Fiber optic welding. How is she going? And what is this? It is immediately important to note here that the welding process itself does not happen the way everyone is used to.
General information
The connection of the optical fiber, or rather, it lived among themselves, is carried out due to heat treatment, passing under high temperature. Today, the development of technology has allowed to fully automate this process. It is carried out by the welding machine in automatic mode. Speaking about the welding of optical fibers, you need to understand that the whole process is carried out by an automated robot, which is equipped with an automatic control system. However, it is worth noting that the general control of the robot is still carried out by a person (operator). If we talk about the dimensions of this device, then it has an average size of 150x150x150 mm.
Welding devices
Modern devices consist of several main components.
- The first main unit is the power supply.
- The second main unit is an electronic unit, which consists of such elements as a motherboard, a voltage converter and a few more details.
- A mechanical assembly is electric drives, carriages, an optical system, etc.
The full name of this equipment is a welding machine for welding optical fibers. Further to this, most often, add the name of the company that was engaged in the production and labeling of the device.
An important detail and the main difference between each model from each other lies in the fact that each of them has its own software. The interface, on the contrary, is often almost the same and consists of such components as a monitor, keyboard and menu. Another feature that almost all devices have is the separation of the menu into two parts. The first part is called open and is intended for everyone, the second part is secret, it is intended for use only by employees of the company manufacturing these devices. Most often, this section is closed with a password, which is a combination of keys. It is worth noting that the price of welding optical fiber will fluctuate depending on what kind of actions need to be performed.
The first stages of fiber welding
If we talk about the process of welding optical fiber, then it consists of several stages:
- The first step is to cut the optical cable. By this we mean the following operations: removal of the outer shell, removal of the inner shells (there are usually two of them, for better cable protection). In order to remove the outer shell most often use a special tool. If the cable is divided into several modules, then the coating from each individually is removed by a stripper.
- Purification of fiber from a hydrophobic type material. Quite often, in order to keep the fiber intact, a hydrophobic type filler is used. For these purposes, a colorless gel is used. To remove it, a special D-Gel solvent is used.
Continuation of work
The welding of optical fibers after the completion of the first two preliminary stages proceeds as follows:
- On the fibers of one of the cables, you need to wear such a thing as KDZS. These are special sleeves - a kit for protecting joints. This kit consists of two heat shrink tubes, as well as a power rod.
- Using a stripper, it is necessary to remove the protective gel from the ends of the optical fiber (approximately 2-3 cm from the end). Before proceeding to chipping, you need to wipe the cleaned ends with alcohol.
- After all the preparatory procedures, you can proceed to cleaving. To carry out this operation, you must have a precision cleaver. If we talk about the cleavage plane, then it should be exactly perpendicular to the axis of the fiber itself. The maximum deviation allowed for each chip is 1.5%.
- To start the process of welding optical fibers, it is necessary to place peeled and chipped fibers in the clamps of the welding machine. The clamps of the equipment are V-shaped ditches that hold and feed the fiber during welding.
The main stages of welding
The cost of welding an optical fiber is quite large, and therefore it is better not to be mistaken during operation, especially in the next stages.
- The first main stage of welding is alignment. By this concept is meant the process of connecting optical fibers to each other. This will require a microscope, and the process itself is carried out at the expense of motors. If we talk about modern devices for welding, then they perform this operation in automatic mode.
- Next, an electric arc comes into play, which heats the ends of the fibers to the desired temperature, while leaving a micro-gap between them. The process of connecting the fibers is rather slow. The ends of the product are combined using the motors of the holder.
- A rather big plus in using the apparatus for welding optical fibers is that it itself estimates the attenuation at the weld site. In addition, it automatically checks the quality of the fiber connection through mechanical influence. In other words, he independently conducts a tensile test.
- An important nuance. Before starting welding, one of the ends is worn with a CDS. After the procedure is completed, the sleeve is manually moved by the operator to the place of work. In this form, the cable must be placed in a heat chamber, in which the thermo-shrinkage of the sleeve will take place.
- The last stage is the laying in the splice cassette of an optical coupler or cross, welded and seated fibers.

Considering the whole process of work, it becomes clear why the cost of welding optical fiber is quite large.
Spikeer equipment
Fusion splicer fusion splicers are some of the most expensive devices a splicer can have. The high cost of this equipment lies in the fact that the device takes care of all the operations of welding the optical fiber. All that remains for the person (operator) is to prepare the cables, put them in the machine, and then get it out, put on the sleeve and place it in the heat chamber.
Getting started and aggregate summary
An optical fiber splicer operates according to the following principle:
- To get started, you will need to lay the peeled and cleaved fibers in the equipment. It is important not to forget to put on the sleeve in advance.
- Next, you need to press the button (if the process does not start automatically) and the device will begin to reduce the ends of the fibers until they see them in the optical system. It consists of microscope cameras and several mirrors.
- At the moment when both ends are in the field of view of the system, the device delivers a weak electric arc. The main purpose of the arc is to blow away microparticles that remain on the surface, despite any, the most thorough wiping. Also, some believe that it slightly melts the ends, thereby preparing for welding. However, it is important to know that if at least a drop of gel, fat from fingers or any other element of a similar type remains on the fibers, then due to the influence of the arc it will be baked, and so that it will not be possible to remove it, you will have to redo the chip.
- In the event that all chips are clean and good, the summarization process will begin, in which precision motors are involved. If something is wrong with the soldering elements, the device will notify the operator of this by a signal, a message on the screen, and the summary process will not start.
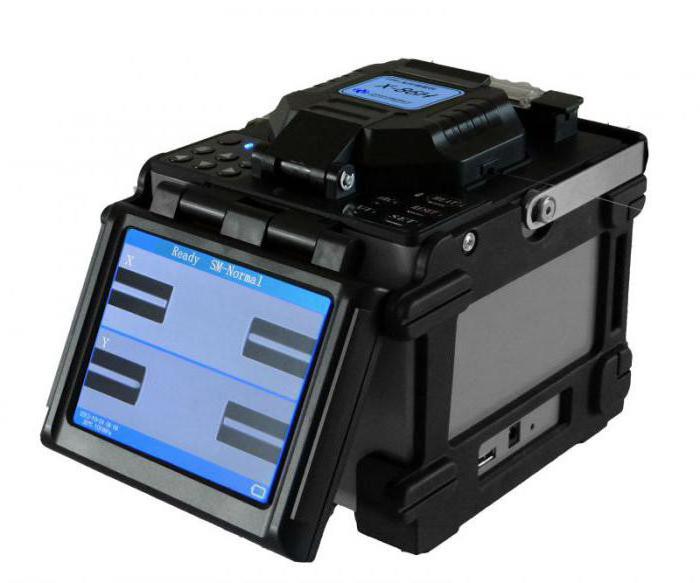
Unit welding principle
After completion of preparation and mixing of fibers, a direct cooking process occurs.
- Both ends of the cable come close to each other. When the motors are turned off, the main electric arc of high power enters into operation, which heats and melts the ends of the fibers in a second or two. When the arc turns off, the motors finish the ends, soldering them together. It is worth noting that the place of work of the arc, that is, the place of welding, cools almost instantly.
- The device also automatically checks the quality of welding for clearance. If the seam is good, then it should hardly be visible. Also, this equipment saves such indicators as the date, time and attenuation of each conducted process. In this case, the welding counter is increased by one unit. It is impossible to reset it.
- As mentioned earlier, the unit independently conducts a tensile test, however, when training in the welding of optical fibers, experts recommend turning it off, since it can ruin the still-cooled welding.
The last stages are putting the sleeve on the place where the welding was, and putting the cable into the heat furnace.
Manufacturers and prices
Today, we can say that of the most common models are devices from Fujikura, Sumitomo. These companies are Japanese manufacturers. The second place is occupied by the Chinese company Jilong. If we talk about distribution in the territory of the Russian Federation, then Fujikura is in greatest demand.
The price of an apparatus for welding optical fibers, which can be used for welding the most important lines, ranges from 120-130 thousand rubles to 300-350 thousand rubles. Lower cost for sets of the Chinese manufacturer. The most expensive were the units of the Japanese manufacturer.
Optical fiber welding rates
If we talk about the cost of fiber welding services, then you need to know what kind of work is included in the cost. Most often, their list is as follows:
- cable cutting and cleaning;
- welding;
- cassette assembly and fiber laying;
- expendable materials.
These are standard operations that are performed in any case. Further, the separation of the cost of welding optical fiber occurs from the number of cores in the cable. If you want to carry out work with a quantity of 32 cores, then for the connection of 1 fiber will have to pay about 250 rubles. If the total volume is in the range from 1 to 32 fibers, then the cost for connecting each will be 300 rubles. There are smaller limits, for example, from 1 to 8 fibers will cost 500 rubles for each core. From 9 to 16 - 450 rubles. It is important to understand that the cost of welding optical fiber is average and each office has its own policy for evaluating services.