The machining of wood and metal blanks is still in demand in various industries. The use of turning and milling operations allows to obtain optimal results of the formation of parts while ensuring high accuracy and low costs. However, the quality of processing and the financial viability of using such methods of manufacturing materials largely depend on the equipment used. On the market, turning and milling machines are represented quite widely - in different configurations, structural and functional versions.
General information about milling and turning machines
Machines of this type are combined equipment designed to perform a wide range of operations. Separate drives are provided for both groups of technological processes. Typically, turning and milling machines are used where it is necessary to alternately produce different processing operations. As for the design, then it forms two parts. The milling department is located vertically, and the horizontal turning segment acts as a kind of base, including a bed, spindle and tailstock.
The specific design makes it possible to perform operations of various types: from shaped machining to boring holes. Also, some models include the addition of third-party functional equipment, which increases the efficiency of processing processes. For example, a wood turning and milling machine is often supplemented with bed extensions that make it possible to work with larger workpieces.
Machine tools for metal
In the traditional version, such units perform drilling, cutting and sharpening operations on metal workpieces. Provided that the power of the unit is correctly used, the material can be given almost any shape. Manufacturers of industrial equipment produce a turning and milling machine for metal with different levels of performance. Typically, low-power installations for workshops and small production lines, as well as high-performance machines for critical and large-scale processing operations, are distinguished.
Low-power models include machines with a power potential of up to 400 watts. Such equipment is characterized by a relatively modest mass and can be installed on a workbench or table. Units with a power of more than 1000 W are most often used for milling and drilling. In this version, a metal turning and milling machine can be found as part of the equipment of large plants, including those from the heavy industry segment.
Woodworking machines
Machines from this category, of course, have lower power indicators, but in terms of flexibility of operation, they outperform the units working with metal. However, most often on such equipment produce typical serial operations of cutting or milling with the creation of grooves. Also in the furniture industry, the operation of curved curly cutting. To date, turning and milling machines for wood processing are offered for both professional and semi-professional tasks. The differences between these segments are mainly reduced to the dimensions of the units and design features.
Main characteristics
Although the quality of work is largely determined by the extent to which the design and mechanics of the machine are focused on servicing specific workpieces, experts put power in the first place in technical parameters. For machines of this type on wood, the average range is 300-700 watts, and models oriented to metal processing have 400-1000 watts. In addition, it is important to consider the gap between the centers of the machine, which will determine the length of a suitable workpiece. Modern turning and milling machines are able to work with a workpiece length of about 75 cm. But again, there are types of equipment that can expand such characteristics. The value of the diameter of the processing, which can be up to 22 cm, also matters. A more in-depth analysis of technical indicators should be determined on the basis of the tasks for which the machine is selected. Depending on the operations, the future owner can also evaluate the depth of sharpening, the parameters of the cutters, the maximum dimensions of the equipment, etc.
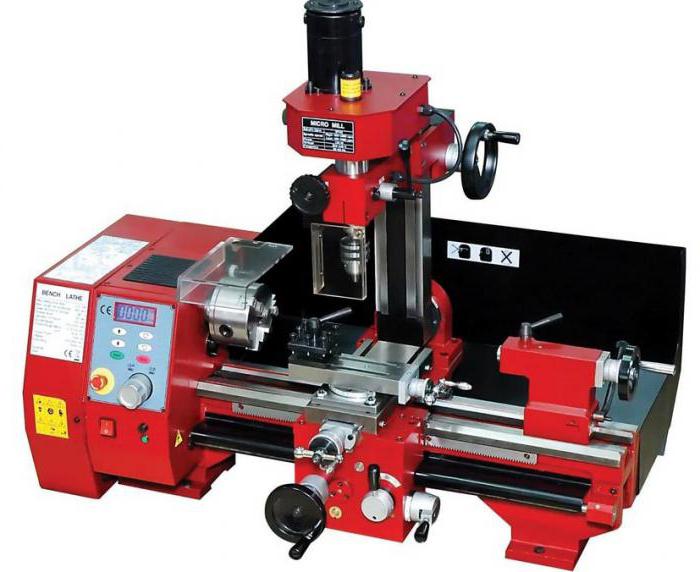
CNC Lathe Milling Machine - What is the Feature?
In fact, these are automatic machines that have the ability to perform processing without operator control. In the most advanced models of this type, the user initially sets up a processing program with certain parameters and leaves the unit to complete the tasks. The program type of control also allows for more precise settings of rotation speed, processing characteristics and other indicators. It is important to note that a CNC turning and milling machine can automatically change processing parameters depending on external conditions. Information can be received from special sensors to the control controller, for example, about temperature. And if an excess of permissible heating indicators is recorded, then the unit will either stop on its own or reduce the pace of work.
Conclusion
The variety of designs in which modern machines are presented allows them to be installed in any suitable place: from the workbench to the factory production line. Search for the desired model should be in the lines of the manufacturers Jet, Oneway, Sturm, as well as the domestic manufacturer Enkor. Specialists of these companies offer the most functional, safe and flexible milling and turning machines in operation. The price of semi-professional level models for wood processing averages 15-25 thousand rubles. And on the contrary, the professional segment of equipment designed for metal billets has about 70-100 thousand offers. However, a lot also depends on the operating parameters of a particular model, and on its configuration with functional support.