Mendeleev once said that drowning with oil was like throwing bills in a furnace. The same can be said about coal. Processing allows to reduce the burden on the environment and practically eliminates coal from sulfur-containing harmful impurities. Consider the main methods and processes of coal processing, as well as the result and products obtained from it.
Coal past
Mankind has been familiar with coal as fuel since the time of Ancient Greece. But as an independent industry, the coal industry stood out only in the 18th century. At the beginning of the 19th century, coal began to be used very actively - fuel for transport, electricity production, metallurgy, the chemical industry, automobile and shipbuilding, etc. More high-quality raw materials were required.
Coal processing methods were developed in the 20th century so that the quality of the extracted raw materials was higher. They were flawed, such as a low yield of products, a rigid framework for the implementation of the process. But with the introduction of various catalysts into the process, the yield of the product became higher, and therefore cheaper, and the passage of the process no longer required strict adherence to all conditions.
Today, coal mining and processing is a step into the future. It is carried out in five ways. The choice of method depends on which end product is needed.
Pyrolysis
This method of processing coal has been used for a long time. Back in the late 90s. In the 19th century, they knew how to heat coal without access to air, to cause the destruction of polymer molecules, with their subsequent transformation. The products of thermochemical processing are in solid, liquid and gaseous state.
Modern coking (another name for pyrolysis) is carried out at temperatures from 900 to 1100 Β° C. The product of the process is coke, which is used in the metallurgical industry, both black and non-ferrous, as well as a by-product in the form of a mixture of gases and vapors.
About 250 chemicals, including benzene, naphthalene, phenols, ammonia and heterocyclic compounds, are later recovered from the mixture obtained after coking under high temperature. The introduction of the catalyst process contributed to the formation of coke with a fine-grained internal structure - a more valuable type of marketable coke.
Semi-coking
In order to obtain fuel (liquid or gaseous) from coal by processing, low temperature coking is used at 500 Β° C. The process is also not innovative, has long been known. Previously, the goal was to obtain solid fuel from brown coal , more valuable energetically. Today, the process of coal processing by semicoking using an oxidation catalyst has increased the environmental friendliness of the final product, it has reduced the concentration of carcinogens and harmful substances. Solvents and fuels are produced from the resulting resin.
Destructive hydrogenation
This method of processing coal aims to convert solid fuel into "synthetic oil" at a temperature of 400-500 Β° C and under the influence of hydrogen. The idea of ββsuch processing appeared in the 20s of the last century. In the 1930s and 1940s, the first industrial enterprises were built on the territory of Germany and Great Britain, but in the USSR they began to use the process on an industrial scale only in the 1950s.
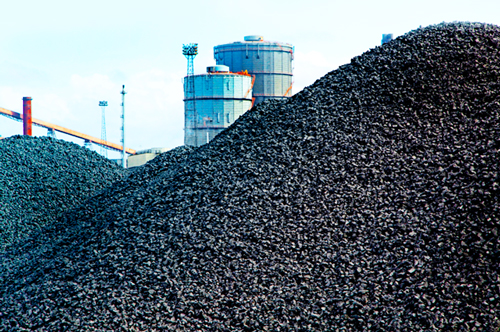
A mixture of aluminum, molybdenum and cobalt is used as catalysts in oil refining. Initially, it was also used for coal, but as it turned out, the process can be made much cheaper without loss of efficiency by using the widely distributed iron-containing ore as magnetite, pyrite or pyrrhotite as a catalyst. It was easy to calculate such a result if you knew that catalysis is proceeding indirectly. Coal passes into the liquid phase not under the influence of hydrogen molecules, but through the transfer of hydrogen atoms from organic solvent molecules to the molecules of the coal component. The catalyst is needed only to restore the solvent properties lost during the removal of hydrogen atoms.
Gasification
Under the influence of high temperatures, but in an air environment where oxygen, hydrogen, carbon dioxide and steam are present, solid coal goes into a gaseous state. This is the essence of the process. There are about 20 technologies. We will not dwell on each of them, but consider how the introduction of a catalyst can help.
In addition to increasing efficiency, it becomes possible with a catalyst to lower the temperature while maintaining the speed at the same level; it is also possible to control the final gasification product. The most common are alkali and alkaline earth metals, as well as iron, nickel and cobalt.
Plasma-chemical processing
One of the most promising, since in addition to liquid fuel from coal and brown coal, such valuable compounds as ferrosilicon, technical silicon and other silicon-containing substances are extracted which, in other methods, were simply thrown out together with ash.
What tomorrow
Considering how quickly oil and gas deposits on the earth are emptying, the fuel issue will soon become rather acute. And one of the simplest solutions will be coal mining. Scientists conduct their research work, in search of new processing processes - more efficient, inexpensive, but environmentally friendly.
Work is underway to produce "synthetic oil". In Krasnoyarsk, for example, it was tested to obtain it from a mixture of coal and water in equal proportions. The synthesis was carried out under high pressure, the processing was mechanical, electromagnetic and cavitation. Energy consumption is low - only 5 kW per ton of oil. In terms of its chemical composition, the obtained fraction is close to natural.
So do not rush to dispose of your iron horse, will feed what. And one more good news - coal is being replenished, which means it will serve humanity for a long time to come.