Soft roofing is a practical, inexpensive and technologically feasible solution for decorating roofs. They perform both the basic tasks of the insulator and the protective functions, protecting the structural elements. There are many options for such flooring, but the most popular is the roll roof, characterized by an elastic structure. It also has different designs, differing in performance, size and purpose.
Roofing Cake Structure
Classic roofing involves the creation of a rigid frame on the surface of the prepared rafter structure. The bearing base is formed by beams and laths made of wood or metal. Supporting elements can be constructed from concrete racks on which the rafters fit. What place in this system will take the roll roof device? This coating is rarely used in private construction and at least requires the preparation of a flat surface. Typically, such floorings are used in the arrangement of industrial, public and multi-storey private buildings.
Roofing provides protection of the concrete platform of the roof, the task of sealing, isolation from moisture and insulation is solved. For this, substrates are formed, furniture protective elements are arranged, and putties with adhesive solutions are also used. In this regard, a flat roll roof is good because it easily covers large areas, requiring minimal financial costs and physical effort.
In the structure of pitched structures of private houses, this type of roof is also used, but not in all types. This can be a traditional roofing material or bitumen flooring, which creates a protective and insulating coating on a previously created substrate. As for the upper part of the βpieβ, it, depending on the type of roof chosen, can be represented by additional processing based on plasticizers, sealants and protective paint and varnish mixtures.
Operational properties of roll roofing
The roof must have reliable protection against mechanical damage, the penetration of cold, wind, rain and moisture. Soft roofing is not ideal as a complete solution - in particular, they are not able to provide the same structural tasks as hard coatings like tiles or metal profiles. In this case, the isolating function will be the main one. Due to their elasticity and strength, rolled roofing materials cover the roof surface with the capture of complex sections. As a result, bridges of cold are completely excluded, noise and waterproofing are increased.
Particular attention should be paid to a small mass. Again, in comparison with traditional hard coatings, soft flooring gives a minimum load on the rough basis - even thick roll materials with several protective layers weigh about 200-300 g per 1 m2.
The only drawback is related to environmental qualities. Chemically unsafe components can be used as part of a roll roof. This factor should be especially taken into account when using the coating in the southern regions, where sunlight can provoke melting of the material with the release of toxic substances. But these qualities do not apply to all rolled coatings, as manufacturers tend to use βcleanβ components, thus expanding the scope of use of the final product.
Types of Basics
Rolled roof coverings can have their own supporting frame, and sometimes they can be done without it. Baseless materials, as a compensation layer, receive buildup of binders and the inclusion of special fillers that make the structure tougher. As a rule, this is a soft roll roof with treatment with astringent organic mixtures. In other cases, a special base, frame or substrate, which acts as a protective support base, is used.
One of the most popular materials performing the task of the base is fiberglass. Its wide distribution is determined by its affordable price and versatility in terms of laying possibilities. But you should not count on the increased technical and physical qualities of fiberglass. If it is precisely the requirements for strength and reliability that come to the fore, then the device of a rolled roof based on fiberglass, which in terms of structural rigidity surpasses fiberglass several times, will be more advantageous.
The base is also made of polyester materials. In terms of strength, they correspond to fiberglass, but at the same time they are distinguished by their elasticity and reliable coupling with roofing impregnations, which increases the sealing effect. In rare cases, the substrate is represented by foil, cardboard and asbestos fibers, but these are specific budget solutions that have a narrow scope.
Types of Binder
The next and main layer in the structure of the roll coating, which determines the "working" or functional qualities of the material. In most cases, the core of the canvases is bitumen in various versions. In pure form, such mixtures (as before tar) are rarely used. Mostly, these are combinations with polymer additives that provide thermal stability to the coating, the same elasticity, sealing, etc.
So, it is worth starting the consideration of binders with the so-called artificial rubber. This is a combined mixture of styrene-butadiene-styrene, the heat resistance of which reaches 100%. This option is noteworthy if you plan to lay the roll coating on the roof with a separate substrate. Ready flooring can withstand shock loads, optimally adhere to the surface and maintain tightness.
Another type of roof on a bitumen-polymer basis is an atactic thermoplastic canvas. In addition to the insulation function, this coating is characterized by resistance to infrared and ultraviolet radiation. High elasticity is out of the question, but resistance to cyclic loads makes atactic coatings a worthy choice for roofs of industrial and public buildings.
Tiled roll roofing
On the one hand, this is a transitional class of coatings that combines the qualities of a traditional flexible roof, and on the other hand, it is a hard roll cover, which also demonstrates the properties of strength and elasticity. Such floorings are used on pitched roofs when installing a single-layer roofing on a solid wooden flooring. The slope angle can be from 3 Β° or more. In other words, if soft roofs are used mainly on flat roofs for industrial use, then, provided you create a strong wooden plank, tile tiles can be laid on private houses.
Actually, why is this type of roof called tiled? This is an exclusively decorative accent in the form of a picture imitating the classic "brick" texture of the roof. At the same time, piece roll roofing, produced in the form of additional and sheet elements, shows a reverse example. In their format, they resemble tiles, and the structure of the material comes from the same soft roof with some strengthening of the binder. In choosing a tiled coating, it is necessary to take into account the increase in mass (up to 4-5 kg ββ/ m2) and the use of protective and decorative layers. The front side is usually covered with coarse-grained colored sprinkles of basalt, which creates the illusion of a real tiled or brick coating with a pronounced texture.
Surfaced roll roofing
A modern variety of soft roofing, which can also be used as a standalone waterproofing. The targets are buildings of various enterprises and, more importantly, engineering structures like tunnels, bridges and foundations.
The structure of a soft roll roof of this type is represented by the bitumen-polymer components discussed above - in fact, artificial plastic that is resistant to biological destruction processes, climatic and mechanical stresses.
The principal feature of surfaced coatings is the laying method. Roll materials, depending on the type, can be fixed with fasteners, glue or clamping devices, followed by sealing joints. In turn, roofs from surfaced roll materials are laid by the method of adhesion under thermal influence. However, this technique deserves a separate discussion.
Mounting technology
At the first stage, the preparation of the basis for future styling is carried out. A feature of soft roofing canvases is their increased sensitivity to the properties of the bearing surface - especially if it comes to roofing without a foundation. Preparatory measures will include cleaning the working area, removing dirt, degreasing and leveling. As for the permissibility of installation on different types of surfaces, concrete, metal and wooden floors can act as a base.
Laying of a roll roof is usually carried out using primers - these are bituminous weldable mixtures, which, under the action of high temperature, acquire a fluid state, and after hardening fasten bonded materials. As a working tool, a construction knife for cutting the blade, a marking tool and a gas burner, which will be welded, are prepared.
The most crucial stage is the direct laying and joining of the unfolded roll sheets. Each segment is heated with a primer mixture in the temperature regime specified by the instruction for a specific material. The flame is directed along the bottom surface of the roll. As a result, the bitumen roller should reach the edges of the cutting blade, which will allow high-quality gluing of the material. Depending on the slope of the roof, the installation of the roll roof is carried out in one or two layers. As a rule, on steep slopes, one- and two-layer βpiesβ are used, and flat roofs are the most demanding in terms of mechanical protection, so they should be enclosed in three layers.
Maintenance and repair of coating
Immediately after the completion of installation operations, the first audit of the coating is carried out, which will identify weak or simply unsuitable for operation areas. This is usually done "by eye". Roofer inspects suspicious places, posing as swellings, dents, stretch marks and other signs of defects. If such signs are found, it is necessary to repair the roll roof, for which a small supply of a similar canvas, primer and gas burner are initially prepared.
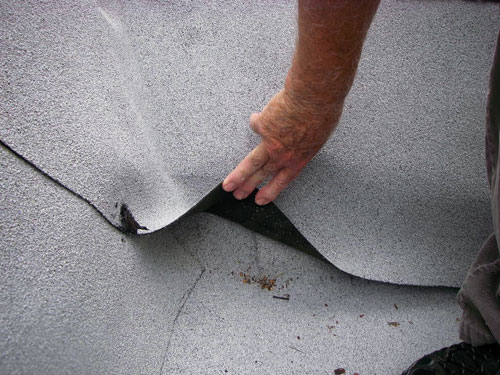
When repairing, the cutting of the site is primarily performed. A small cutout is made with a mounting knife , under which an empty, non-glued niche opens. It is the empty areas without bitumen fixation that will be the target point of view of recovery. After determining the parameters of the empty area, a canvas is cut along its edges. Next, a primer is applied to the area, after which the patch is laid with the burner. Moreover, its size should be such that the material in addition to the open zone also captures an additional 10-15 cm at the edges.
In case of renewal of the roofing, dismantling operations may be required. One of the disadvantages of the same fused web is the complexity of its elimination. In the process of dismantling, one can not do without the binder melt, on which the coating was laid. As the docking places are heated up by the burner, the roll roof is phased disassembled, including using a special tool. Professional roofers use for cutting in difficult areas stroboreza, but you can do without cutting the flooring with an ordinary ax. The material collected in this way is discarded; it cannot be used in the future.
Roof manufacturers
The initial level of coatings is represented by Izolyuks products. This is ruberoid material worth about 200-300 rubles. per 15 meter roll. This flooring, in addition to an affordable price tag, is praised for its universal set of insulating and protective properties, sufficient tensile strength and durability. But for a private house, this option is hardly suitable because of environmental insecurity and the difficulty of laying on a pitched roof.
In all senses, the universal solution will be the Technonikol coating. The company offers soft and flexible flooring, characterized by users as durable, aesthetically attractive and easy to maintain. A worthy insulation function and sound insulation are separately noted. At the same time, the Technonikol roll roof costs an average of 500 to 1200 rubles per roll.
Another popular roofing manufacturer is Ruflex. In terms of cost, the products of this company correspond to the analogues of Technonikol, and the users themselves note special accents on the decorative properties of such coatings. Suffice it to say that the assortment contains a wide range of specialized models for decorating roofs with attics, for asymmetric structures, options in eco-style, etc.
Conclusion
This is not to say that rolled floorings completely replaced the rigid traditional roof. The most problematic segment for promoting soft coating is considered the private sector. Mostly roofing materials manufacturers are fighting for it , improving manufacturing technology. The problem with the construction of a roof made of rolled materials as applied to a suburban cottage, for example, is that it is more likely to serve as an insulator substrate. But the roof will require additional physical reinforcement in the form of a boardwalk or protection from a metal profile. In extreme cases, you can initially select models with improved protection in the basic structure. As for the use of this type of roof in industry and multi-story construction, in view of the presence of a solid concrete base in such buildings, only one function of the insulator will be laid on soft flooring. And it is quite enough for the successful operation of a flat roof.