In generators, internal combustion engines, etc., plain bearings are used. These are parts that are capable of transmitting torque, ensuring the normal operation of the mechanisms. Bearings have a certain design. This provides a specific set of technical and operational characteristics of the part. Design features of sliding bearings, their varieties, advantages and disadvantages will be discussed later.
General information
Plain bearings (GOST 3189-89) are the oldest form of such parts. They are used as an element of rotating parts for transmitting translational motion. This is the main component of the shaft support, which provides the process of its rotation during the sliding of the journal on the bearing surface.
The presented detail perceives axial and radial loads that were applied to the shaft. The correct operation of the unit depends on the quality of this structural element.
There is a significant difference in rolling and plain bearings. The first of these options is characterized by the presence of such a design that provides load distribution between a plurality of rolling elements. They are enclosed inside the enclosure. The sliding bearing, however, takes up the load when sliding occurs. But in both varieties of parts, proper operation can be ensured only with high-quality lubricant.
Considering the difference in rolling and sliding bearings, it is worth noting that their cost is noticeably different. This is due to the degree of load that these parts can withstand. So, a rolling bearing is more expensive, since it can work at higher speeds. It has a more advanced design.
Plain bearings are relatively inexpensive. Moreover, it is used in many sectors of human activity. Such varieties of designs are used where the use of rolling bearings is impossible or disadvantageous:
- In products in which shafts operate under conditions of increased vibration and shock. For example, it can be internal combustion engines, hammers, rolling mills, etc.
- In the construction of large diameter shafts. It can be a system of hydroturbines, rolling mills, etc.
- In high-speed units, such as centrifuges.
- In high-precision devices, for example, the supports of the mechanisms of telescopes, microscopes, machine spindles and so on.
- In household appliances, slow-moving machines and mechanisms, devices that work in water or in an aggressive environment.
- In devices with small shaft sizes, such as watches, chronometers, etc.
Design
How is a plain bearing arranged? The main elements of its design are the housing in which the special insert is located. The manufacturing process is regulated by GOST.
The plain bearing housing can be split or solid. In the first case, to connect the base and the cover is made using bolts, screws or wedges. If the case is solid, it can be solid or welded. The choice depends on the operating conditions. Cast varieties withstand heavy loads.
Since transverse forces act on solid housings, the cover and base are provided with special coordination surfaces to extend their useful life.
The plain bearing shells can have an adjustable and unregulated clearance. The design work is provided by one or more oil-type wedges. In one-piece bearings, bushings are made in the form of bushings.
In modern units, bearings have a relatively short length. This reduces the stiffness of the shaft. Also, the clearance requirements for landing have become less stringent. It can be minimal in a short bearing. In this case, there is no danger of jamming, seizing of the moving parts of the structure during skew.
Considering how the sliding bearing is arranged, it is worth noting that short varieties of designs have some drawbacks. They finish lubrication faster. If you do not add it in time, the design will fail. But in them there will be lesser clearances. In short bearings, heat dissipation from rubbing surfaces is better. If the length is large, a self-aligning design is used. It allows you to eliminate distortions when they appear.
Construction lubrication
Considering the design of plain bearings, it is worth noting that one of the important elements is lubrication. As already mentioned, it consists of a housing and a sleeve. The supporting part of the shaft is called a trunnion. It (like the shape of the working surface of the structure) can be conical, cylindrical or flat. If the pin is at the end of the shaft, this is a spike. If it is located in the middle, this is the neck.
A mandatory structural element is a lubricator. It delivers oil or other material with the appropriate qualities to the gap formed between the shaft and the sleeve. Lubrication allows the structure to rotate with little drag. If this material runs out, the part will fail due to overheating arising from the friction process. Work surfaces will also collapse.
Lubricants can have a different look. Most often these are high viscosity grease materials. During the operation of the bearing, it heats up, becomes more fluid. This explains the qualitative sliding of the moving elements.
To increase the safety of the use of such designs, industrial bearings began to provide special lubrication. It is a solid porous material. It is a powder lubricant that is durable and of high quality. It provides a long bearing life.
This is a self-lubricating system design. It is made using powder metallurgy technology. During the operation of the bearing, oil is released from this material. They initially impregnated the solid fraction. When the system is idle, it cools down. Oil is absorbed back. So oil loss is minimized. This is especially important when operating industrial bearings. Considerable loads act on them, therefore, high requirements are put forward to the quality of the lubricant. When using a similar system on the bearing indicate that it is self-lubricating.
Varieties of designs
Considering the classification of plain bearings, it can be noted that they differ in different ways. First of all, the presented details are distinguished by structural features. They can be collapsible and non-collapsible. According to the field of application, bearings can be domestic and industrial. They differ in size, principle of operation and installation.
In addition, the bearings on sale are distinguished by the material of the housing and sleeve. As already mentioned, the lubricating composition inside the system is different. Another classification is the difference in details according to the principle of perceived load. In accordance with this characteristic, three main types of plain bearings are distinguished:
- Persistent. They perceive axial forces that are directed parallel to the axis of the journal. Such designs are often referred to as thrust bearings.
- Radial. Such designs are designed to operate under radial load conditions. In this case, a perpendicular load acts on the axle axis.
- Angular contact. Universal type of construction. They perceive both axial and radial loads.
Depending on the characteristics of the presented devices, their scope is also determined.
Manufacturer's choice
Considering the design features of plain bearings, it is worth noting that it may vary slightly depending on the approaches to production. They are made from different materials. The scope and life of the products depend on this.
Today, one of the largest domestic manufacturers of the parts presented is the Tambov Plain Bearing Plant. The most modern technologies for manufacturing structures from bimetal are used here. The company specializes in the production of plain bearings for the engines of tractors, automobiles, diesel locomotives, combines, ships, as well as for compressors of large industries. Production is carried out on modern equipment of well-known foreign companies.
The plant's products are used in the engines of such vehicles:
- GAS.
- M-412.
- WHA.
- ZAZ
- YaMZ.
- ZIL.
Also presented is a large selection of bearings for tractor engines. Bushings for crankshaft have dimensions:
- Width - 14-102 mm.
- Diameter - 24-135 mm.
- Thickness - 1.5-6.1 mm.
Actively collaborating with manufacturers of various vehicles and assemblies, the Tambov Plant is constantly improving its bearing designs. This allows you to meet the growing demands of customers.
In addition, the manufacturer in the domestic market offers a wide selection of bearings of other manufacturers, for example, Daido Metal Rus LLC, Zollern Company, etc. The presence of competition in the market leads to continuous improvement of designs, promotes the use of new materials, technologies in the manufacturing process bearings.
Advantages and disadvantages
There are a number of advantages and disadvantages of plain bearings. The positive characteristics of the design include:
- Simple design, so the cost of this variety of parts is relatively low. For lightly loaded and low-speed machines, the bearing is made in the form of a simple sleeve.
- Reliability during operation. Plain bearings are used even in high-speed drives. Moreover, their design is quite reliable, which allows you to operate such a part for a long time.
- Able to accept and withstand large dynamic loads. The design is not afraid of shock, vibration. This is due to the large area of ββthe working surface, which takes the load. The lubricant layer has a damping effect. It is located between the liner and the shaft, which also significantly extends the life of the product.
- Bearings emit low noise during operation. At any speed, the system functions almost silently.
- Radial dimensions are relatively small.
- When using detachable structures, it can be installed on the necks of shafts of complex shape, for example, a crankshaft. In this case, it is not necessary to dismantle gears, pulleys and other parts located on other trunnions.
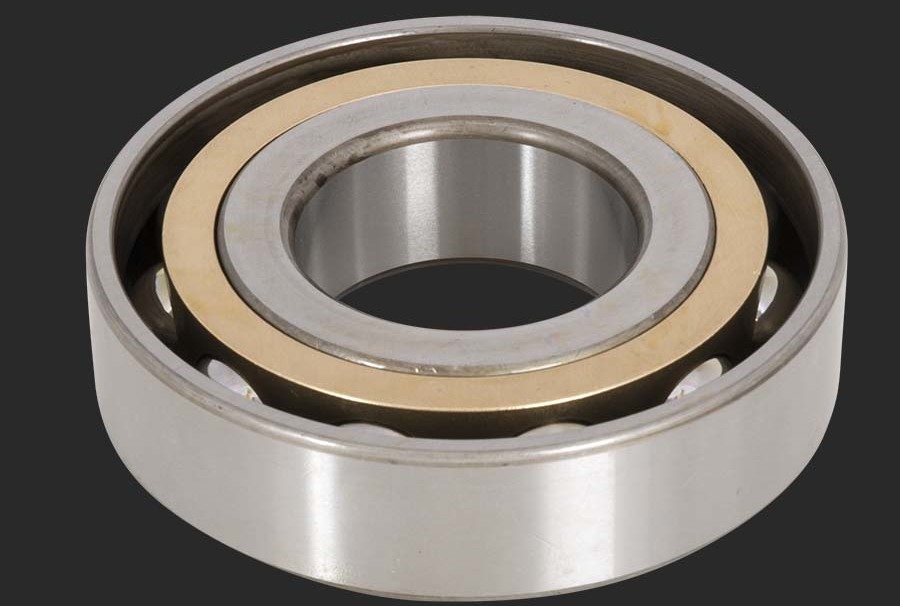
The design of plain bearings has certain disadvantages:
- During operation, the system is constantly monitored. This is explained by the need for the presence of lubricant in the design. Otherwise, the system may overheat. If the lubricant ceases to flow to the rubbing elements, it will break.
- The axial dimensions are quite large. This is necessary to increase the working area of ββthe working surface of the structure. She perceives the load.
- During start-up, significant power losses due to friction are observed. This can happen when using poor-quality or improper grease.
- Operating costs are relatively high. This is due to the need to use a large amount of lubricant. The units are also shut down to clean and cool the system. This leads to equipment downtime.
- The system during the start-up period affects the wear of the trunnion surface. This is especially noticeable when using low-quality grease.
Liner Materials
A number of specific qualities differ plain bearings. Sliding bearing materials must satisfy a number of requirements. They have to:
- Be wear-resistant and have a high resistance to seizing when improperly lubricated. This is especially noticeable during the start, acceleration and braking.
- Resistant to brittle fracture that may result from shock. Also, materials should be endowed with high fatigue resistance.
- Possess low friction.
- Have a high value of thermal conductivity.
- Characterized by a low coefficient of expansion with increasing temperature.
A bushing is a replaceable part of a plain bearing. It should be made of durable, high quality materials. It is the liners that wear out the fastest. They take on the main burden. If the axle wore out, its replacement and restoration would cost much more. Therefore, its qualities put forward increased requirements.
The harder the trunnion surface, the more reliable the mechanism. Therefore, this part of the bearing is usually hardened or hardened. Inserts can be either metallic or non-metallic. Ceramic bushings are distinguished in a separate category.
Metallic varieties of materials are bronze, babbits, alloys of aluminum, zinc, special anti-friction cast iron. The choice of material depends on the scope of the bearing, the features of its operation.
Metal liners
Plain bearings can be made from various metals and alloys. The materials of the plain bearings meet the requirements of the standards. The following metals can be used for the manufacture of bushings:
- Bronze. This type of liners is used at high loads, as well as medium speeds. The highest antifriction effect in this group is possessed by tin bronze alloys. If this metal is combined with aluminum or lead, the trunnion will wear out quickly. Therefore, such alloys are mounted only on hardened varieties of the shaft support portion. Bronze and lead alloys are used if impact loads are applied to the structure.
- Babbit alloy. It is created on the basis of tin or lead. Such material is used for the manufacture of bushings in critical structures that operate under heavy or medium loaded conditions. This is one of the best antifriction metals, as it is resistant to seizing, it is also well earned in its assembly. But its strength is low. Therefore, babbitt is poured with a thin layer on a solid base of a sleeve made of cast iron, steel or bronze.
- Cast iron. Antifriction varieties of material are used. They are suitable for use in low-speed, low-responsive mechanisms.
Cermets
Replacement part of the sliding bearing can be made of cermet. This material is made in the process of pressing and sintering of copper and iron in powder form. Graphite, lead or tin is added to the composition.
This is a porous material that is pre-saturated with molten oil. This allows the system to operate for a long time without changing the lubricant. Cermet liners are used in slow-moving machines, in places where it is difficult to lubricate.
Non-metallic liners
Bushings can be made of non-metallic materials. For this, special anti-friction plastics are used. Also for this purpose wood-laminated plastic and rubber can be used. Such varieties of liners are resistant to seizing, undemanding to lubricating compositions. They are well run in the knot. The scope of these bearings is specific. Since the system can be lubricated practically with water, this makes it possible to use the bearing in the food industry and a number of other industries.