Copper and its alloys are used in various sectors of the economy. This metal is in demand due to its physicochemical properties, which also complicate the processing of its structure. In particular, copper welding requires the creation of special conditions, although the process is based on fairly common thermal impact technologies.
Specificity of welding workpieces made of copper
Unlike many other metals and alloys, copper products are characterized by high thermal conductivity, which necessitates an increase in the thermal power of the welding arc. At the same time, it is necessary to ensure symmetrical heat removal from the working area, which minimizes the risks of defect formation. Another disadvantage of copper is fluidity. This property becomes an obstacle in the formation of ceiling and vertical joints. With large weld pools, such operations are not possible at all. Even small amounts of work require the organization of special conditions using restrictive linings based on graphite and asbestos.

The tendency of the metal to oxidize also requires that in certain conditions, with the formation of refractory oxides, special additives such as silicon, manganese and phosphoric gels be used. Among the features of copper welding include the absorption of gases - for example, hydrogen and oxygen. If you do not select the optimal thermal exposure mode, then the seam will turn out to be of poor quality. Large pores and cracks will remain in its structure due to active interaction with the gas.
The interaction of copper with impurities
It is necessary to take into account the nature of the interaction of copper with various impurities and chemical elements as a whole because electrodes and wires of different materials are often used in the welding process of this metal. For example, aluminum can dissolve in a copper melt, increasing its anticorrosion properties and reducing oxidizability. Beryllium - increases mechanical resistance, but reduces electrical conductivity. However, specific effects will also depend on the nature of the protective environment and the temperature regime. So, welding copper at 1050 Β° C will facilitate the entry of the iron component into the structure of the workpiece with a factor of about 3.5%. But in the mode of the order of 650 Β° C, this figure will decrease to 0.15%. In this case, iron as such sharply reduces the corrosion resistance, electrical and thermal conductivity of copper, but it increases its strength. Of metals that do not affect such preforms, lead and silver can be distinguished.
The main methods of welding copper
In various configurations, all common welding methods are allowed, including manual and automatic. The choice of a particular method is determined by the requirements for the connection and the characteristics of the workpiece. Among the most productive processes can be noted electroslag and submerged arc welding. If you plan to get a high-quality seam in a single operation, then it is advisable to turn to gas technology. This approach to welding copper and its alloys at low temperature gradients creates favorable conditions for deoxidation and alloying of the workpiece. As a result, the seam is positively modified and durable. For pure copper, arc welding techniques with tungsten electrodes and protective gas media can be used. But, most often they work with copper derivatives.
What equipment is used?
Pre-copper products can be processed on turning, grinding and milling machines with the aim of forming dimensional blanks for welding. The industry also uses plasma arc cutting technology, which allows cutting with almost perfect edges. Directly welding copper is carried out by argon-arc installations, semi-automatic machines, as well as inverter devices. The current strength of the equipment can vary from 120 to 240 A, depending on the size of the workpiece. The thickness of the electrodes is usually 2.5-4 mm - again, it depends on the complexity and amount of work.
Argon welding
One of the most popular methods. In particular, the aforementioned argon-arc welding technique, which involves the use of tungsten electrodes, is used. During heating, copper interacts with oxygen, forming a dioxide coating on the surface of the workpiece. At this stage, the workpiece becomes pliable and requires the connection of a non-consumable electrode. For example, rods of the MMZ-2 brand provide optimal weld quality when welding copper with argon and protective media. If you do not have the task of severe penetration of the workpiece, then you can apply a lightweight version of welding in a nitrogen atmosphere. This is a good method of thermal exposure at low voltage indicators, but an even greater effect in terms of weld quality can be achieved using combined gases. Experienced welders, for example, often use mixtures of 75% argon.
Gas welding
In this case, an acetylene-oxygen medium is used, due to which the flame temperature increases significantly. In the working process using a gas burner. This device is good for its performance, but its limited adjustment capabilities do not allow you to finely adjust the parameters of the weld pool.
Often used and the method of divided thermal exposure with the connection of two burners. One is used to warm the working area, and the second is used directly for gas welding of the target workpiece. This approach is recommended for thick 10 mm sheets. If there is no second burner, then it is possible to perform bilateral heating along the line of the future seam. The effect is not so high-quality, but the main task is being realized.
Allows gas welding technique and the introduction of flux to obtain a clean connection structure. In particular, gaseous fluxes such as azeotropic solutions of boromethyl ether with methyl are used. Active pairs of such mixtures are sent to the torch, modifying the characteristics of the weld pool. The flame at this moment takes on a greenish tint.
Features of carbon electrode welding
An arc welding method that is best suited for copper alloys. Its main distinguishing feature is ergonomics and versatility - at least in everything that relates to the mechanics of the physical actions of the operator. For example, a welder can perform manipulations directly in the air, using a minimal set of protective aids. This is due to the fact that carbon electrodes during the heating process give off a sufficient amount of thermal energy, on which low-power copper is welded. The process turns out to be inefficient, but the connection acquires all the necessary mechanical qualities.
Manual arc welding
The technology of this welding method involves the use of coated electrodes. This means that the connection will receive decent strength characteristics, however, the composition of the product structure will ultimately differ from the primary workpiece. The specific modification parameters are determined by the properties of the alloying deoxidizers that are present in the electrode coating. For example, in the active composition, such components as low-carbon ferromanganese, fluorspar, powder aluminum, etc. can be used. This technology allows copper welding and independent manufacture of coatings. Usually, a dry mixture is used for this, which is kneaded in liquid glass. Such a coating makes the seam more dense, but the electrical conductivity of the structure is significantly reduced. The general welding process with coated electrodes is characterized by strong spatter, which is undesirable for copper.
Submerged arc welding
The flux itself for welding with copper is needed as an arc stabilizer and, most importantly, as a protective barrier against the negative effects of atmospheric air. The process is organized using non-consumable graphite or carbon electrodes, as well as with consumable rods under a ceramic flux. If coal consumables are used, then the electrodes for welding copper are sharpened to form a flat tip in the shape of a blade. Additive material from tombac or brass is also brought to the side of the working area - this is necessary for deoxidation of the weld structure.
The operation is performed on direct current with heating. Due to several protection barriers, it is possible to maintain the basic structure of the workpiece, although most often experienced welders seek to improve the composition of the material thanks to the alloy wire. And again, preventing undesirable melt flows, it is recommended to initially provide a graphite substrate, which will also act as a form for the flux. The optimum operating temperature for this method is 300-400 Β° C.
Arc welding in a protective environment
Welding activities with the connection of inverters and other semi-automatic devices are carried out in gas environments with wire feed. In this case, in addition to argon and nitrogen, helium can be used, as well as various combinations of gas mixtures. The advantages of this technique include the possibility of efficient penetration of thick billets with a high degree of preservation of the mechanical properties of the billet.
The powerful thermal effect is explained by highly efficient plasma flows in a burning gas medium, but these parameters will also be determined by the characteristics of a specific inverter model. In this case, the argon-arc welding technique for copper is more preferable in relation to workpieces with a thickness of 1-2 mm. As for the protective function of the gaseous medium, one cannot completely rely on it. There remains the risk of oxides, porosity and the negative effects of wire additives. On the other hand, an argon medium effectively protects the workpiece from oxygen exposure in air.
Conclusion
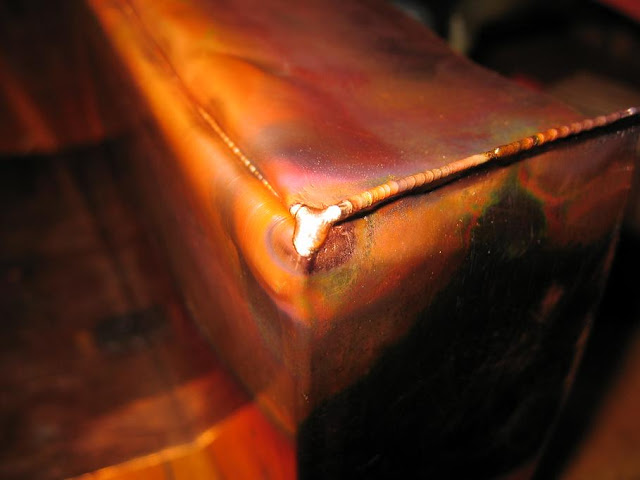
Copper has many features that distinguish it from other metals. But even within the general group of its alloys, there are many differences, which in each case necessitate the search for an individual approach to the selection of the optimal technology for the formation of a seam. For example, gas welding is suitable in cases where you need to get a strong connection in a large workpiece. However, this method is not recommended for beginners because of the high safety requirements when working with burners and gas cylinders. High-precision small-format welding operations are entrusted to convenient and productive semi-automatic machines. An inexperienced operator will be able to fully control such equipment, fully controlling the parameters of the work process. Do not forget about the importance of gaseous media. They can be used not only as a billet insulator for the duration of welding, but also as a way to increase certain technical and physical properties of the material. The same applies to electrodes, which can introduce a positive alloying effect.