The work of welding, regardless of the technology used, is associated with the need for a rather troublesome organization of the work process. The master must prepare equipment, supplies, as well as take care of safety measures. At the same time, it is necessary to take into account the cost of the event, since financial support of such operations on a regular basis does not always justify the quality of the result. In this regard, one of the most profitable is thermite welding, which is distinguished by its simplicity of performance, the availability of materials, and in some cases allows to achieve high strength joints.
Technology features
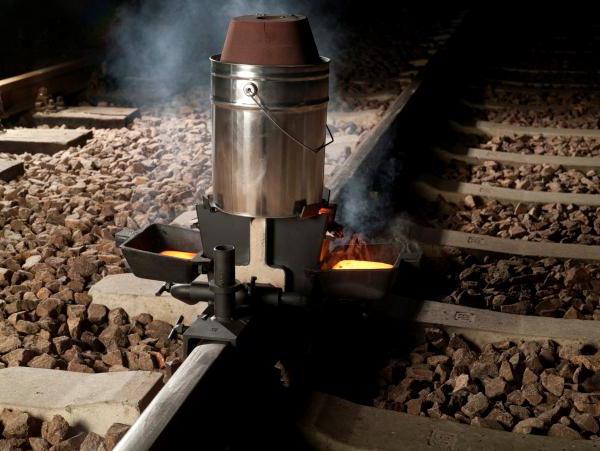
The process of welding with termites is characterized by the use of special powder mixtures, which during combustion produce a large amount of heat. As a rule, these are metal mixtures, which are called termites. The traditional combination involves the use of two components - the ignition mass and the composition from which heat is released. The oxide is iron oxide, and the main activator is termite, which contains magnesium and aluminum. In addition, the technology of thermite welding allows the use of oxides of chromium, tungsten and nickel. Thanks to these powders, an increase in thermal effect is achieved. So, if a mixture of aluminum and magnesium provides heat of the order of 2500 ° C, then the chromium compounds increase the temperature to 3500 ° C. Mixtures for fuse also vary. The most common formulation for this task is a combination of magnesium, sodium, and barium peroxide. The features of a burning termite include maintaining active heat generation even in contact with water. In other words, the mixture is almost impossible to extinguish by random exposure.
Types of thermite welding
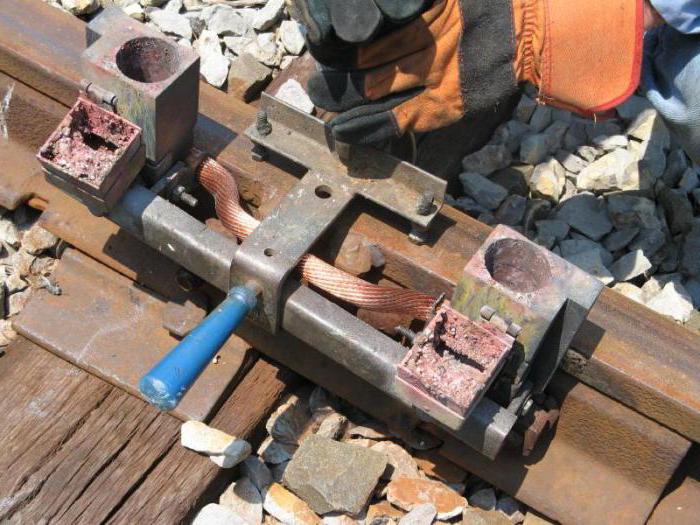
There are four main techniques for performing such welding - through intermediate casting, combined, end-to-end and duplex. In the process of performing the operation by intermediate casting, the powder mixture goes into the state of liquid metal, and this does not affect the initial characteristics of the active termite substance. Typically, this technique is used for the installation of metal structures that are pre-mounted in the desired position. Especially for working with plate products, cathode and drainage leads, butt termite welding is used, the mixture for which is preliminarily fired in a furnace. The combined technique involves a combination of the injection method and butt welding. That is, the master can carry out the main work with the help of liquid deposition, and finish the edges using delicate back-to-back welding. As for the duplex, this method provides for the introduction of an additional stage, during which the molten gap of the structure is pressed.
Applied Equipment
The basis of the equipment is a crucible, which provides the ability to work with termites, including the discharge of molten metal mass. This element can be made of ceramic or tungsten, depending on the requirements for temperature conditions. Casting molds are also prepared separately. Special matrices allow you to work with a wide range of molten base. You should also prepare equipment for thermite welding in the form of clamping and fixing devices for massive structures, a special cutter and technical pencil designed specifically for this kind of operation. Depending on the conditions of work and the requirements for the result, a special burner for the inverter and a thermometer may be required.
The practice of organizing work at home
In households, this type of welding saves those who cannot properly implement the electric arc method or gas-melt bonding. Typically, termite with a minimum temperature of about 1300 ° C is used in such cases. This mode allows you to provide the simplest aluminum composition, due to which it is possible to repair small cracks in metal structures, implement auto-metalwork operations, or weld building reinforcement. As a rule, thermite welding at home is carried out without special inverters. A termite pencil will act as a working tool, with skillful handling with which you can achieve a strong connection.
The practice of operations in an industrial environment
Industrial organization of the welding process using thermite mixtures has many significant differences. First of all, more efficient metal compositions with increased heat release are used. These are the same termites with the inclusion of chromium, tungsten and other elements with an active combustion function. For the technical organization of the process, the use of more powerful equipment is also necessary, that is, specialists are not limited to one termite pencil. For example, thermite welding in the electrical industry without fail involves the use of inverters, thermostats and other equipment that allows you to monitor the parameters of the work process. The third distinguishing feature of welding in industrial sectors is the preparation of special holding equipment. Casting refractory molds are used to fill gaps, high-strength crucibles, holders and clamps for various designs.
Features of welding wires
The technology of thermite welding is optimal for working with electrical wiring. Moreover, this approach can be used both in industry and in everyday life. In the course of the work, an all-metal connection of the wiring ends is formed. It is important to note that in the place of thickening of the wire in the welding area, the electrical resistance decreases with respect to the rest of the material. A special thermite cartridge is used for welding itself. In particular, with its help, thermite welding of wires made of aluminum and steel-aluminum is performed. There are special cartridges for working with copper wiring - they are made of chill mold.
Welding Safety
Despite the simplicity of this method of welding, it is precisely due to the specificity of the chemical properties of thermite mixtures that rather stringent safety rules are determined. First, there are special requirements for organizing the storage of metal powders. Storage should be provided only in dry and heated rooms. Moreover, thermite welding does not allow the use of wet powders directly during the ignition process. Secondly, there are special requirements for the conditions for welding. The operation can only be performed at temperatures above 10 ° C. Joints must be pre-cleaned and degreased.
Pros and cons of thermite welding
The advantages include the availability of materials, the simplicity of most operations and low power consumption during the execution of work. In other words, this option is suitable for large-scale welding of massive building structures, and for minor household operations. As for the shortcomings, thermite welding presents many difficulties in working with seamless joints. The fact is that directly during the operation, the master cannot fully monitor the quality of the formation of the gap and connection. As a result, in most cases it is not necessary to count on an even and clean reduction of parts of structures without significant deformations. But in terms of strength and durability, termite joints are considered one of the best.
Conclusion
Manufacturers of welding equipment mainly improve cutting equipment, endowing them with high performance exactly the thermal impact tool. This approach to the development of devices justifies itself, but the operation of equipment with increased power naturally requires large investments in energy supply. As the practice of termite welding in everyday life shows, the use of metal powder mixtures based on aluminum and magnesium in terms of cutting force gives the same effect as alternative methods. Another thing is that the content of these same mixtures also requires considerable troubles and costs. But these inconveniences pays off the versatility of technology. The presence in the economy of a full range of metal powders from aluminum to tungsten will allow you to create a variety of mixtures suitable for connecting railway sleepers, and for fine work with wires.