The meaning of the activity of any manufacturing enterprise is to create a product valuable to the consumer with minimal costs that would be successful in the market. It is impossible to realize this goal without forecasting and planning the future.
It is no coincidence that the business plan provides for a special section, which describes in detail the upcoming technological and innovative processes, the tradition of quality control adopted at the enterprise, potential capabilities and actual workload of equipment, and compliance with environmental standards. This section is called the Production Plan. The achievement of all other goals, including financial ones, depends on its substantiveness and validity.
What is a production plan? How is it made up? First of all, this is a document for investors, which should convince them that the business idea is feasible and commercially attractive. It is impossible to achieve credibility without economic calculations and mathematical calculations, therefore a large number of formulas are always present in the technological section. The total capacity and planned volume of output, equipment productivity, break-even point, labor efficiency index and other indicators should be calculated. A business production plan should have the right combination of general language and specific information, as well as high readability and credibility. It is important that the investor, even without deep technological knowledge, be able to understand whether it is worth supporting the project or not. For greater clarity, charts and graphs are constructed that display the dynamics of indicators by month. In the following economic and financial sections, these data will be applied in the calculation of the most important indicators - profit, profitability, payback period, net income.
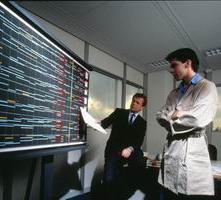
In fact, the production plan is the basis of all other sections. The information contained in it, its logical correspondence to economic calculations and calculations plays a decisive role in deciding on the financing of the project. It is good if the investor finds answers in the document to questions about what the dynamics of production will be, whether it will be necessary to open new plants, expand the equipment park, are there conditions for the normal supply of raw materials and the sale of finished products, and whether waste recycling will be applied. If the production plan is developed not for investors, but for internal use, then a different approach to its preparation is used.
The main goal here is the correct distribution of the load among individual workshops and departments, adequate loading of equipment, ensuring its coordinated work, the release of a sufficient amount of each product from the assortment without defects, with minimal costs.
When the company draws up an internal production control plan , the results of marketing research, the condition of the equipment, staffing, and available reserves are necessarily taken into account. The more factors will be taken into account in the process of compiling the program, the more likely it is to produce high-quality products that meet customer expectations and commercial success.