The principle of heat exchange using heated circulating media is considered optimal for maintaining the operation of heating systems. A properly organized system of heat transfer channels requires minimal financial maintenance costs, but at the same time provides sufficient performance. An optimized design variant of such a system is a regenerative heat exchanger, which provides alternate execution of the processes of heating and cooling.
What is a heat exchanger?
The designs of modern heat exchangers provide thermal energy transfer processes with minimal losses between operating environments. The exchange most often occurs between hot fluid and cold metal surfaces, whose walls, in turn, transfer heat to another circulating medium. Constant movement provides the effect of stable mass transfer, used both in industrial enterprises and in domestic services of private houses. In addition to the energy exchange between cold and hot environments, heat exchangers can provide processes of evaporation, drying, melting and condensation with cooling. Instead of heat, cold flows can also be used as the main working medium, which is especially common in production processes where periodic cooling of equipment is required. However, it is heating tasks that are more likely associated with the designs of heat exchangers. For example, high-temperature equipment of this type can increase the thermal regime to 400-700 ° C.
Features of the regenerative heat exchanger
The design of heat exchangers at a basic level is divided into surface and mixing. In this case, we are talking about a representative of a group of surface devices, which are characterized by the fact that two active media (heated and cold flows) and a metal wall that transfer energy between the circulating masses participate in the work process. In a regenerative heat exchanger, the washing of the separating metal plate is carried out with a certain frequency, but not constantly. For comparison, we can give an example of another surface heat exchanger - recuperative. In such devices, the workflow involves the constant washing of a similar wall with cold or heated streams.
The principle of operation of the device
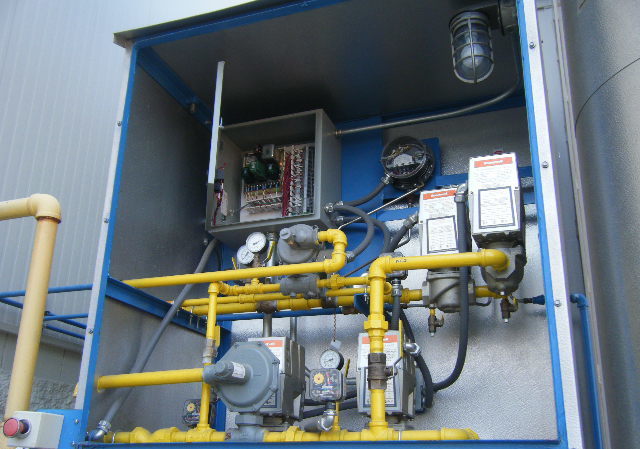
The main function of the heat exchanger is performed at the moment of contact of the active working medium with a metal plate separating the flows. That is, the key principle of action is the accumulation of energy from a liquid that currently has a different temperature than the wall of the heat exchanger. Roughly speaking, in the first cycle of work, hot streams transfer and thereby retain heat in the metal element, and in the second and final one, the cold medium already receives this heat. The accumulative principle of operation of the heat exchanger with a clear separation of the medium on the basis of temperature has significant advantages. Firstly, the absence of the need for mixing working media improves the quality of the composition of the streams. This is an important factor in the technical and operational content of communications. Secondly, the heat transfer efficiency as such is increased. On the other hand, these advantages are inextricably adjacent to the design minuses. Fundamental separation of flows increases the dimensions of the equipment, sometimes forcing to increase the pipeline segments in the old heating communication networks. In addition, ensuring the circulation function requires an increase in energy potential, which is expressed in the need to connect high-power pumping stations.
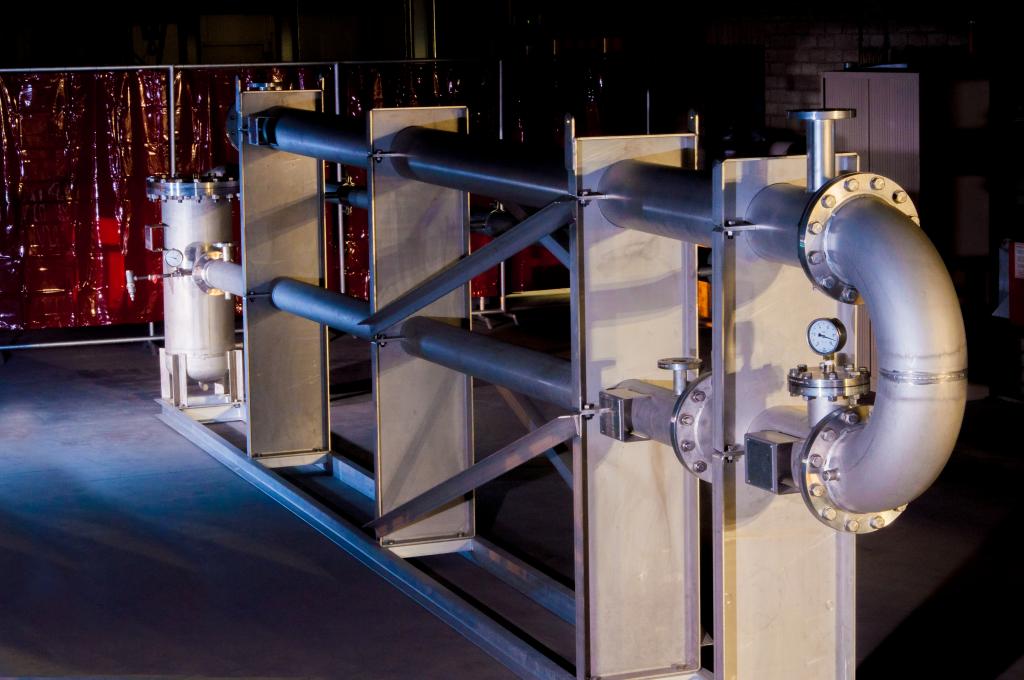
The used heat carriers
Regenerative models of heat exchangers are universal in terms of service capabilities of different working environments. As in the case with other devices for heat exchange, the most common active medium is a liquid - water or antifreeze. The heat carriers used in technological operations in production are more diverse. Water heating, gas mixtures, smoke and combustion products are used for heating and cooling. However, this does not mean at all that the same regenerative heat exchanger can support work with different coolants. In principle, the design allows such a theoretical possibility, but each instance should initially be designed for operation in contact with a certain aggressive environment, since both high temperatures and liquid as such adversely affect the metal structure.
Types of regenerative heat exchangers
There are two varieties of such aggregates. These are devices with continuous and periodic action. Continuous heat exchangers are installations with a granular circulating filler. The control system for the process of moving the working medium allows a complete stop of movement, in which the coolant will maintain contact with the surface being washed. By the way, the function of a natural automatic regulator can be performed by special thermal storage nozzles. In the design of a regenerative heat exchanger with fixed nozzles, the possibilities of flow control are limited and completely depend on the settings set by the operator. As for models with periodic action, they have a complicated distribution structure of chambers with coolants. Such a device improves the efficiency of the apparatus, but also requires a more responsible function of the power supply from the circulation pump.
Fusible core heat exchangers
One of the most advanced versions of the heat transfer regenerator at the moment, the nozzle of which is formed by a plate with an average thickness of 20 mm. In this system, there is a melting core - a device with a liquid metal inside, which during thermal periods of melting or crystallization emits thermal energy. Latent heat in regenerative heat exchangers with a movable nozzle increases the heat capacity of the circuit by a factor of ten compared to conventional units, which create favorable conditions for heat storage processes. The performance of a high-temperature heat exchanger of this type will be determined by the specific surface of the nozzle and its ability to heat accumulate.
Scope of equipment
Heat exchange units are widely used in various systems of heating equipment with boiler plants, water heaters, storage tanks, boilers, etc. This applies mainly to the private segment, but the highest technical and operational characteristics of this device are disclosed in the industry. For example, the target areas of application of the regenerative batch heat exchanger are formed by metallurgical and glass-smelting enterprises where work with very high temperatures is required. For example, the connected air heaters in such operating conditions are calculated for modes up to 1300 ° C. And again, we can talk not only about liquid media, but also about gas mixtures, which increases the safety requirements for the operation of such units.
Conclusion
The regenerative modification of the heat exchanger was developed in order to optimize a number of heat engineering processes. As a result, today, at the same industrial facilities, it is possible to carry out technological processes with minimal fuel consumption, while maintaining a high combustion temperature. But this does not mean at all that the principle of operation of a heat exchanger with an accumulative function is completely devoid of drawbacks. The weaknesses of this equipment include the limited automation capabilities of the heat engineering process, the large size and weight of the apparatus, as well as the difficulty of connecting the structure to the main production communications. Another thing is that the design of the regenerator is constantly being improved, as evidenced by the emergence of more developed models of heat exchangers with a fusible core.