Aspiration - the process of ventilation of industrial premises with high dust content. Such areas are equipped with special filtration equipment. In particular, gas cleaning and dust collecting plants are used . The premises of various enterprises are equipped with such equipment: from factories for the industrial production of bricks to grain processing plants. Let us further consider what dust collectors (UVP ) are.
Classification features
Ventilation dust collecting unit (UVP ) is an equipment designed for air filtration. The separation of impurities is carried out in special filters.
Depending on the mechanism of action, these elements are divided into:
- Gravity.
- Wet.
- Electric.
- Oil.
- Inertial.
- Porous.
- Combined.
- Acoustic.
- Cloth, etc.
The main types of equipment
Depending on the degree of filtration of the installation, there may be:
- Rough cleaning. The particle retention efficiency in such equipment is 40-70%. Such aggregates include large-sized cyclones, sedimentary chambers.
- Medium cleaning. They provide a particle retention of 70-90%. This category includes louver, rotary units, cyclones, etc.
- Fine cleaning. In them, the particle retention rate can reach 90-99.9%. This group includes hose, electric, roll, cell, foam aggregates, etc.
Depending on the application, the devices are divided into 2 categories. The first includes units used to filter ventilation and industrial emissions into the atmosphere, the second includes devices designed to clean flow streams, as well as air masses returned to the workshop during recycling. Businesses can use different dust collectors at the same time. The price of equipment ranges from 36 to 400 thousand rubles.
Technical and economic indicators
According to them, it is determined how effective the operation of dust removal systems at a particular enterprise is. The key technical and economic indicators include:
- Dust extraction.
- Hydraulic resistance.
- Performance.
- Dust collection efficiency (fractional and total).
- Power consumption.
- The cost of filtering.
- Maintenance costs.
Comparative characteristics
The dust removal unit is considered the simplest, the mechanism of action of which is based on gravity. As a rule, rough filtration is carried out in it. Particle capture efficiency is not more than 50%. In this case, elements larger than 50 μm are absorbed. Cyclone is a more efficient dust collector . In it, filtration is based on the use of centrifugal force. In the process of rotation, particles of substances are thrown to the walls of the unit, and then showered in a special hopper. The purified air, rotating, leaves the installation through a pipe. The filtration efficiency of cyclones today is 80-90%.
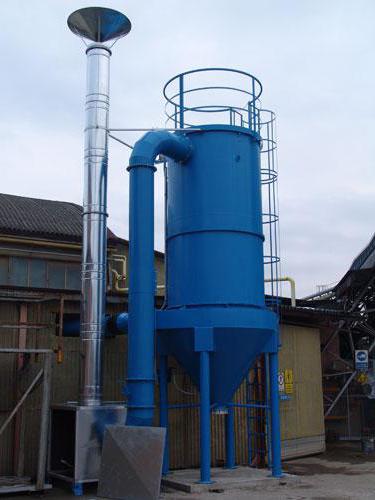
Currently, such units have a very different design. If you need to clean a large volume of air flow, several devices are combined into groups or battery cyclones are used. They are presented in the form of a large number of small units installed in one housing and placed on one hopper. The most popular today, however, are wet dust collectors. Due to contact with the liquid medium, the particles are wetted and coarsened, and then removed from the apparatus in the form of sludge. Such units can have a very different design. For example, it can be rotocyclones, disintegrators and so on.
Foam aggregates are also classified as wet plants. They supply water to the perforated grate. Filtered air also passes through it. A threshold is provided on the grill (drain partition). It allows you to save a certain thickness of the foam layer. Such a dust collector is highly efficient - up to 99%. The unit is able to filter particles larger than 15 microns. In industry, PGP-LTI and PGS-LTI devices with a productivity of 3-50 thousand m / h are produced.
Schemes
Foam dust collecting unit includes:
- Receiving box.
- Body.
- Grill.
- Threshold.
- Drain box.
The bag filter has the following design:
- Inlet pipe.
- Sleeve.
- Suspension.
- Shaking mechanism.
- Outlet pipe.
- Bunker.
The electrostatic precipitator consists of:
- Inlet pipe.
- Corona electrode.
- Filter housings (precipitation electrode).
- Outlet pipe.
- Bunker.
- Rectifier.
Mechanism of action
Hose ventilation dust collector filters the air through the fabric. It is stitched in a special way and placed in a sealed enclosure. The air to be cleaned is sucked out of the filter by the fan and emitted into the atmosphere. The sleeves are periodically cleaned using a shaking mechanism with reverse blowing. Filters can be pressure and suction types. For their manufacture, dense synthetic or natural fabric is used. The efficiency of the sleeves is 95-99%. In practice, the most common filters are FTNS, FRM, FVK.
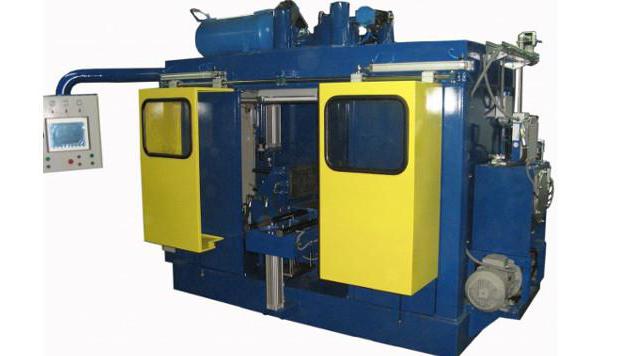
Electric appliances are widely used in the purification of industrial and ventilation emissions. The mechanism of their work is based on the following: when gas passes between two differently charged plates, ionization of the air occurs. Ions and dust particles collide, the latter receive electric charges. Under their action, they begin to move to electrodes of the opposite sign and settle there. The filtration efficiency in such devices is 99.9%. Electrical installations are considered economical to operate. They can filter flows at temperatures up to 450 degrees. However, electrical installations cannot be used to trap explosive particles.
Specific Aspiration
This process involves not only the removal of dust from the air, but also its additional cleaning. The system operates in such a way that prevents the accumulation of particles and the creation of "traffic jams". This ensures uninterrupted operation of personnel and equipment in the room. Taking into account the huge amount of waste at industrial enterprises, it can be concluded that aspiration becomes even more popular due to established health and safety standards when working in hazardous conditions.
This method differs from other methods of indoor air cleaning in that the systems are located at a certain angle. This prevents the formation of stagnant zones and localizes areas of maximum pollution. As a result, the multiplicative filtering effect is realized. The concentration of harmful compounds does not exceed permissible limits.
Chip Vacuum Cleaners
Aspiration systems are used not only in enterprises of the chemical and metallurgical industries, but also in woodworking, grinding and crushing plants. In such rooms, the installation of filtering equipment requires special knowledge, so professionals are invited to install it. The design of the aspiration system begins with the examination of the premises. Based on it, a preliminary calculation of the power and size of the equipment is made. In the furniture industry there is a huge amount of fine waste. They must be removed from the workspace without fail. For this, a chip extraction system is used. Equipment is considered a type of suction apparatus.
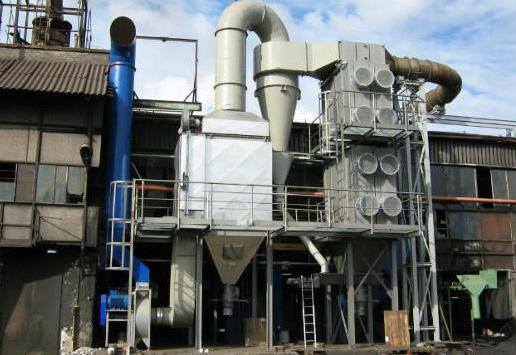
The chipbreaker can eliminate particles up to 5 microns in diameter. In the cyclone of the equipment there is a special fan and filtered bags. A separate machine is connected to a chip pump using a flexible duct system from a reinforced or corrugated pipe. The principle of operation is quite simple. The fan draws in contaminated air, which is filtered. Dust particles are collected in a bag. From there they are sent to a special filter for final cleaning. With maximum filling, the bag is removed and cleaned or replaced with a new one. Chip cleaners are easy to connect and easy to transport.
Requirements
The devices must function smoothly, reliably, with indicators corresponding to the design or obtained during commissioning activities and agreed with the developer. Gas treatment plants should be equipped with auxiliary devices and equipment. When using such units, responsible persons keep documentation. It reflects the main indicators by which the operating mode of the equipment is characterized. In particular, we are talking about a deviation from the optimal operation scheme, identified malfunctions, failure of individual devices or the entire complex as a whole, etc. All units must be registered with the State Inspectorate for Gas Treatment. At least once every six months, an inspection of the units should be carried out to assess the technical condition. This procedure is carried out by a commission appointed by the head of the enterprise.
General rules for the operation of gas cleaning and dust removal systems
It is not allowed to use technological equipment with the filtering devices turned off. In each case, turning off the cleaning device with a functioning machine, the organization’s management is obliged to notify the State Inspectorate. In this case, it is necessary to obtain an emission permit agreed by supervisory authorities.
When operating dust-collecting plants for gas filtration with a high content of explosive (combustible) elements, it is necessary to especially carefully maintain the specified pressure and airtightness of the structures, the correct purge of devices and communications to prevent ignition and explosion.