed near the filter, at the inlet and outlet).
It is worth noting that all the working equipment with the cabinet body is made of durable materials that are resistant to various kinds of external loads. As a rule, these are metal products with anti-corrosion coatings that can withstand temperatures in the range from -40 ° C to 80 ° C on average. Can also be applied electrochemical cathodic protection ShRP. What it is? Such devices are used for added protection against corrosion. But when using this insulation with conductors, it is necessary to take into account compatibility with the electrical engineering of the regulation module itself.
The working process
Technological operations are performed as gas passes through the serviced circuit. The operation of individual nodes will be influenced by parameters such as pressure, temperature, density and velocity of the medium. The gas supply in the ShRP system starts from the ball valve towards the regulator. The latter can be cleaned using an integrated filter, after which it reduces the gas pressure. Typically, the operation of the device is to increase operational performance. So, if in a high-pressure gas pipeline from 0.6 to 1.2 MPa, the value of 1 MPa is taken as the optimal operating indicator, then a regulation unit will automatically work when lowering it. Under normal conditions, without any effect on the supply line, the pressure naturally decreases. That is, from time to time the ShRP will connect and raise the input pressure indicators to the optimum level, which, by the way, is adjusted by the operator when the equipment is put into operation.
Installation of construction
Before installation on the prepared site, the removable panel of the cabinet is removed, and the mounting (bearing) part of the housing wall is fixed with complete screws or bolts. At the points of entry and exit to the nozzles are connected to the contours of the pipeline - the outlet and inlet segments. The regulator is installed either by welding, or union nuts. Experts recommend, in principle, referring to those connection methods on the basis of which the construction of the gas pipeline and adjacent structures was carried out. This will allow during the maintenance process to save on tools and consumables when performing dismantling operations. But if possible, it is still worth giving up welding in favor of threaded joints. At the final stage, shut-off, control, measuring and protective equipment with connection to the failed communications is installed. Next, we begin to test the system.
ShRP connection leak test
Before setting up and operating directly, it is important to test the circuits for the quality of the connections made. This is done by filling the pipeline lines with air under pressure corresponding to the optimal load on a particular circuit. Standard pressure testing of high pressure gas pipelines can be done at 0.3 MPa. After the installation point of the regulator, a threaded fitting should be installed on the outlet pipe and a pressure test should begin. Both branch parts of the gas pipeline are painted together with the joints, after which the regulator is mounted on the union nut and the sealing air mixture is supplied to the circuit under operating pressure. Defective areas will be detected using the applied paint.
First ShRP launch
After successful crimping, it is necessary to verify the integrity of all the working bodies of the complex through visual inspection. The crane must be in a closed position. Before starting the gas pipeline with the ShRP, the following actions are performed:
- Using the fitting on the regulator, mount the adapter to install the control pressure gauge.
- Slowly open the tap and check the gas pressure indicator at the gas inlet pipe through a manometer.
- Remove the pressure gauge and plug the inlet with a plug.
After this procedure, when there is sufficient working pressure, the inlet valve opens. The trigger is cocked on the regulator, but so that the outlet pressure stabilizes gradually without jumps. A pressure gauge is again installed on one of the outlet pipes through a special adapter.
Maintenance Measures
Service is usually performed by personnel involved in the integrated management of the trunk line on which the ShRP is installed. In the process of this set of measures, the following actions are performed:
- Visual inspection of equipment. The external state of the structure is evaluated.
- Checking the tightness of the pipeline. The same crimping with a marker emulsion is used to detect leaks.
- ShRP bypass testing. What it is? This is one of the complete components that allows you to mount a backup (emergency) gas transportation path. He must always be in good condition and ready to work.
- Quality control of fasteners and mechanical joints.
- Performing cleaning of the surfaces of the functional parts of critical assemblies.
Based on the results of a comprehensive examination, an act can be drawn up with instructions or recommendations for repair measures.
Possible device malfunctions and repairs
The most common malfunctions of gas controllers include the following:
- Gas leak at connection points. If the joints were made with threaded fittings, then the nuts with bolts are tightened or the sealing materials are replaced. If the construction of the gas pipeline was carried out by means of a welding joint, then non-destructive testing cannot be dispensed with. This reveals internal voids and cracks that could leak.
- Filter clogging. Cartridges are usually used for cleaning, so in most cases it is enough to replace the filter membrane.
- Untimely actuation of the valve on the shutoff. There is probably mechanical damage, so a thorough visual inspection is carried out, after which the system is restarted. If the problem recurs, then the valve is changed.
Safety during operation
ShRP stations have strict restrictive measures aimed at maintaining fire protection rules. In particular, it is forbidden to use fire sources at gas transmission facilities, to interfere in the design of equipment without appropriate authority, to change the settings of working valves, etc. Particular attention is paid to shut-off and safety devices of ShRP. What it is? These are system components that trigger automatically when signs of a gas outage are detected. In such situations, it is necessary to find out the causes of the fuse tripping, and then take measures to restore the regular operation of the complex.
Conclusion
Regulatory and instrumentation systems as part of modern gas pipeline networks are characterized by a high degree of autonomy and independence from the operator. The same metering station sends information about gas consumption to the control panel, in which a whole range of decisions can be made based on the data received - from changing the supply volume to the redistribution of gas supply lines. Along with this, more and more emphasis is placed on the performance of mechanical operations. The regulation point is directly involved in the processes of stopping and starting gas transportation with the parameters that are currently needed.