The installation of pipeline networks in recent years is carried out using polymer components. If earlier plastic was used at low-responsibility facilities where minor loads on the line were assumed, today thanks to new technologies and polypropylene alloys this material is used in gas and water mains. As one of the components for such networks, an electric-welded coupling is used for low-pressure polypropylene (HDPE).
What is a PND coupling?
In their main tasks, such couplings are similar to traditional pipe fittings. Their design is carried out according to the same principles, but with some differences. First of all, the electric-welded coupling, the photo of which is presented above, is made on the basis of electric heating material with accompanying elements that provide high electrical resistance. Like the main pipeline communications, the coupling introduced into their infrastructure is made of low pressure propylene. What does this give in practice? An electric current can be supplied to the pipeline circuit with the coupling, due to which the line will be heated. That is, the electric energy in the PND material itself is converted into heat. In such conditions, welding is formed, forming a monolithic joint. Especially for electrical operations on the surface of the coupling, two terminals are provided to which the electrodes are connected.
Where is an electrowelded coupling used?
To begin with, it is worth highlighting the technical and operational properties that determined the scope of application of this hardware. Thanks to a special installation technique, the fitting provides increased strength and tightness. Low pressure propylene itself copes well with mechanical and chemical loads, so it can be used as part of large underground utilities. So, in what cases are electric-welded PND couplings used in practice? They are used to make joints between the elements of the pipeline infrastructure in the housing sector, the oil and gas mining industry, in the construction industry, in the construction of sewer and sewage channels. Again, the resistance of the material to various kinds of negative influences allows it to be used in the circuits along which chemicals are transported.
Coupling production
During the manufacturing process, the layers of composites supplemented with polypropylene copolymers are used as the main raw materials. Depending on the modification, reinforcement made of aluminum foil or fiberglass may be used. Reinforcing steel can also be used to give increased strength to the product, but this solution is rarely used for couplings. Modern production of electrically welded couplings, as a rule, is carried out in automation mode. After the manufacture of the main workpiece is completed, an automated cutting step follows with the integration of terminals and other auxiliary devices on the surface. Many large enterprises have several lines for the manufacture of couplings, each of which is designed to produce a fitting of certain sizes. More technologically advanced enterprises work with conveyors in which parameters of products can be changed. Among the most successful enterprises of this orientation in the domestic market are the companies “Mufta PRO” and “Plastitaliya”.
GOST requirements for the product
Technical and operational requirements for couplings are determined by GOST under the index 18599-2001. The following requirements are imposed on the appearance:
- Smoothness of surfaces, internal and external.
- Slight undulations of the plastic are allowed, which do not protrude.
- The color may be light yellow, orange or black.
- Extraneous inclusion in the structure is unacceptable.
As for the technical and physical properties, the product must withstand loads with a pressure of 10-13 MPa. The specific value of the allowable voltage is determined by the temperature of the medium in which the electric-welded coupling is used. GOST notes that for a temperature of 20 ° C a load of 13 MPa is allowed, and in operation at 80 ° C only products with a voltage strength with a pressure of 4-5 MPa can be used. Regardless of the conditions of use and temperature, the hardware must not be subject to deformation. The coupling must retain both the appearance and the technical parameters for a given operational period.
Coupling Dimensions
The coupling size is selected specifically for a particular pipeline. Artificial extension of its length and thickness to the initially inappropriate pipe dimensions is not allowed. The length range of sizes varies on average from 80 to 350 mm. This is the total length, and the spectrum from 40 to 160 mm determines the parameter of the area in which the electrowelded coupling will be connected. Dimensions in diameter are also diverse - from 20 to 400 mm in inner thickness. The product height is also taken into account, taking into account technological contact inclusions - it varies from 50 to 460 mm on average.
General Coupling Installation Procedure
The principal difference between electric-welded fittings is the possibility of using electric welding with controlled deformation parameters. Before starting this procedure, both the coupling itself and the target integration site are prepared. It is important to note that the shape of the pipe can be oval and simply non-circular. This is not an obstacle to the introduction of the coupling into the connection node. However, before installation, in this case, you will need to correct the configuration of the pipe to fit the fittings. Then proceed to the cleaning of surfaces and electrical work. As a rule, HDPE electric-welded couplings are installed using a special tool that implements plastic solder with current supply, heating and melt. This is the main technology for joining electrofusion fittings, but traditional mechanical fasteners are also not excluded. To do this, use integrated clamps in the design of the coupling. The joint is formed by holders that physically do not allow the two ends of the pipes to separate. But even in this case, to ensure sealing, the technique of electric-welded solder of plastics can be connected.
Preparation for installation
The site in which welding will be carried out must be protected from rain, snow and other external influences. It is also necessary to ensure the same temperature conditions for the elements being welded and the apparatus itself. In case the contact between the electrodes and the work surface with the capture of the inappropriate zone occurs during welding operations, a cleaning inventory should be prepared that will allow timely cleaning of the consequences of broken welding. For the same purpose, special solutions like Tangit are used. But it is best if the electrowelded coupling with adjacent connection sections during operation remains the only open surface - again, not counting third-party devices that protect from rain, etc. The rest of the area should be protected from direct thermal exposure.
Cleaning surfaces of connection elements
Special solvents are used to clean the surfaces of pipes and couplings immediately before welding. It is recommended to use undiluted fast-evaporating products. Degreasing wipes can be used as the application material. There are some restrictions on the use of cleaning agents for polypropylene. So, treatment with water-alcohol compounds is not allowed, since their coating can degrade the quality of the formed joint. Only future welding zone is degreased. In order for the electrowelded coupling to occupy and maintain the optimal position for the connection during welding, the contours and fixations must be marked with a marker. At the same time, its trace with ink should not fall directly into the welding zone.
Installation work
After removing from the packaging and cleaning the coupling, it must be carefully inserted into the target pipe. It is advisable not to touch the places of future welding with your hands. The element is inserted all the way and in accordance with the intended contour of the connection. If the mounting clamp is to be installed, its screws are carefully tightened already at this stage, after which it is possible to start welding. A current is supplied to the electrodes connected to the terminals from the welding machine in accordance with the load required for the melt of a particular element - these indicators are indicated in the documentation for the specific fitting. The parameters of the welding machine will depend on the size of the pipe and coupling. After the completion of the melt, the indicators on the fitting are checked. They are displayed on the screen of the device and reflect the current state of the material. Further, the installation of electric-welded couplings provides for the integration of additional clamps and fasteners. At this stage, it is important that the inclusion of the bearing fittings does not change the position of the coupling relative to the intended contours and does not exert excessive loads on the connecting node.
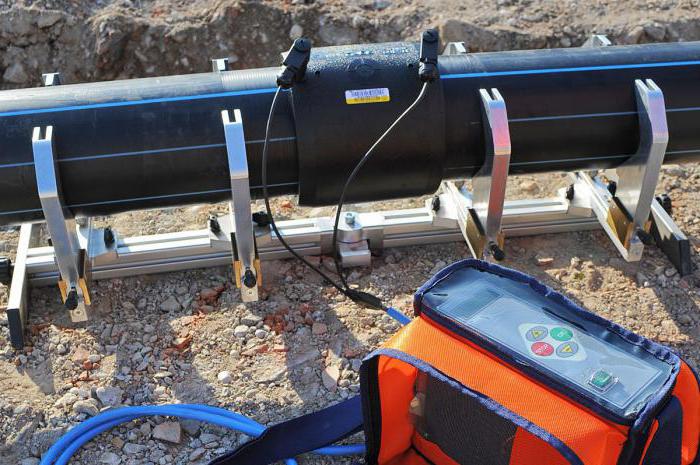
Mounted seam test methods
Non-destructive testing tools are usually used to check the quality of the weld. These can be ultrasonic and electromagnetic devices, which, by emitting a signal and receiving a reverse reaction, make it possible to evaluate the density of the internal structure of the compound. Since immediately after welding, the PND electric-welded couplings are in a state of gaining hardness, it is desirable to carry out such a check after a certain time period. It can range from several hours to a day - it depends on the characteristics of the connected elements and the parameters with which the welding machine worked.
Couplings pros and cons
The advantages of such couplings include the possibility of quick installation with a strong and reliable connection, a high degree of tightness, the versatility of the installation method and a variety of assembly configurations. Also, despite the manufacturability of the product and, to some extent, the innovativeness of the joint formation method, this option for connecting pipes is affordable both for private use and for large enterprises serving pipelines. It has an electrowelded coupling and its drawbacks. The main one is the troublesome organization of the installation process. Although the installation itself is implemented quickly and without serious forceful measures, sophisticated electrical equipment must be delivered to the junction to prepare for it.
Conclusion
The use of new modifications of polyethylene and polypropylene pipes and fittings allows to achieve a number of positive operational qualities. Among them are reliability, durability, functionality and a high degree of pipeline security. Specifically, a polyethylene electrofusion coupler makes it possible to assemble network lines in different configurations. Moreover, there are almost no restrictions on the use of this fitting in the pipeline infrastructure, depending on its purpose. Properly selected connecting fittings of this type meet the requirements for resistance to mechanical, chemical and climatic influences. Of course, in order to ensure the full range of protective qualities, the maintenance rules of the connecting unit should be followed after installation is completed.