How to cook stainless steel is a rather urgent issue for modern industry. It is worth noting that this type of steel is a fairly durable material, so its processing has certain nuances. The choice of welding method depends on the thickness of the workpieces, and on the chemical composition.
Stainless steel. Main characteristics
Stainless steel is an alloy of carbon and iron alloyed with chromium. The high content of the last element provides high resistance of the material in a corrosive environment. Chromium oxides form a special protective film, due to which the base metal remains stable. Additionally, steel is alloyed with nickel, cobalt, and titanium. The main advantages of stainless steel are high resistance to contact with aggressive media, high strength, respectively, and a long period of operation. In addition, steel has a good aesthetic appearance.
Features of corrosion resistant steel welding
This material has a large linear expansion. As a result, during thermal exposure, the workpieces can deform, change their sizes. To avoid this situation, it is necessary to clearly adhere to the optimal clearance between the parts that are connected. The action of high temperature can lead to the fact that alloyed steel loses its properties somewhat, corrosion resistance decreases. In this case, the weld must be cooled in a timely manner. Low thermal conductivity of steel requires a decrease in current strength of about 25%. It is also worth choosing the right welding electrodes, as overheating is possible with a long length. Another difficulty is the appearance of refractory carbides on the surface, intergranular corrosion.
Stainless Steel Cooking Methods
There are many methods for welding stainless steel. With a small metal thickness (1.5 mm), it is advisable to use arc welding (in an inert gas environment). How to cook stainless steel with a thickness of less than 0.8 mm? In this case, a pulsed arc method is used. Thin metals are also connected by an arc with a jet transfer of material. Increasingly, the plasma welding method is used. It can be used for a wide range of workpiece thicknesses. Cross sections over 10 mm are cooked under a ball of flux. They also use high frequency current welding, the laser method.
Argon welding of material
This process takes place in a protective environment of gas - argon. It protects the material from exposure to oxygen. In a special device, an arc is formed between the part and the tungsten electrode. During heating, the edges melt, a protected weld pool arises. A special wire for welding stainless steel is also constantly fed into the arc. The connection process itself is performed at an angle of 90 °. For the best quality work, it is necessary to exclude any oscillatory movements of the electrode. The result is a seam free of slag. This connection is of high quality, durability, satisfies all aesthetic needs. Stainless steel gas welding is used in many industries: chemical, food industry, automotive, aviation, heat power. Among the shortcomings, one can single out only a large investment of time on the process itself. Also, the technology requires special skills and experience from employees.
Equipment for argon arc welding
First of all, an inverter is needed for this type of metal compound. There are a lot of modifications and models: Svarog, KEMPPI Master, BRIMA, etc. The main advantages of the device are ease of operation, small size and weight, stable arc. Inverters can be used for welding almost any metal, and the joints will be of high quality. How to cook a stainless steel inverter and what to consider? First of all, you need to choose the right temperature range. Some models do not work outdoors in cold weather. It is also worth considering the power of the device. For domestic use, an inverter with a current of up to 160 A is suitable (for example, Svarog TIG 200 P, PRO TIG 200 P) The parts are cleaned and degreased before connection. For welding, a gas cylinder with argon is also required. Although in practice, the use of diluted gas is allowed. A burner is attached to the gas hose , into the holder of which a tungsten electrode is inserted. On the handle of the burner there are buttons for supplying current and gas. A welding wire of the same material as the parts to be joined is also required.
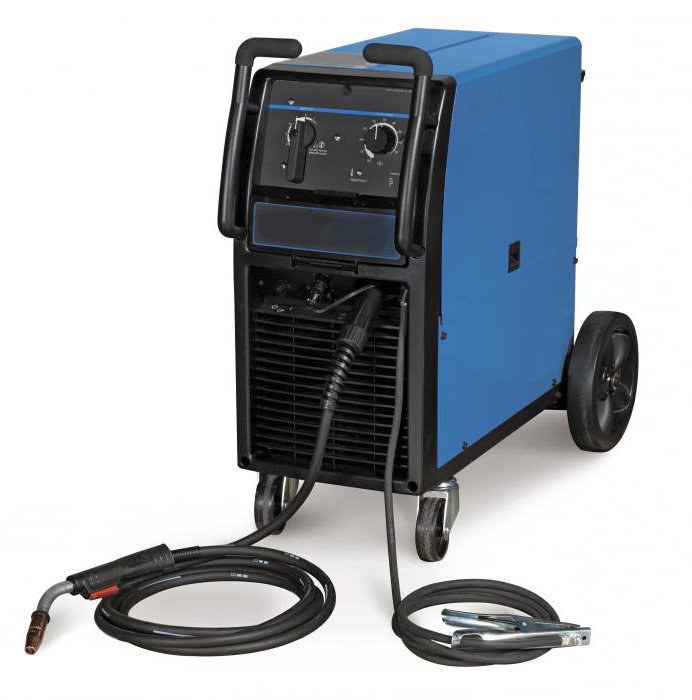
How does semi-automatic welding take place
How to cook stainless steel when repairing a car in everyday life? In this case, a semi-automatic welding method is often used. It can occur both in a protective environment and without the use of gas. Semiautomatic devices are also used at large automotive enterprises, which indicates the high quality of the welded joint. The electrode and filler material in this case is a special wire. There are several ways to work with equipment: a short arc, jet transfer, pulsed welding of a stainless steel. The technology provides for operation without protective gas, however, in this case, special powder electrodes should be chosen. This method is also suitable for working in the air. There is no need to buy (and, accordingly, spend additional funds) a gas cylinder. This has its drawback - over time, the weld may become rusty. Therefore, experts still recommend using special stainless steel electrodes and welding using argon. Today, there are many varieties of semiautomatic devices both domestic (FEB, Svarog), and foreign production (BRIMA, EWM, TRITON, etc.). The choice of apparatus depends on the tasks, the volume of welding and the characteristics of the materials being joined.
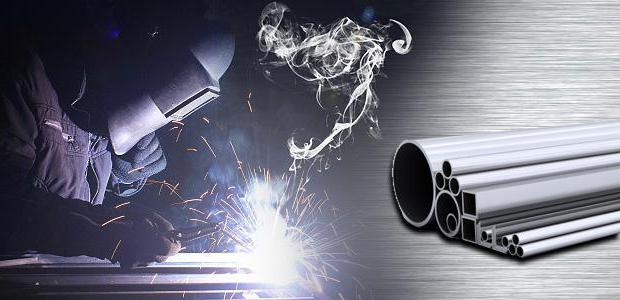
Using electrode welding
How to cook stainless steel, if there are no special requirements for the quality of the seam? As a rule, in domestic conditions, when connecting all kinds of pipes, in small-scale production, as well as to obtain a short seam, electrode welding is used. The essence of this process is the formation of compounds from the workpiece material and the metal of the electrode.
The advantages of the technique include simplicity of execution, the ability to connect different metals (both thin and rather large sections). There is no need to use gas, which reduces the cost of the process. Also, welding with electrodes makes it possible to approach hard-to-reach parts of the part. There are certain disadvantages of this technology. Firstly, the weld requires cleaning from the resulting slag. Secondly, the welding speed is small.
How to choose electrodes for welding
Stainless steel electrodes are widely used to connect corrosion-resistant alloys that operate at high temperatures. As a rule, rods are made on the basis of nickel, chromium. In manual arc welding , two types of electrodes can be used. The first - work in direct current conditions. The main coating most often consists of magnesium, calcium carbonates. Rutile-coated welding electrodes can operate with alternating current. When welding using argon, various tungsten rods are used. Due to the high operating temperature, they do not melt. There are many of their varieties. Green Electrodes (WP) are made of pure tungsten. They provide a sufficiently high arc resistance. White ones - WZ-8 - are doped with zirconium oxide. Thorium oxide is added to the red electrodes. This is the most common group, the rods are highly resistant. Also, tungsten electrodes may include lanthanum, cerium.
Weld Processing
After the process of joining parts is completed, it is necessary to clean the seam. This should be done in order to improve the appearance, extend the service life. Otherwise, corrosion may occur in this area. First of all, mechanical cleaning of the weld is carried out. The connection point looks more aesthetically after sandblasting. The next step involves grinding the surface. In this case, it is not recommended to use abrasives based on corundum, since it can provoke the appearance of corrosion. It is worth noting that all these manipulations are aimed at improving the appearance of the part. Etching and passivation will help protect the weld from damage. Etching is the surface treatment with special chemicals that destroy the resulting scale. During passivation, a special substance is applied to the junction. Under its influence, a protective film (from chromium oxide) appears.
Laser alloy welding method
One of the most modern and technological joining methods is laser welding of stainless steel.
The essence of this method is to use a laser beam as a heat source. Such welding is distinguished by high speed, high concentration of energy at the junction. The thermal effect on the zone, which is in close proximity to the seam, is negligible. Therefore, the risk of hot or cold cracking is minimal. The seam obtained as a result is notable for its strength, there is no porosity. It is also possible to deliver shielding gas to the junction of alloying elements. Since there are no welding electrodes, foreign compounds do not enter the seam. Laser welding can even be used for jewelry, since all seams are thin, neat and durable. The only drawback is that the equipment is quite expensive, so the mass application of such plants is not yet possible.