Shell casting is also called shell casting. And abroad, this method of work is called Shell.
general information
In the modern industrial industry, many different casting methods are used. In addition to shell, casting is also used, as well as in metal molds and several other methods. A common advantage of such casting methods, when compared with working with sand forms, is that they make it possible to obtain more accurate final materials in their shapes and sizes as a result. In addition, the number of roughnesses on the surface of such products is reduced. In more rare cases, but still it happens that the need for subsequent machining after smelting is eliminated. In addition to everything, the use of casting in shell molds and other methods contributes to the fact that this process can be mechanized as much as possible, as a result of which its automation is increased. And this, of course, greatly increases the productivity of any industrial facility.
Shell casting
Speaking specifically about this method, it was first introduced in factories back in 1953. Currently, the method is used quite widely. It is by casting in shell molds, for example, that most of the parts for the Kirovets tractor are manufactured . All parts that are produced by this method are obtained the highest quality from steel or cast iron. By shell casting is meant a method by which the final result of the casting has a shape consisting of two sand-resin shells. Also, this method of manufacturing parts is used only in cases where it is necessary to create a part with small or medium sizes, but at the same time with high accuracy. Examples of the application of this casting method may be parts for engines or thin-walled casting.
The essence of the method
Using this method of operation, various parts can be obtained for fans, motors, pumps or textile machines. However, the maximum length of the product obtained cannot exceed 1 meter, and also it cannot be heavier than 200 kg.
The essence of casting in shell molds is based on certain properties of thermosetting resins, which are part of sand-resin mixtures. The advantage due to which such components are used is that these resins tend to harden quickly and irrevocably if they are treated with a temperature of 200-250 degrees Celsius.
The manufacture of shell molds
In order to make a mold for subsequent casting, it is necessary to have fine-grained quartz sand, which comes with the addition of thermosetting resin, which is its connecting element to obtain a full shell mold. These materials, in particular, the resin is selected due to the fact that when it passes a certain temperature barrier, it hardens. The manufacturing process is as follows. First, the resin is heated to 140-160 degrees Celsius. Under the influence of such an environment, it turns into a liquid adhesive mass, which completely envelops the form of quartz sand.
The scope of casting in shell molds is quite wide, and therefore the process of manufacturing molds is brought to automatic or automated.
After the mold is completely coated with resin, the temperature is increased to 200-250 degrees Celsius. This temperature threshold is quite enough for the adhesive mass to harden irreversibly and form. Further, when the casting process begins, that is, when the molten metal enters the mold, the temperature in it reaches about 600 degrees. This mode is sufficient so that the resin does not melt, but burns out, leaving pores on the form itself that facilitate the escape of gases.
Advantages and disadvantages of shell casting
Like any other production process, this one has its positive and negative qualities. If we compare this casting method, for example, with casting in ordinary sand forms, we can distinguish several of the following advantages:
- The first and rather significant difference is the accuracy class, which is 7-9. In addition, the surface finish of the obtained part is improved to 3-6. In addition, allowances are reduced that are allowed for subsequent machining of the obtained part after casting.
- One of the big pluses is a significant reduction in labor costs for the manufacture of castings.
- This casting method reduces the consumption of molding materials, as well as the amount of metal due to the fact that the size of the sprue channels is reduced.
- Significantly reduced the number of defective output.
However, there are also some disadvantages of shell casting. These include:
- The service life of the shell mold is 1 cast.
- The cost of the molding sand is quite high.
- High percentage of harmful gases.
Body forming process
The process of forming the body is carried out in six stages:
- The first step is the process of pouring the mixture onto the hot metal model, as well as the aging process, which lasts several tens of seconds until a thin strong crust forms around the part. Most often, models are made of cast iron, and they are heated to 230-315 degrees.
- After this, it is necessary to carry out an operation to remove excess molding sand. The thickness of the crust in the end should be from 10 to 20 mm. It depends on the time the mixture was on the model, as well as on temperature.
- After that, it is necessary to transfer the model plate together with the mold to the furnace, where they will remain until the curing process is completed. At the end of this procedure, the shell strength should be from 2.4 to 3.1 MPa.
- After removal from the furnace, the hardened shell is displaced from the stove. A special pusher is used for this procedure.
- After that, two or more models are fastened together by means of a clamp or by gluing. These molds can be used for casting in shell molds or simply stored. Shelf life is almost unlimited.
- Before starting the process of casting in the finished form, a shot is poured into them, which helps to prevent or destroy the mold during further pouring.
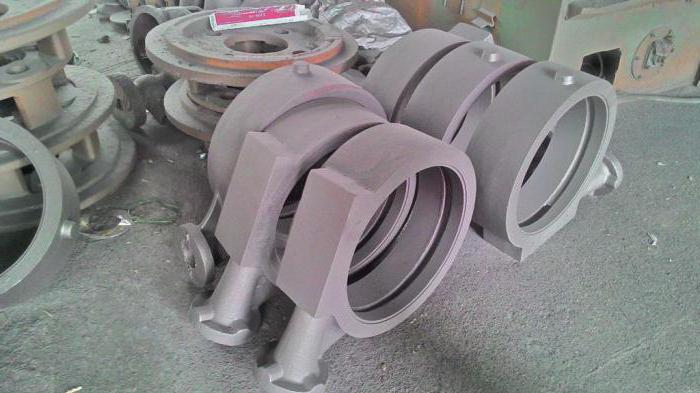
Cast Details
It is worth starting with the fact that the typical tolerances that are allowed in the manufacture of equipment can be 0.5 mm. The surface roughness is allowed in the range from 0.3 to 0.4 microns. Such limits are justified by the fact that fine-grained sand is used. It is also worth noting: the use of resin significantly contributes to the fact that the surface will be very smooth.
Production volumes
In order to engage in the production of such forms and parts, you must take care of installing the model-chill mold. The time required for installation is less than a week. After installation is complete, the number of products can reach from 5 to 50 pieces per hour. Such production volumes per hour are quite real, but for this it is necessary to properly prepare the casting process. The main materials required for casting are cast iron, aluminum, copper, as well as alloys of these types of metals. Another necessary material will be an alloy in which aluminum and magnesium are used.